The FlexStore storage and retrieval systems are in the plant’s center, feeding multiple product lines.
Cabinet doors for the Thermofoil Series are shaped on a series of six Morbidelli CNC routers.
The company has two IMA edgebanders on site, including a "true" laser bander.
Two Wemhoner presses are on site for the company’s 3D and flat panel lamination requirements.
Corona Millworks offers dovetail and dowel drawers with standard, angled or scalloped sides.
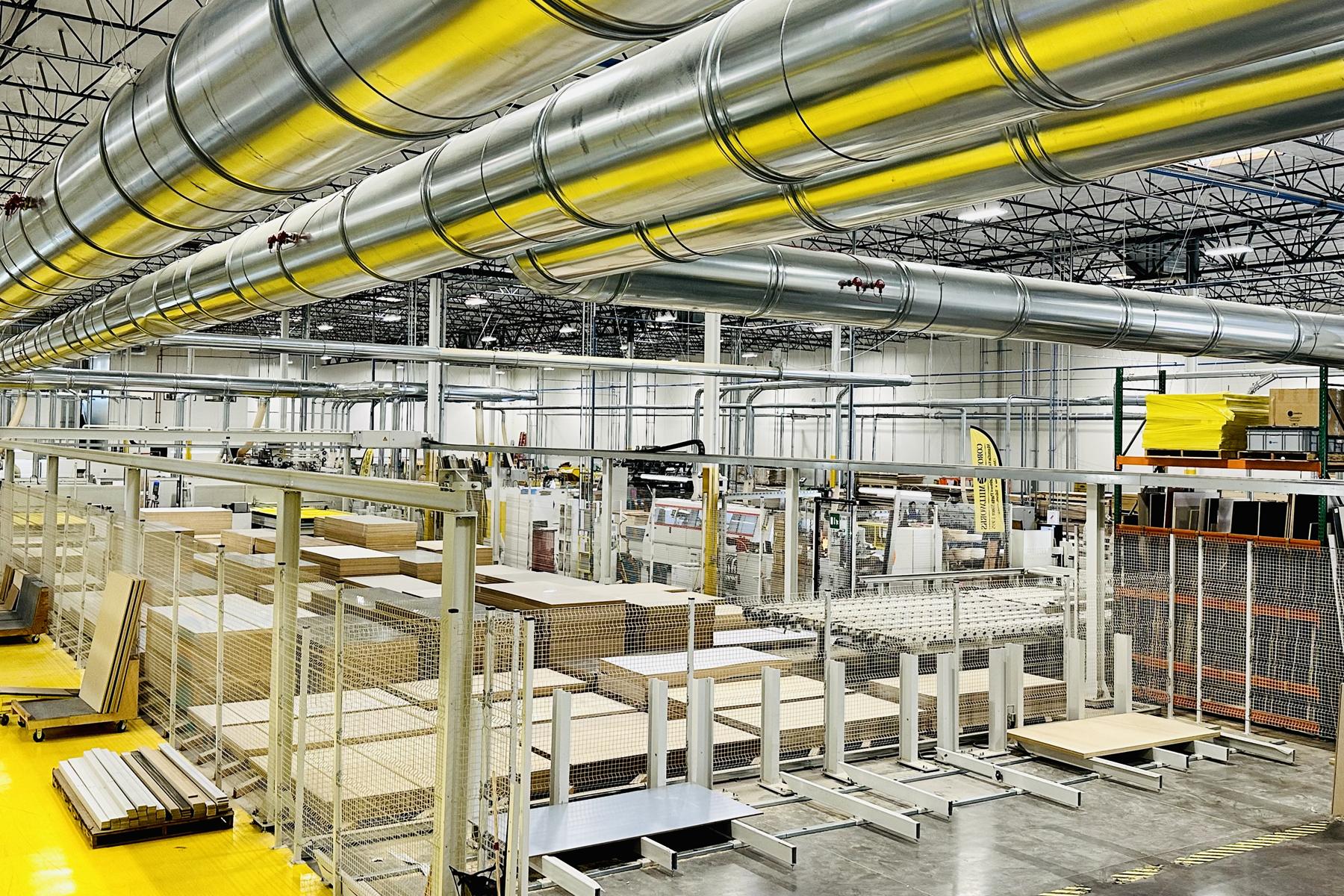
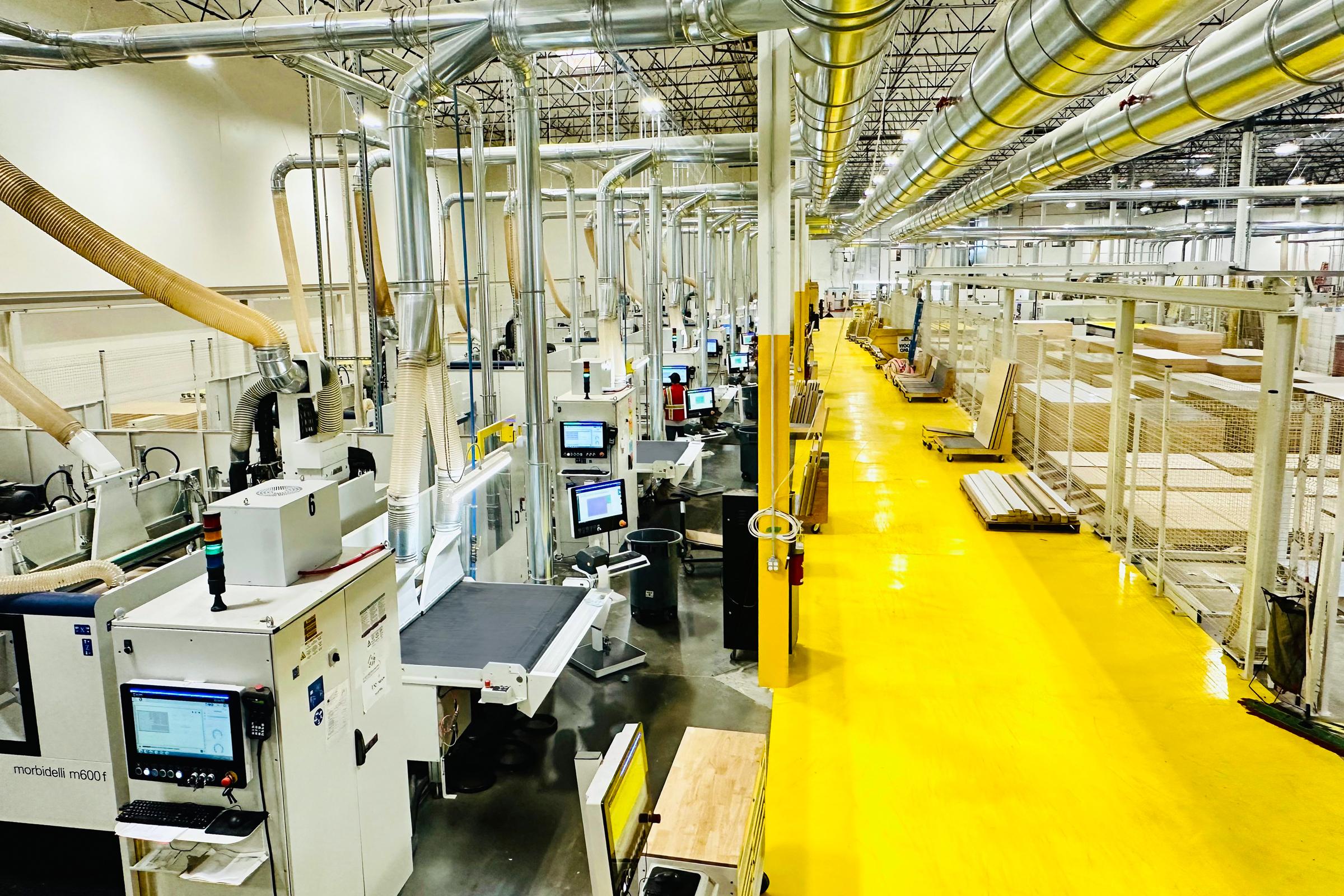
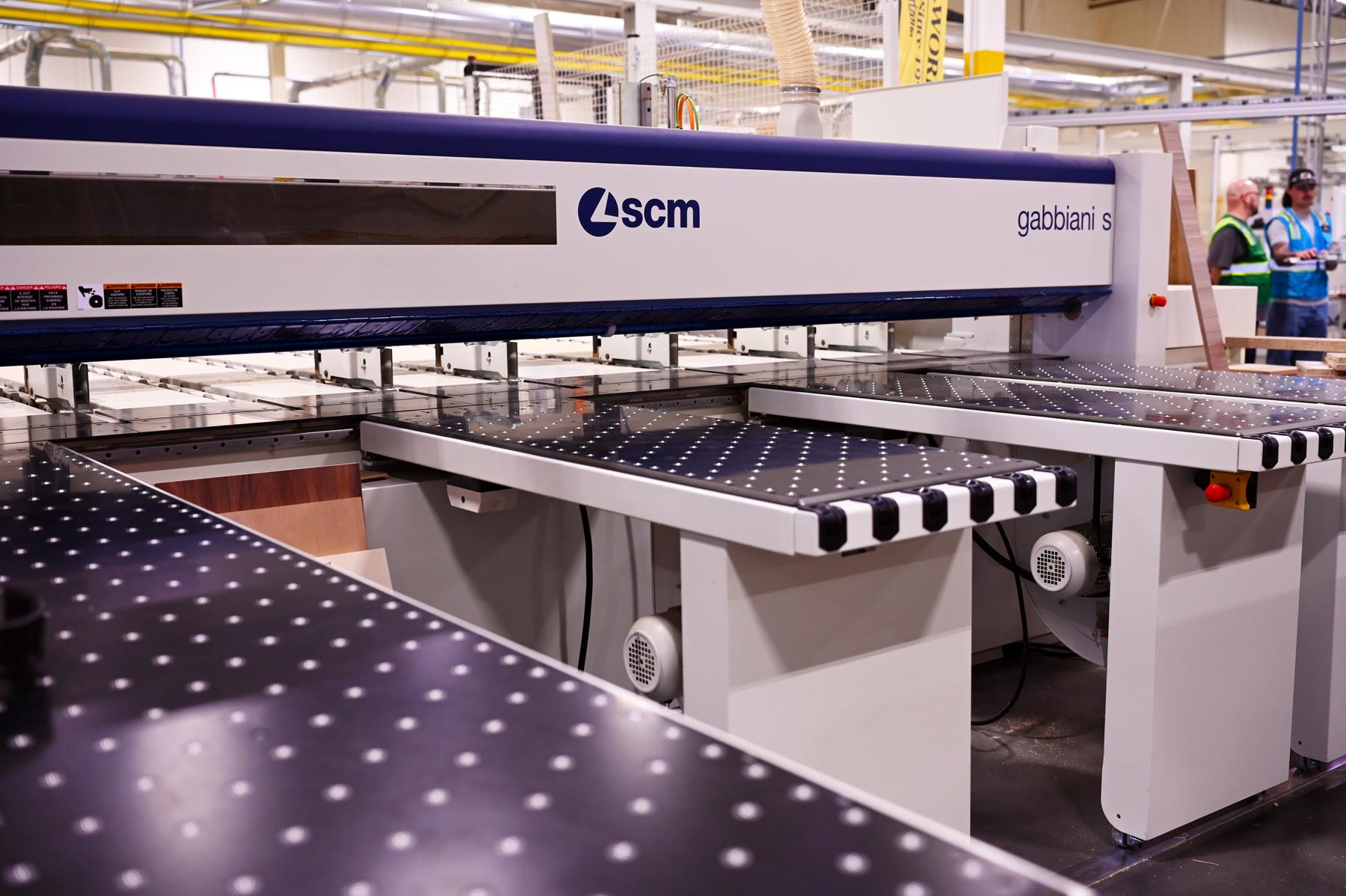
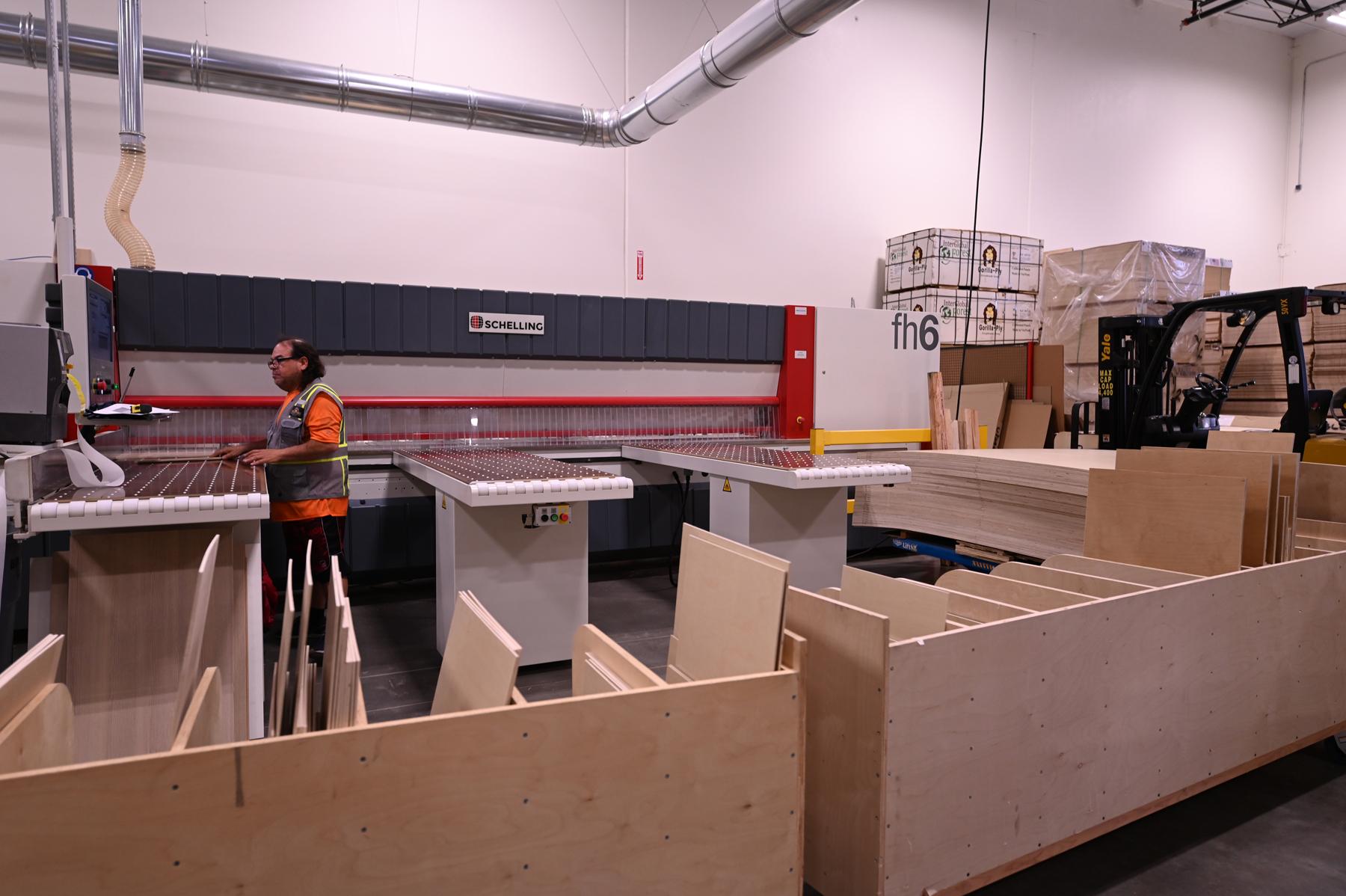
