Some wag once said, “If all you have is a hammer, everything looks like a nail.” That’s not wrong. We are prisoners of our tools and obtained skills. How we work, what we make, and how we make it are all wrapped up in what tools we have available.
I’ve been thinking a lot about this over the last few months as I continue my journey in learning CNC manufacturing firsthand. I keep running up against limits based on my own knowledge, the capabilities of my machine, and the different kinds of software I can use, and, oh, yes, how much time and treasure I’m willing to invest to break out of those limitations.
Think about it in your own shop. What projects do you avoid because you don’t have the right equipment or skills? Look at it another way. Have you ever bought a new machine, new software, or spent time to learn a new skill just so you could take on a special project?
Shops full of conventional equipment tend to do more work in solid wood. Shops with CNC routers and edgebanders do panel processing and mostly eschew solid wood. The accomplished finish carpenter who aspires to build cabinets dreams of a shop full of big stationary machines that he could never have on the job site. The cabinet shop that is getting into closets might lust after a beam saw to crank out all of those shelves. Edgebanding is a huge challenge for any shop until they get their first quality edgebander. The list goes on.
In my CNC journey, I knew from the get-go that I would face limits based on my space, my machine, and the software that came with it. Some of those limitations can be pushed. Dovetails are a great example. If you want to do dovetails or box joints, it traditionally requires applying joinery to the ends of boards. Router jigs and purpose-built dovetail machines do that with ease. It’s not so easy on a CNC router designed primarily to machine the faces of boards or panels.
A number of creative machinery and tooling suppliers have introduced solutions for this. Most require special bits and make a joint that does not have the crisp corners of a traditional dovetail or box joint. My solution, which I learned in my own CNC Bootcamp last year at AWFS, was to cut a slot in the table of my CNC router to allow dropping boards down so their ends could be machined. It worked great.
I’ve also encountered software challenges that have forced me to do workarounds and use multiple kinds of software to accomplish challenging tasks. When it comes down to it, I guess it really is about having the right tool for the job as well as learning how to use it properly. But sometimes focusing only on the limits of existing tools makes you blind to the possibilities. What can your existing tools really do? Are you sure you have reached the limits of their capabilities? Of course, maybe buying that shiny new machine is indeed the solution.
You don’t have just one hammer and just one nail to deal with.
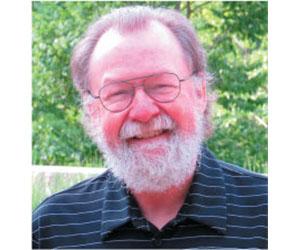
Have something to say? Share your thoughts with us in the comments below.