Q. We have some southern pine beams from a building constructed around 1870. The ring spacing is easily 20 and more rings per inch of diameter — very, very slow growth indeed. We estimate, by counting the rings, that the trees were growing before 1800. How can we prove that they are heart pine?
A. Wood that can be identified as heart pine (sometimes spelled heartpine) is extremely valuable. However, visual and microscopic examination will not confirm that these beams are from longleaf southern pine, referred to as heart pine. The wood from the four southern pine species is not different enough to allow separation by looking at the wood alone.
However, we do know that around 1800, longleaf pine dominated the Southern states. Due to the high density of the trees in the forest resulting in many rings per inch, due to their old age when the beams were installed in the 1870s, and due to the common use of longleaf pine for beams due to its high strength, it is extremely likely that these are heart pine. I would hope that people wanting heart pine for historic restoration would be satisfied with this evidence. It is all we have.
As it is likely that the beams were manufactured locally (because transportation over long distances would be difficult and expensive), perhaps the state forestry office has some records of the past species and sawmill activity nearby. This could help strengthen the identification.
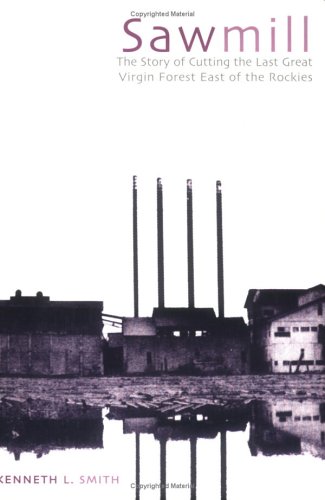
There is a very interesting and enjoyable book about the cutting of the last virgin southern pine forest: “Sawmill: The Story of Cutting the Last Great Virgin Forest East of the Rockies” by Kenneth L. Smith. The book was published in 1986, but the book is still available from Amazon.
Q. I have taken over the management of the purchasing, grading and drying operation at our factory. I am convinced by my experience so far and your writing in FDMC, that moisture content of the wood going into our rough mill is an important quality factor. So, I am looking at an in-line moisture meter. The cost is so high that I am having trouble justifying the meter. Can you provide any guidance or direction? Thanks.
A. It is good to hear that you believe that the MC of lumber coming into the plant is important. Incorrect MC can causing gluing, machining, and finishing issues, plus subsequent warping and other defects that the consumer finds. Consumer repairs are certainly expensive. I suspect every manufacturer, when pricing furniture, cabinets and so on has to include the cost of “consumer problems” in the cost.
My experience is that at least half of the consumer issues can be eliminated by proper MC of the lumber. (A quick case story that I worked on: A door manufacturer in the Midwest had about 100 complaints every winter. They put in an in-line meter, eliminated wetter pieces of lumber, and the next winter complaints dropped to three!)
Indeed, an in-line moisture meter can be set for the species and thickness you are running. Pieces that are too dry (never should happen with the correct drying procedures) or too wet can be pulled out of production for re-drying.
The big question for you: “Is removal of the wet pieces worth $25,000 to $30,000?” Indeed, if the machine works for 10 years, then the question is, “Will eliminating the wet pieces save $3,000 or more per year?” The answer is not overwhelming for most older operations that are used to incorporating the cost of recalls into the price of a finished product.
So, let me suggest a second benefit. What if you related the in-line MC values to location of the lumber in the kiln, to air drying time, to species, to thickness and to a specific kiln (if you have more than one kiln)? The answer is you will begin to develop a moisture profile related to these variables. With this knowledge, you will see which kiln is not up to top performance and where kiln operational factors such as a schedule need improvement.
You will see relationships to air drying times and locations. You will also see opportunities for better moisture sampling in the kiln.
In short, the MC data will give superior guidance to management. In short, this in-line MC measurement serves as a “drying detective” for management to shorten drying time without compromising on final moisture content values.
An important financial factor is that a savings of one day in kiln drying time in a 50 MBF kiln saves about $1,000. A one-day savings in 30 loads, even if it takes several years to accomplish this savings, will pay for the in-line equipment, with the reduction in consumer complaints an added benefit.
Hints: Appreciate that a mill checking final MC for the same softwood species, like southern pine, and the same thickness material, like 2” thickness, has an easier job than running hardwood lumber with species and thickness variations.
Plus, the MC specs for hardwood lumber usually allow only a small variation in MC for hardwoods, compared to a several times larger variation for softwoods. Therefore, I do suggest that you visit an operation using the in-line meter you are thinking of buying, making sure this operation is testing many of the same species you will be running.
Make sure the data entry system for kiln location, air drying time, incoming MC, and so on is easy and straight forward, so operators can be quickly trained. I prefer a system that uses one sensor and scans the lumber lengthwise; a second option is to use three or four sensors and scan three or four spots across the lumber. One sensor is easier to maintain.
Have something to say? Share your thoughts with us in the comments below.