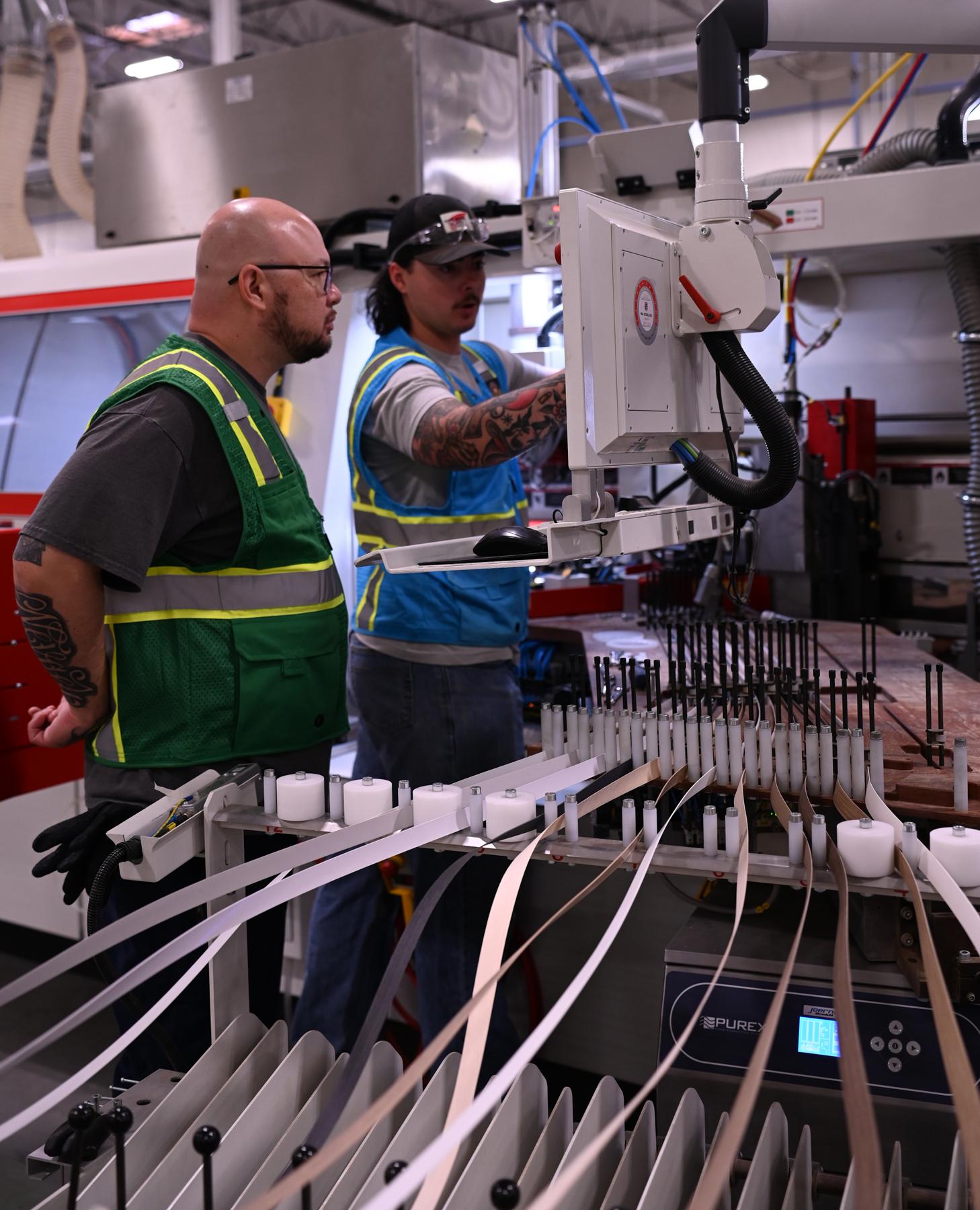
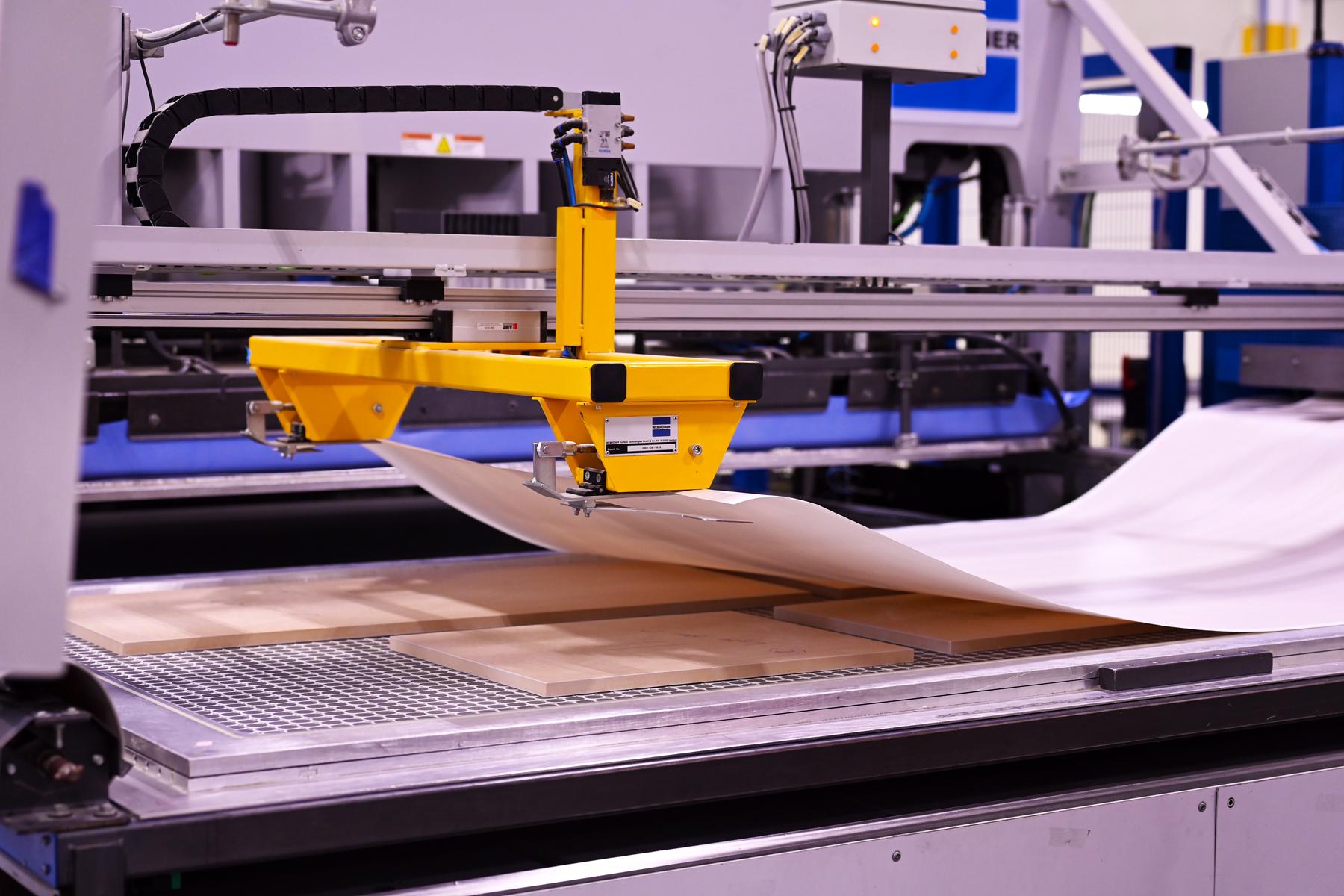
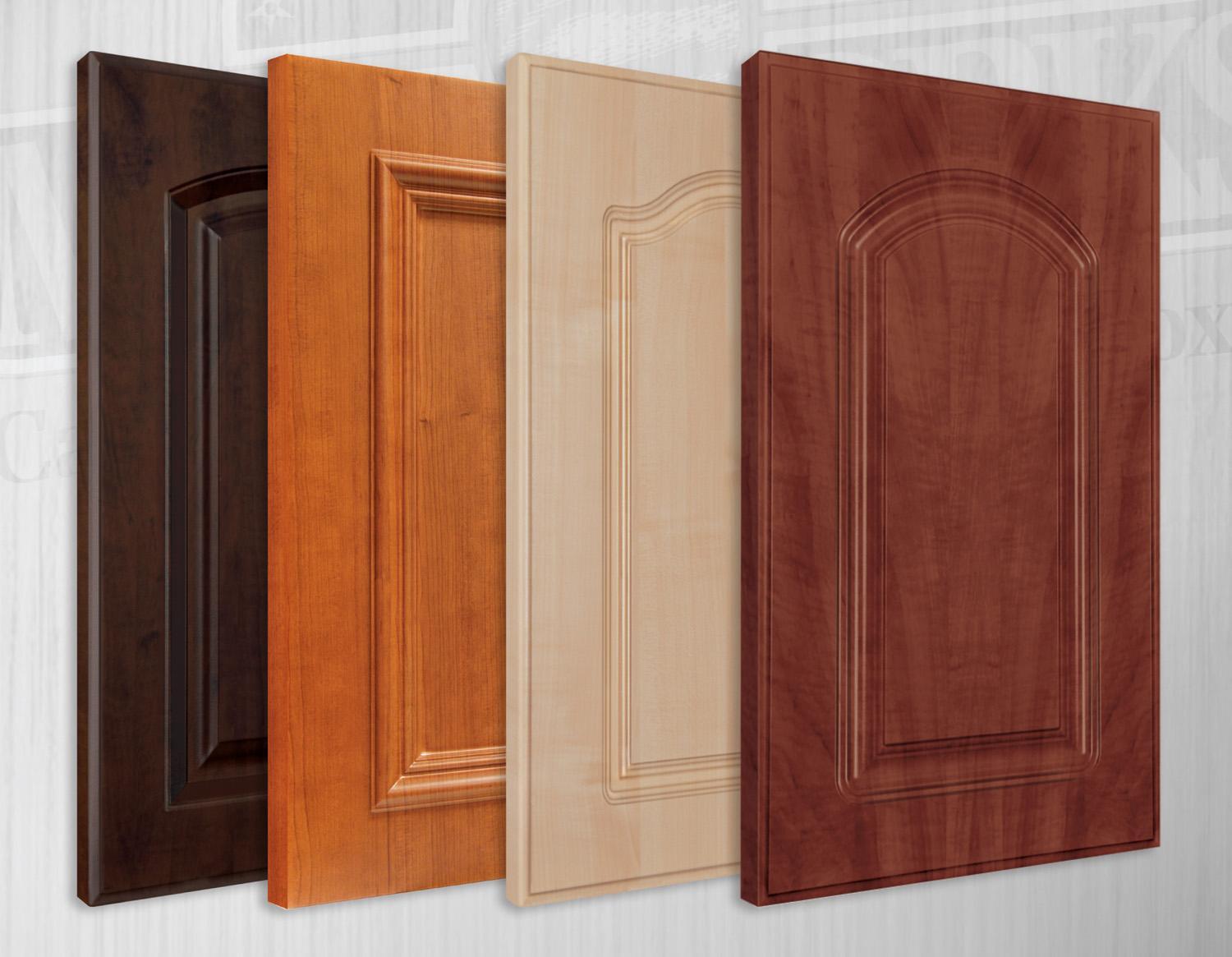
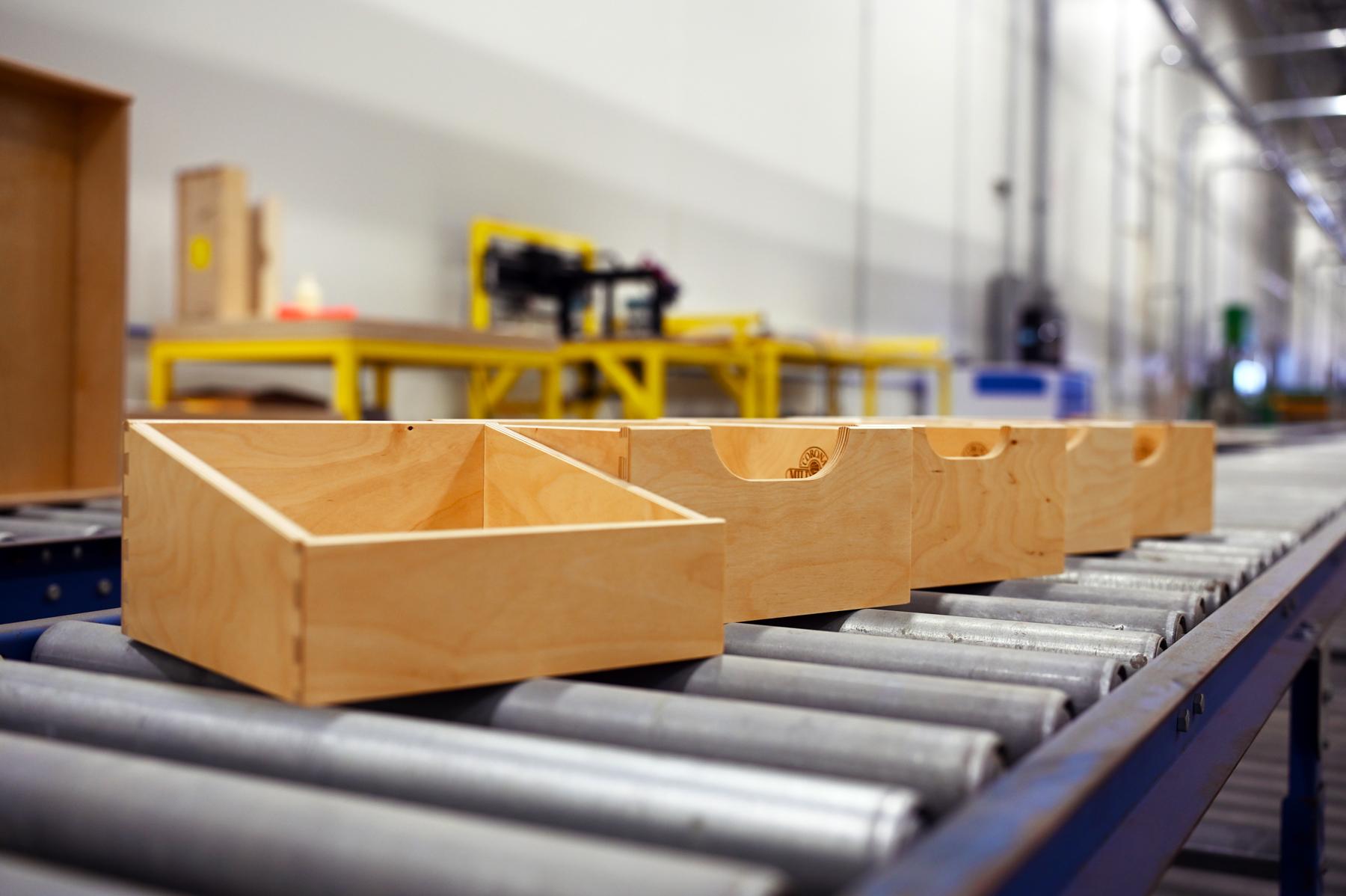
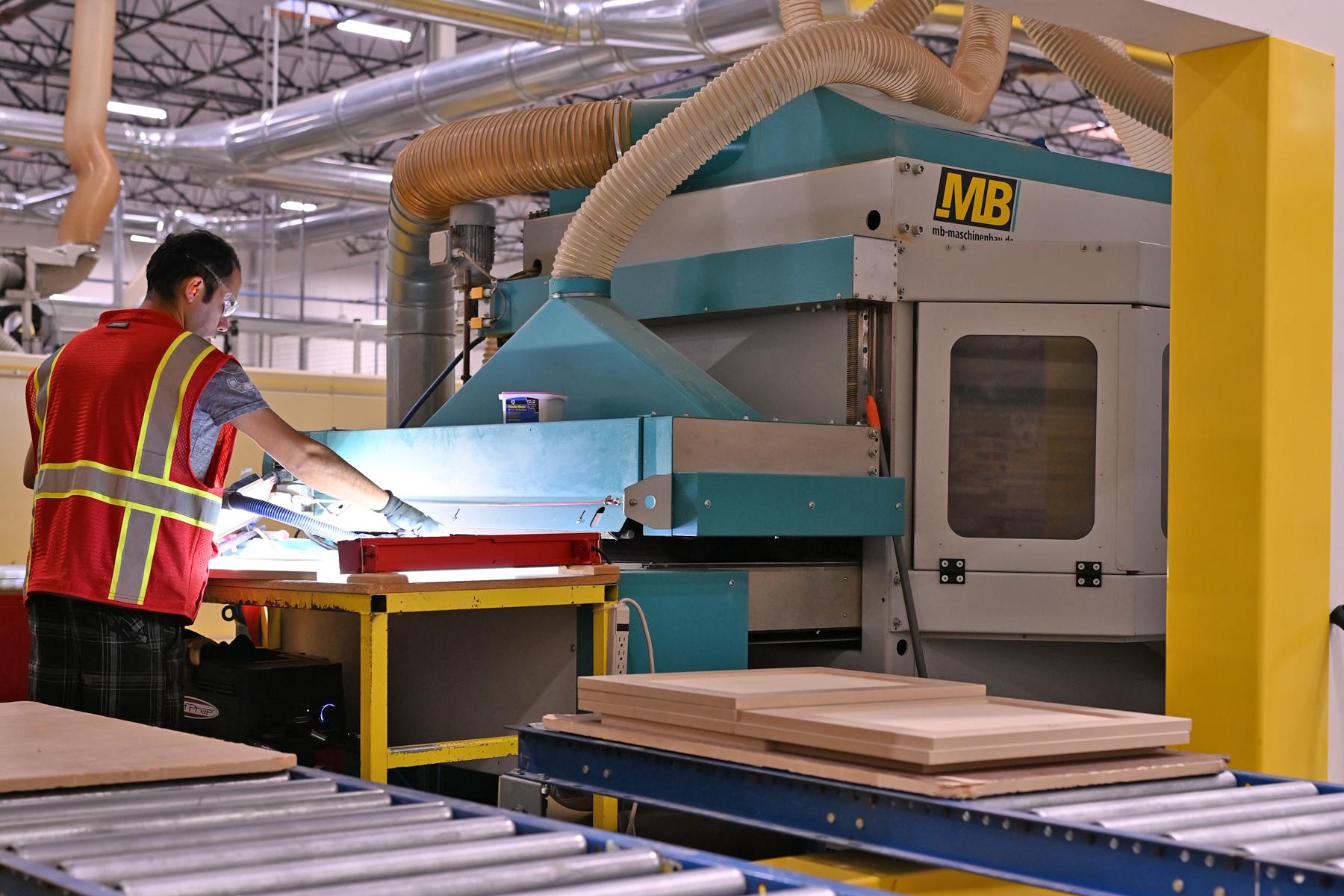
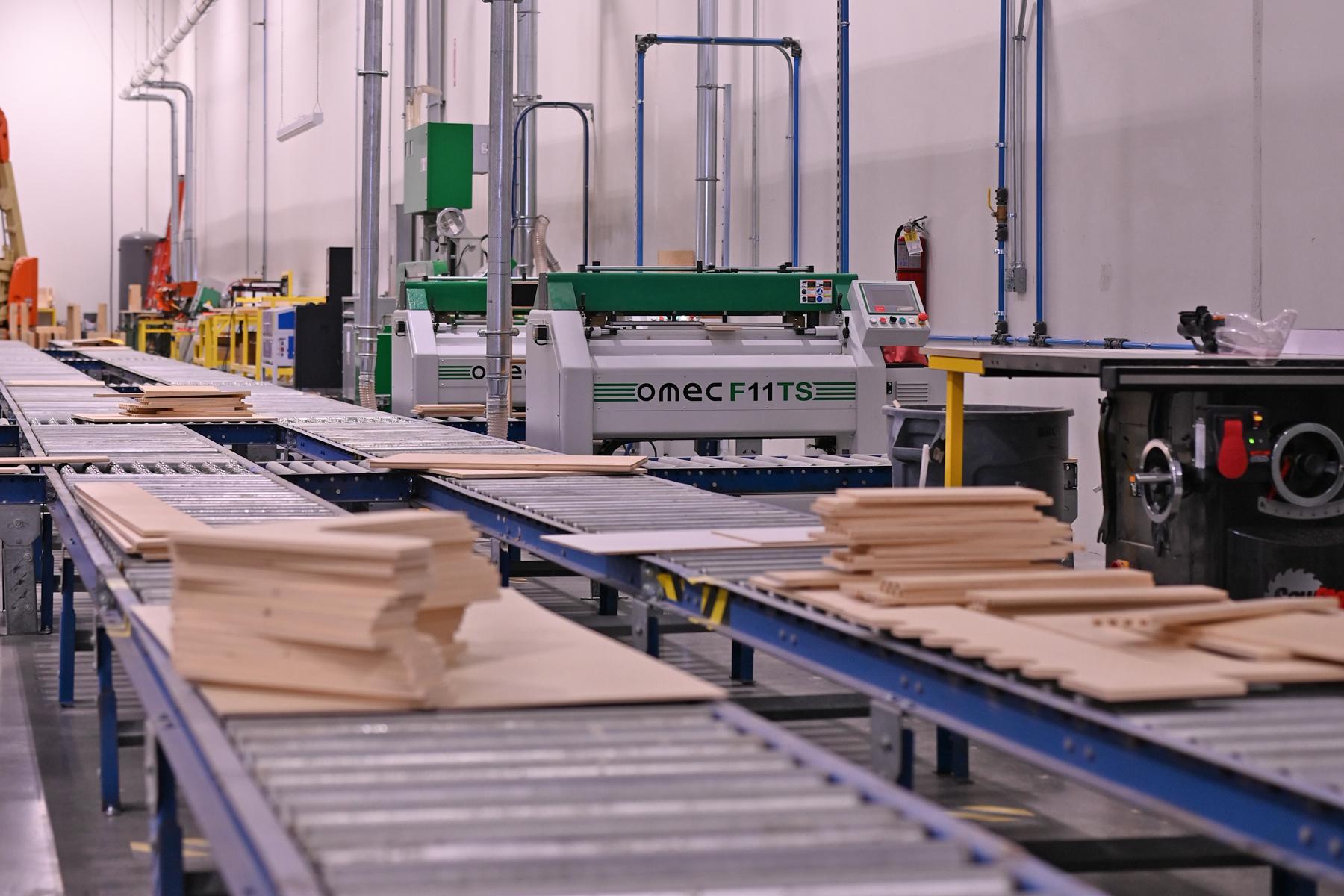
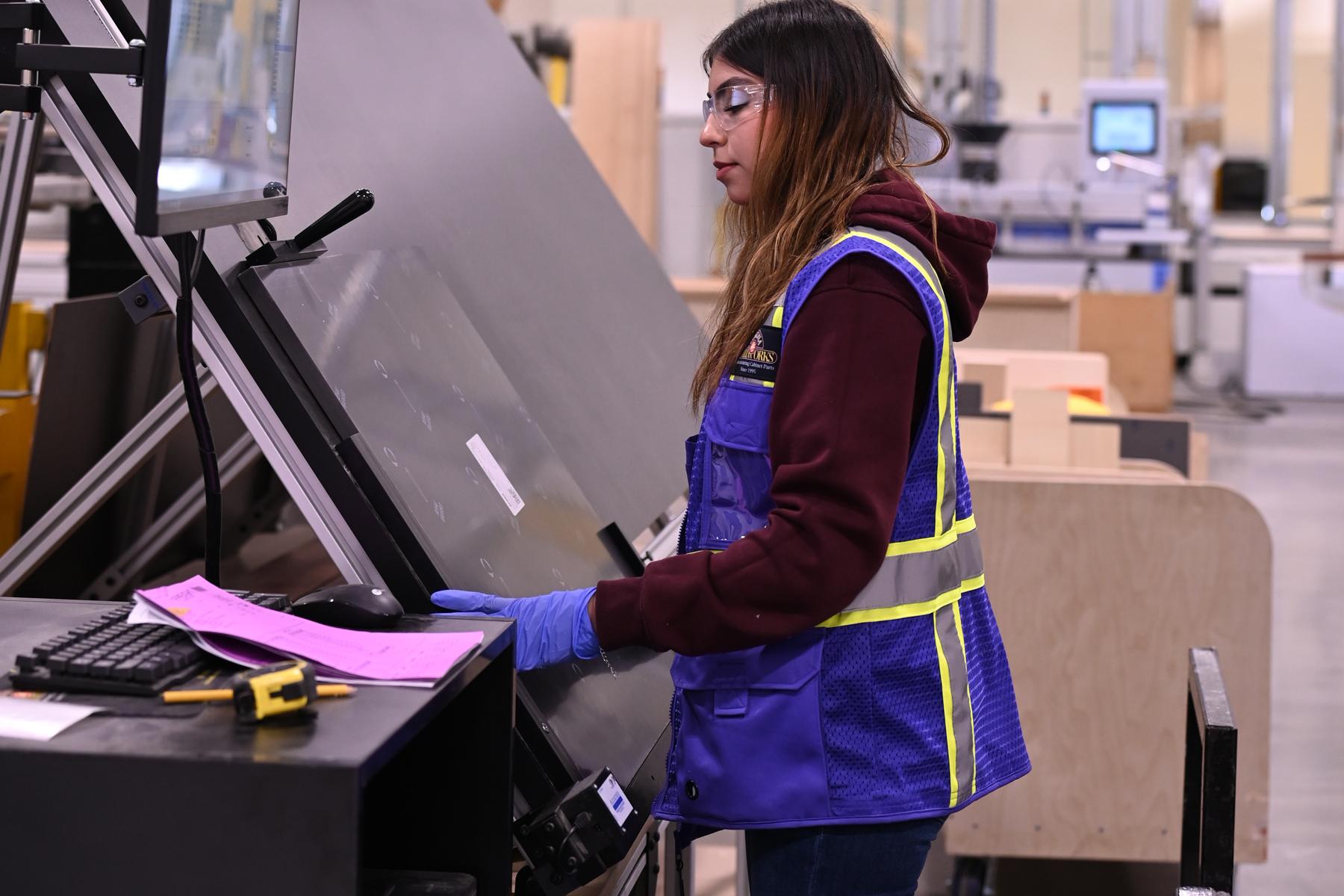
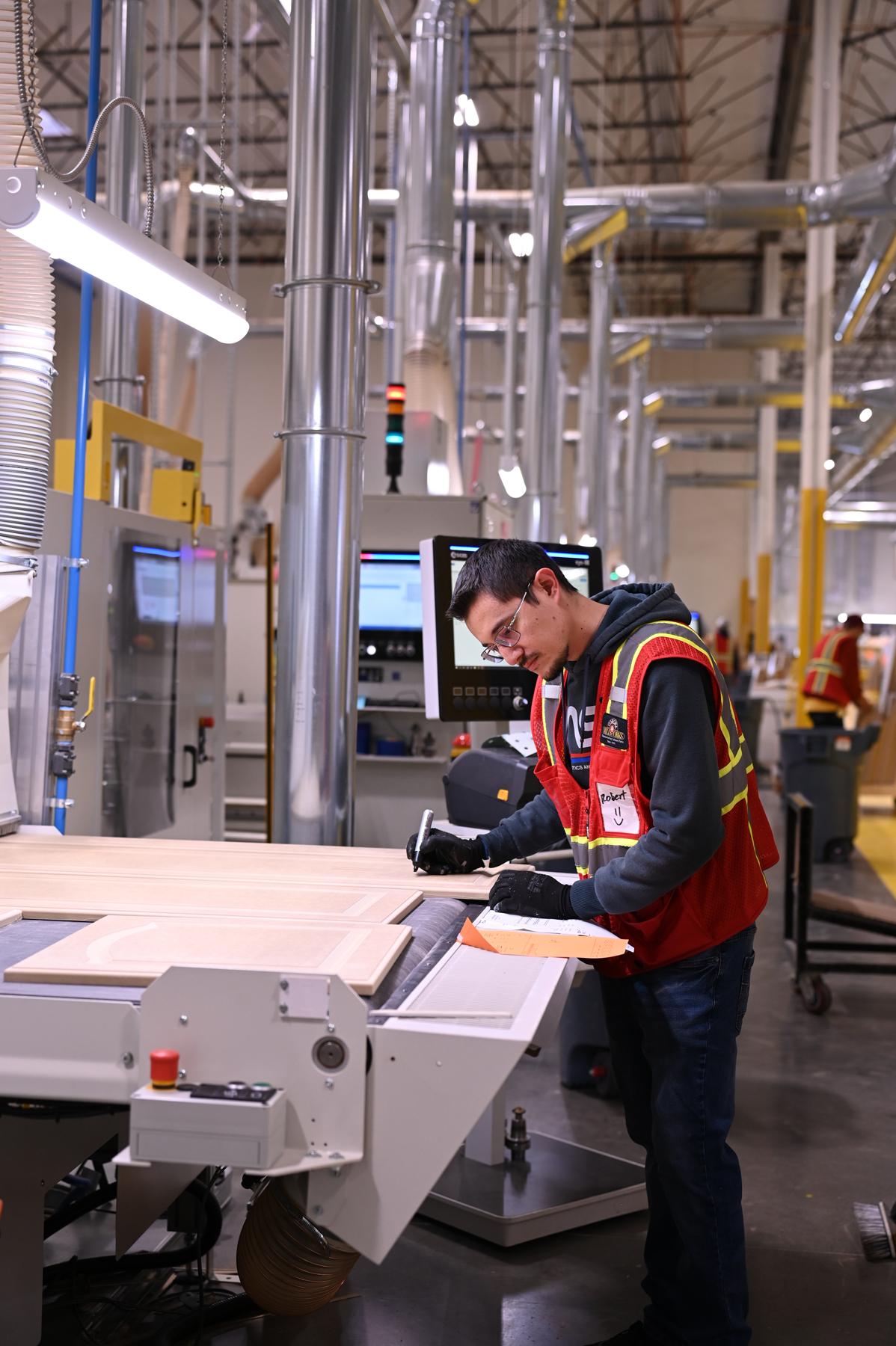
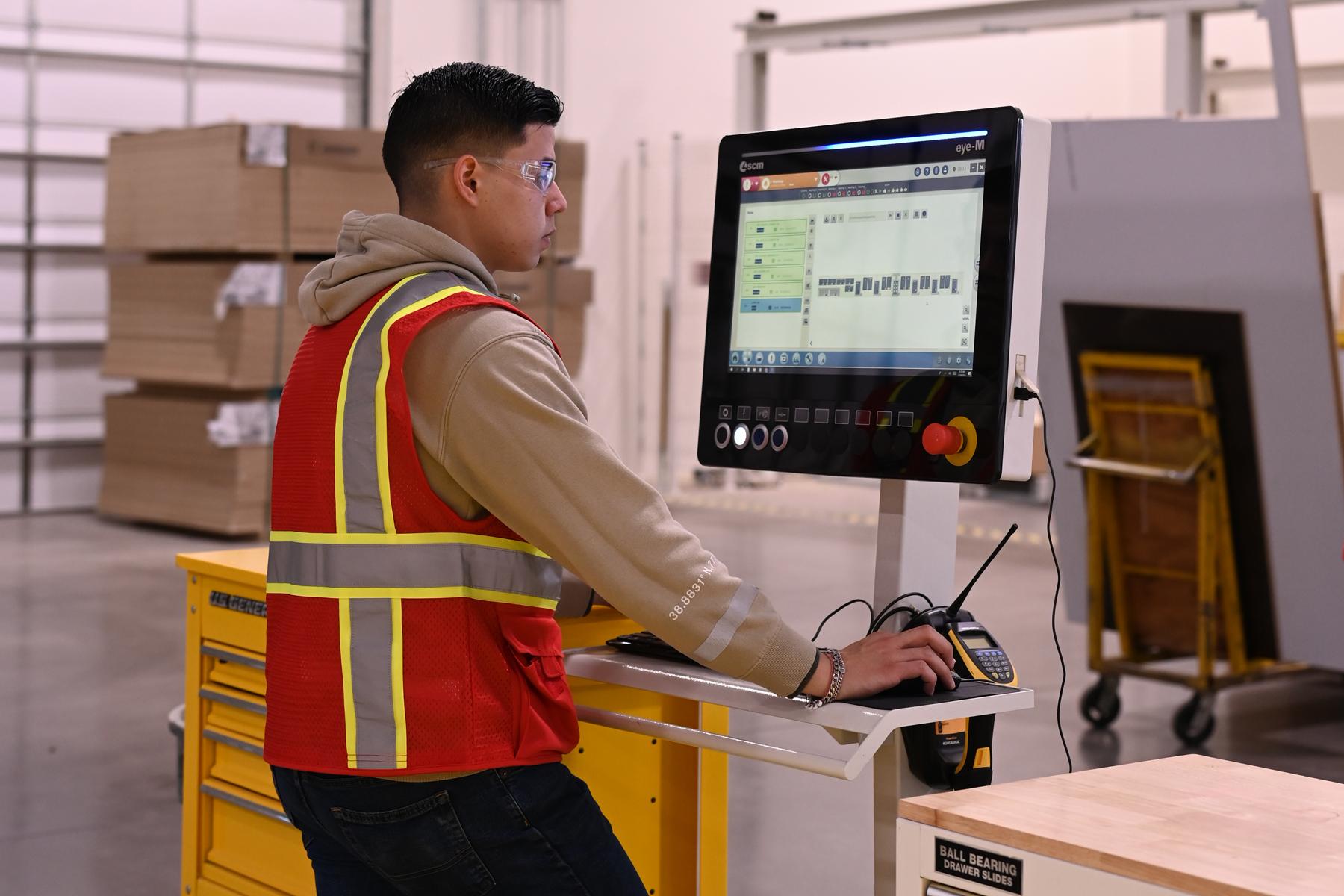
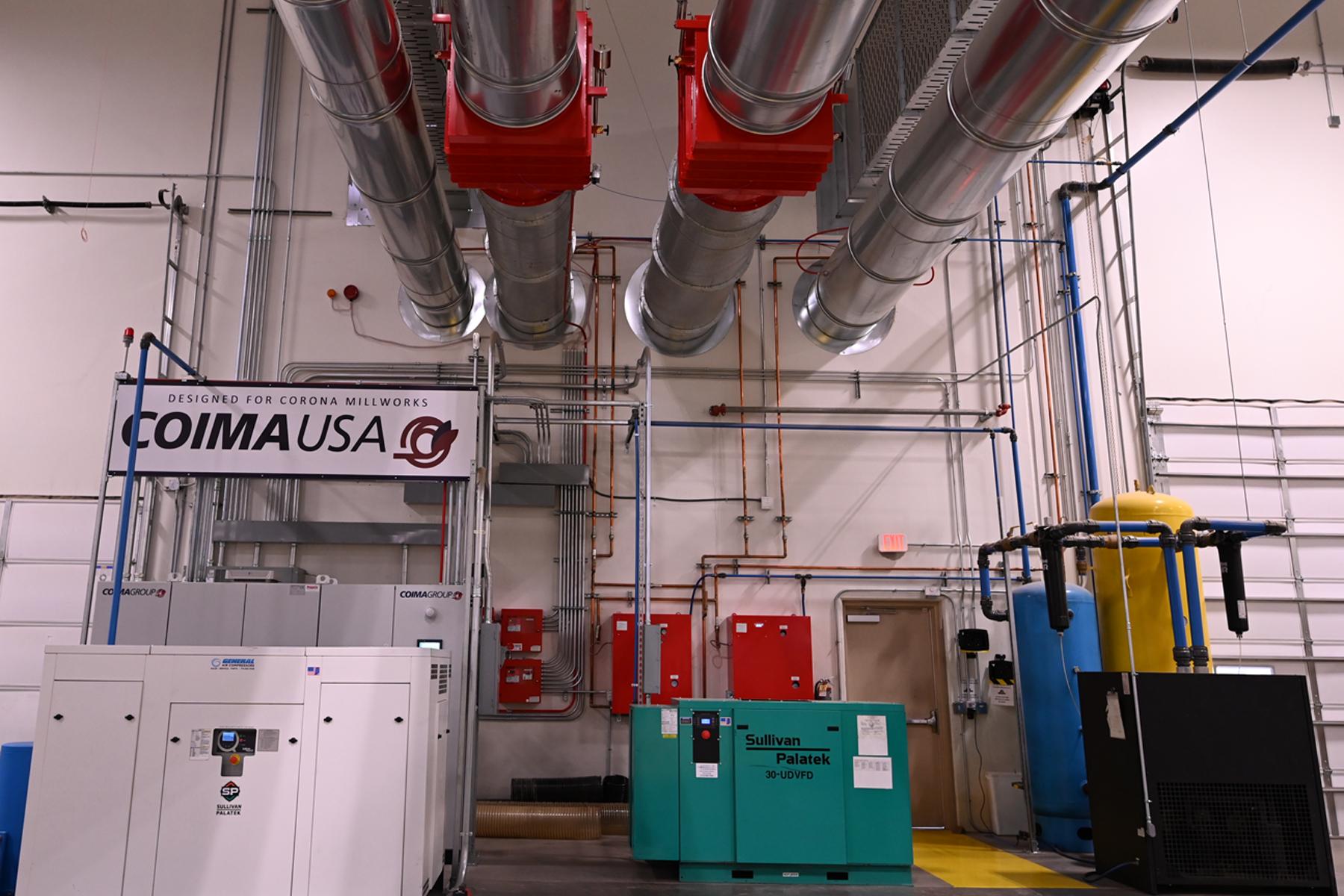
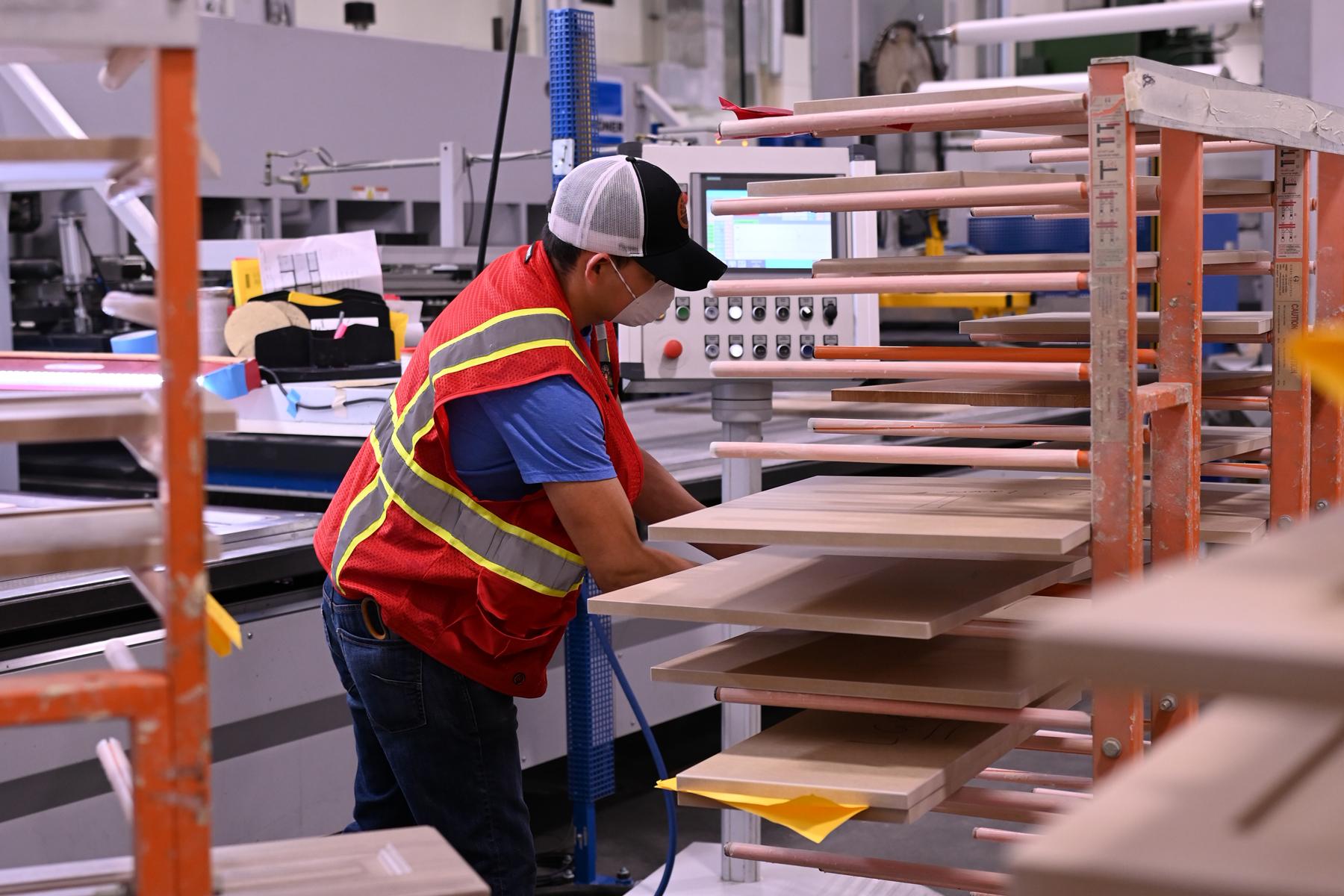
Corona Millworks’ newest facility in Tolleson, Arizona, is abundant with state-of-the-art equipment for efficient manufacturing of its cabinet doors, drawer boxes, and other components. Along with the seamless production that comes with incorporating Industry 4.0 technology, the company also can collect and analyze data to optimize order entry, estimating/pricing, inventory management, production scheduling, and machine maintenance.
Headquartered in Chino, California, Corona Millworks is #175 in the FDMC 300, a ranking of the largest wood products manufacturers in North America. 2023 sales were approximately $40 million and are projected to grow 10 to 15 percent for 2024 as the company continues to ramp up production.
The addition of the Arizona location brings Corona Millworks’ total square footage to approximately 150,000, with roughly 200 employees, noted Ashley Corona, operations manager.
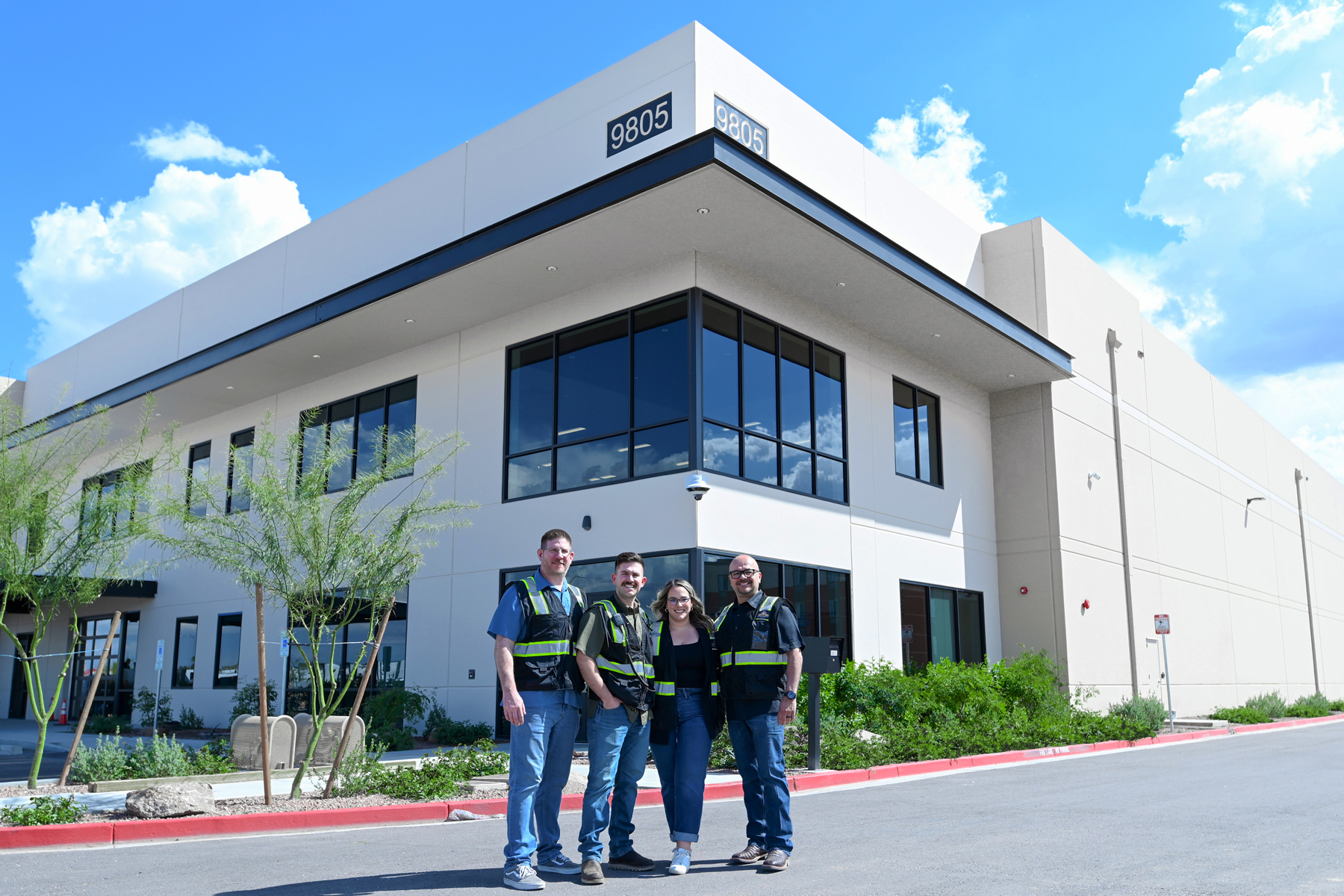
Filling a niche
Corona Millworks was founded in 1995 by Jose Corona, then a general contractor of custom homes. Corona experienced trouble obtaining the cabinetry to finish jobs and began building cabinet parts for his own projects, then for others by request. It wasn’t long before he decided “the best way to take the company was to just focus on the cabinet parts and leave general contracting in the rear view,” explained Nathan Corona, Arizona operations.
Today, Corona Millworks provides custom components for kitchen and bath cabinetry, closets, garages, and more to industry professionals. “By providing cabinet parts to our customers, it allows them to take on more work, and/or supplement work that exceeds their capacity,” he added.
Products offered include: rigid thermofoil (RTF) doors in a variety of styles, E-Series doors which are laser edgebanded and offered in a range of textures, and wood doors in cope-n-stick, mitered, applied moulding, louver and contemporary styles. Also available are dovetail and dowel construction drawer boxes and other cabinetry components.
Production is split between the two locations, with the thermofoil doors, E-Series doors and cabinetry components manufactured in Arizona, wood doors in California, and drawer boxes at both. The current capacity is roughly 10,000 doors per week for the foil line, 1,000 per week for the E-Series, 7,500 for wood, and 3,000 for drawer boxes, with an estimated 750 sheets cut weekly for cabinet boxes and other components, said Mitch Brown, general manager.
“We’re helping our customers and adding value,” added Felix Brown, national account manager. “And as we scale our business, we are helping our customers scale theirs.”
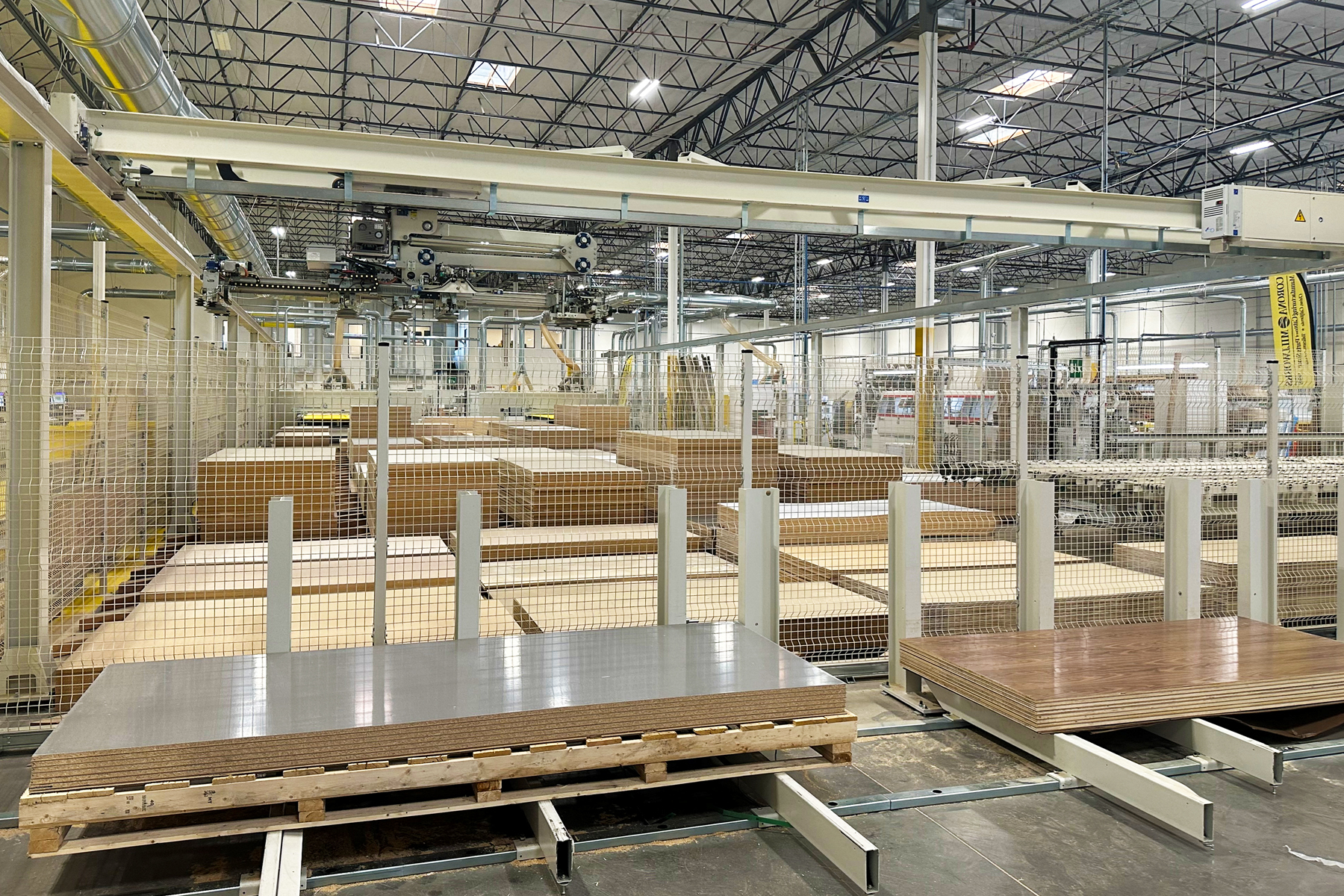
Connecting with Industry 4.0
The newly built 80,000-square-foot facility represents an investment in excess of $10 million by Corona Millworks to grow not only its future but also its customers’ businesses. “This industry is moving so fast,” Felix said. “We’re not only ready for today but also anticipating where we need to be – and to grow with this equipment.”
Technology is packed into the production floor, with machines connecting and exchanging information through the network for efficient and seamless manufacturing. “It didn’t make sense to have outdated machinery in our brand new facility,” Nathan said. “We wanted it to be top-of-the-line.”
The strategic use of technology has helped alleviate labor recruitment concerns, and also enabled Corona Millworks to “condense what was in three buildings in California into the one in Arizona,” added Mitch.
The production floor is separated into four cell areas under one roof, for easy flow: Thermofoil Series doors, E-Series doors, drawer boxes, and cabinet components.
For the Thermofoil Series, panels are fed from a FlexStore ELR three-axis storage and retrieval system to one of six Morbidelli m600 CNC routers for shaping. Designed for medium to large production, the SCM FlexStore is a flexible system that manages both homogeneous and mixed stacks, dimensions and colors, and provides organization and inventory tracking.
“The RTF doors are available in more than 50 styles with more than 50 color choices in stock. Once routed, the MDF doors are sanded on the MB sander, sprayed with adhesive, and the decorative surfacing material is laminated to the MDF substrate using a Wemhoner 3D press. A second Wemhoner press is also in-house for flat panel lamination.
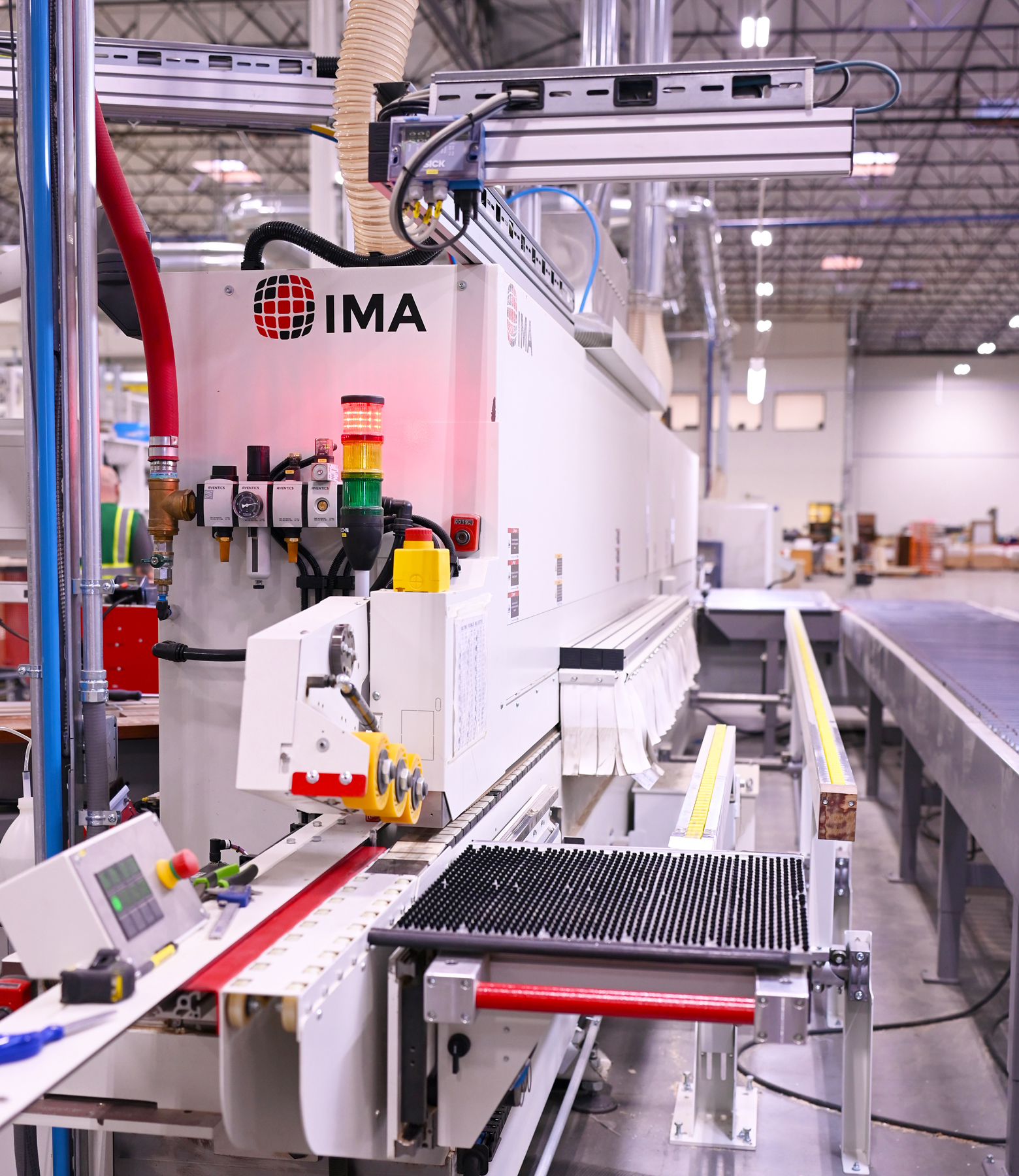
One of the many things that set the company apart, Mitch and Felix agreed, is its use of a “true” laser edgebander, an IMA Novimat, in the production of its E-Series doors. Corona Millworks, they added, boasts the largest one on the West Coast.
For the E-Series items, sheet goods of all types, including textured melamine, acrylic, laminate, and veneer panels are cut to size on the Gabbiani S panel saw, then finished with zero-joint laser edgeband. The seamless joint between the edgeband and panel creates an upscale finished product. “It is virtually seamless banding, so you don’t see the glue line that you do with a PUR product. You spend less time detailing, which helps with our production efficiency,” Ashley said.
E-Series doors come in Slab (one-piece), Sienna (three-piece), and Shaker (five-piece) styles, and are available in a wide variety of colors and finishes.
A second FlexStore system feeds both the E-Series and cabinet components cells. Also used to produce the cabinet boxes and components is a Morbidelli x200 CNC, Omga cutoff saw, Omal Insert dowel insertion machine, an IMA edgebander and Robotech sander.
“You still need people to offload, but the whole system is talking to each other — it’s seamless,” Mitch said of the technology.
The drawer box cell is also highly automated and includes a rear-loading Schelling f6 panel saw, Omga cutoff saws, multiple Omec F11TS dovetailers, Omal Insert dowel inserter, and an Eagle laser engraver. Drawers are available with standard, angled or scalloped sides, and can be engraved for added customization.
“We’re taking the craftsmanship of the past and combing it with the technology of the future,” Ashley said. “Our modern equipment allows us to fabricate high-quality goods in a very efficient manner, so we don’t have to sacrifice quality for speed.”
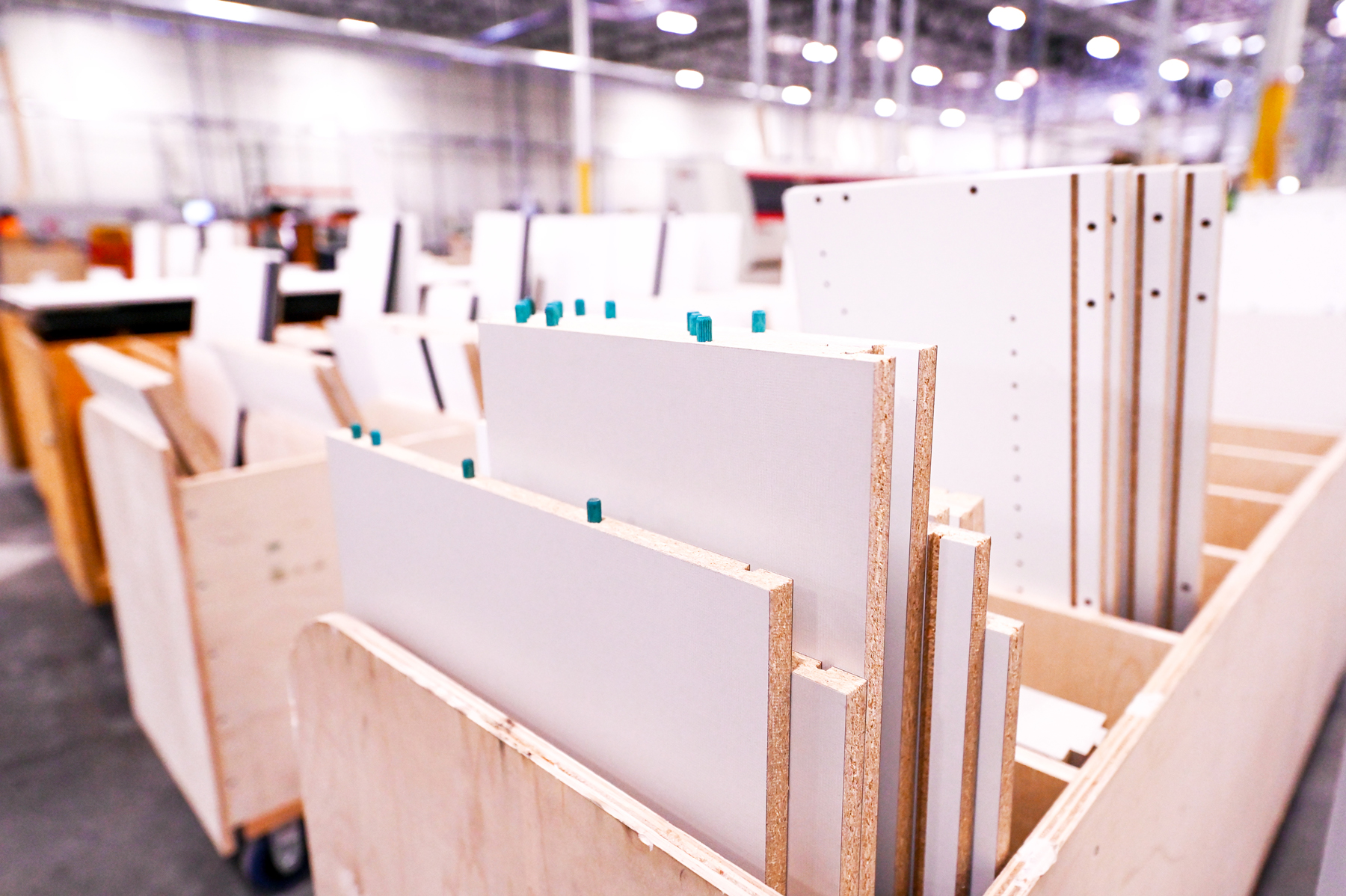
Safety & sustainability
Safety and sustainability are key at Corona Millworks. Given the large number of machines running at any given time, the company installed a large – over 25 feet tall – Coima dust collector equipped with a variable frequency drive that can automatically control and optimize the airflow based on the frequency and power usage of the machine operations. Some of the company’s sawdust is also repurposed.
There are other ways Corona Millworks is actively reducing its carbon footprint. Along with lighting on occupancy/motion sensors for energy savings, “The new materials that we’re using are eco-friendly,” Mitch noted. “We recognize in today’s world that that’s a direction we have to continue to go in.”
In addition, a new online ordering system is being implemented, part of Corona Millworks’ commitment to paperless production and Industry 4.0. According to Ashley, the system will include preset options for items such as color/pattern/finish and style, and help facilitate customer estimates and lead times.
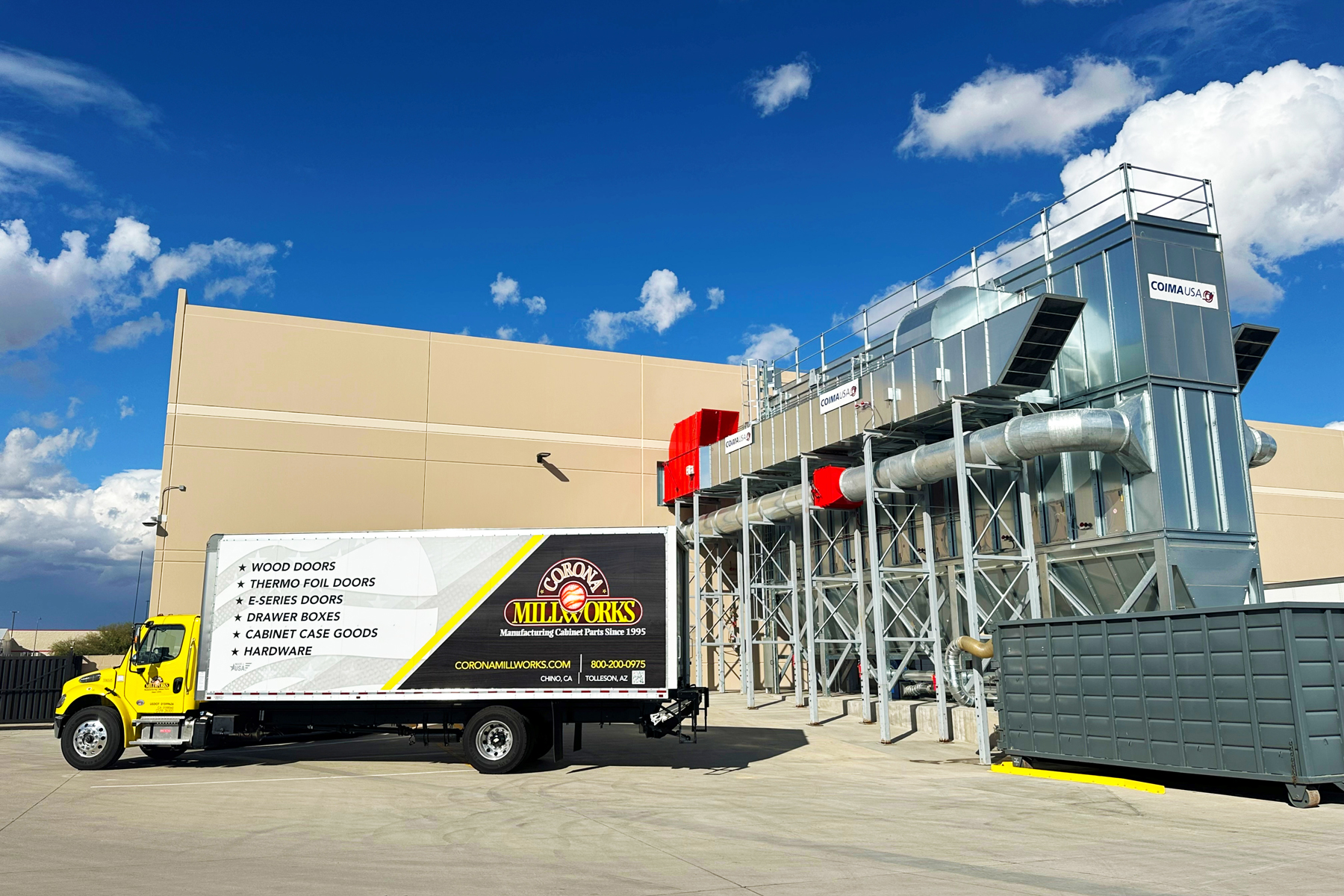
More opportunities
Along with the technology, more capabilities and capacity, locating the facility in Arizona has additional benefits for Corona Millworks. “We have had a presence in Arizona for many years, today we are more than just a presence, we are actually part of the community and contribute to the growth of the Phoenix area,” Felix said. Because of the lower freight and shipping costs to the regional and national customers, it is allowing Corona Millworks the opportunity to expand its existing customer base.
“As our ability to expand nationally continues to grow, we will see returns on our investment over the next three to five years,” Jose Corona added. “We want our customers to see us and use us as an extension of their business and a partner to help them grow their future business.”
Corona Millworks has already felt the impact and benefits of the move to Arizona and is looking forward to the future opportunities. For a video showing some of the operations go to bit.ly/CoronaMillworksAZ.
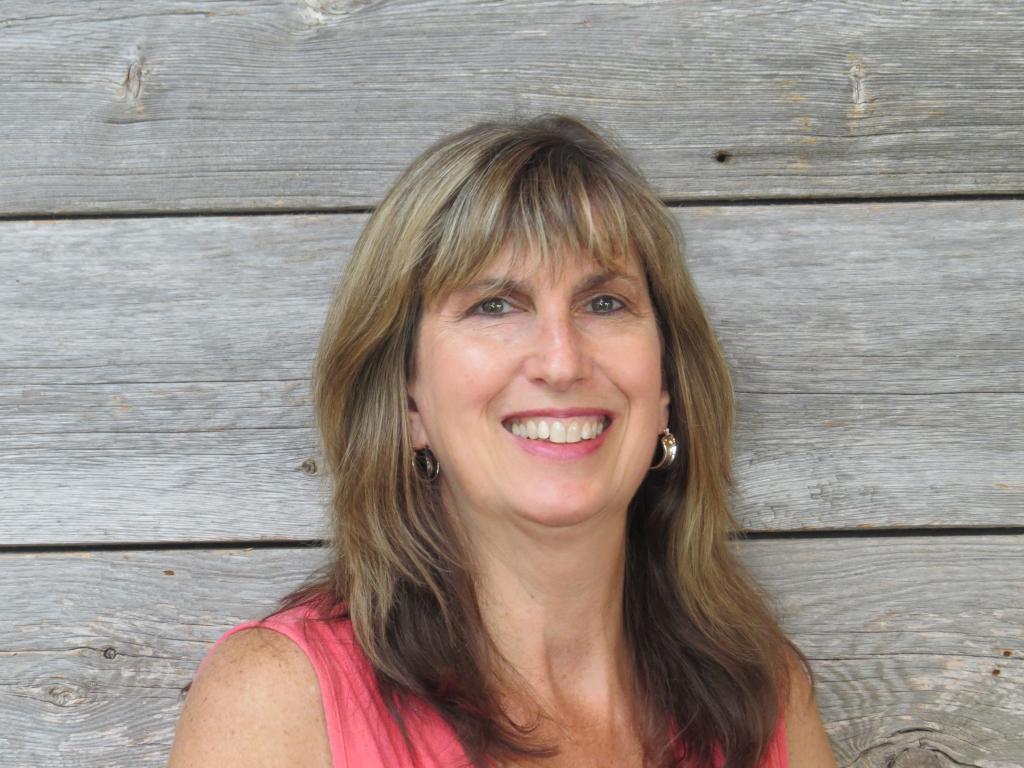
Karen M. Koenig has more than 30 years of experience in the woodworking industry, including visits to wood products manufacturing facilities throughout North America, Europe and Asia. As editor of special publications under the Woodworking Network brand, including the Red Book Best Practices resource guide and website, Karen’s responsibilities include writing, editing and coordinating of editorial content. She is also a contributor to FDMC and other Woodworking Network online and print media owned by CCI Media. She can be reached at [email protected]
Have something to say? Share your thoughts with us in the comments below.