This solid hardwood American flag made by Advanced Stair Systems is carved to look like it is waving in the breeze.
Gluing up all the parts of the flag takes three stages. The white stripes and stars are hard maple, the red stripes are sapele mahogany, and the star field is black walnut.
A CNC router is used to cut the recesses for the 50 stars in the field of black walnut.
Cutting the stars from hard maple is a particular challenge to get crisp corners.
The maple stars are glued into the black walnut field before the field is glued into the rest of the flag.
With the field glued into the rest of the flag, the Stars and Stripes are finally together.
Steve Guenzel said it took a lot of programming work in Autodesk Inventor to get the wave just right. It is cut out on the company’s 22-foot CNT Motion CNC router.
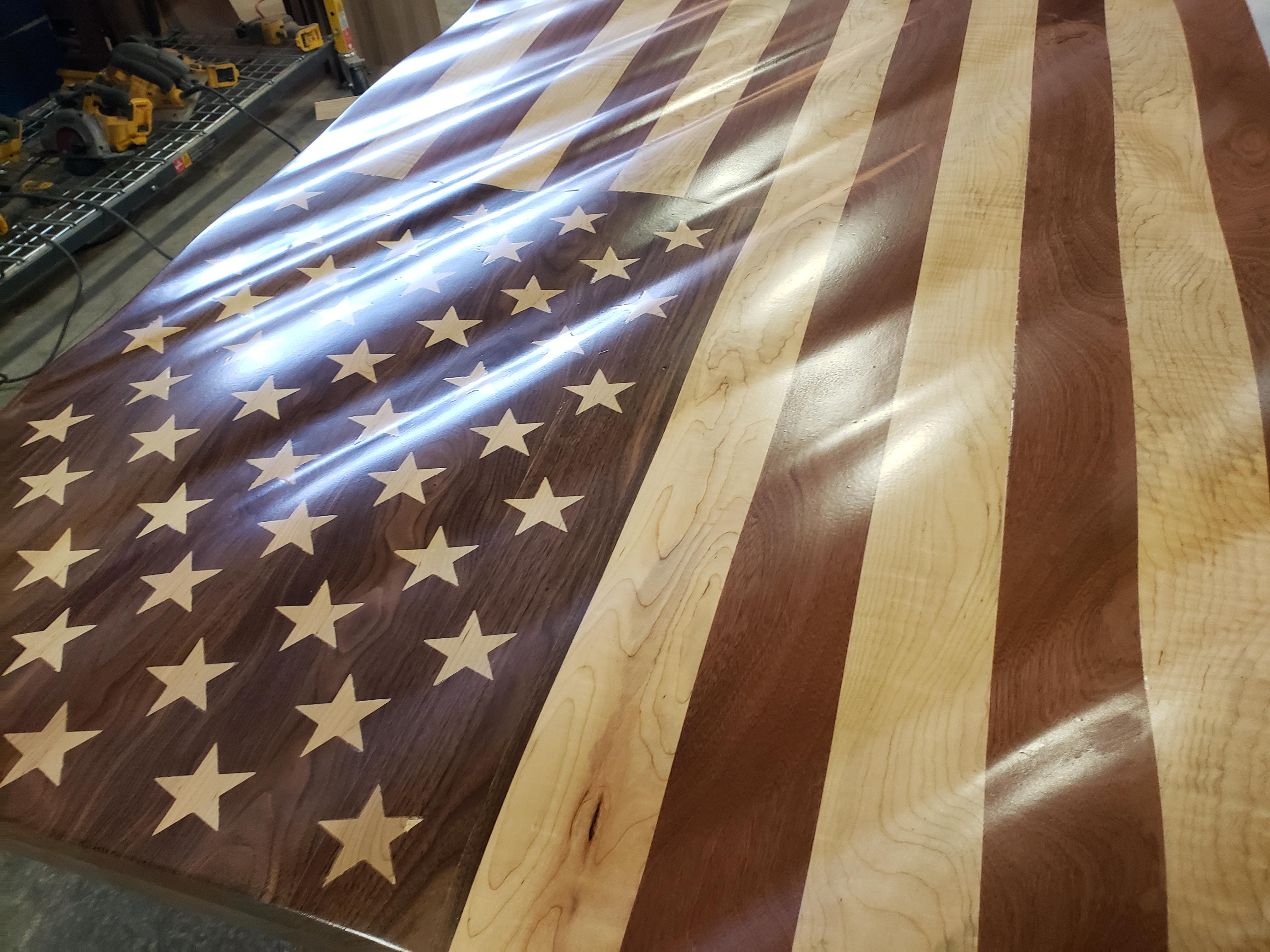
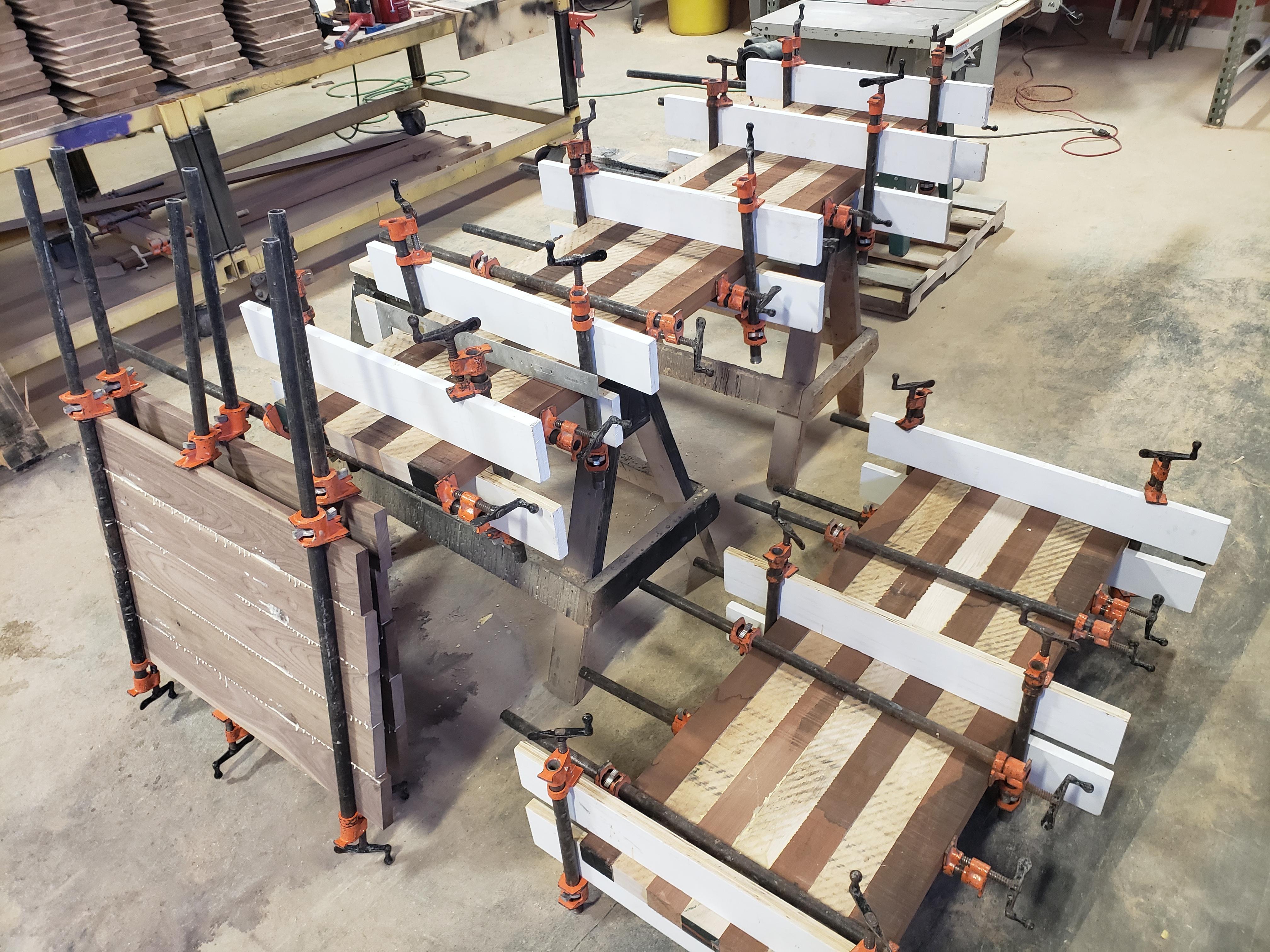
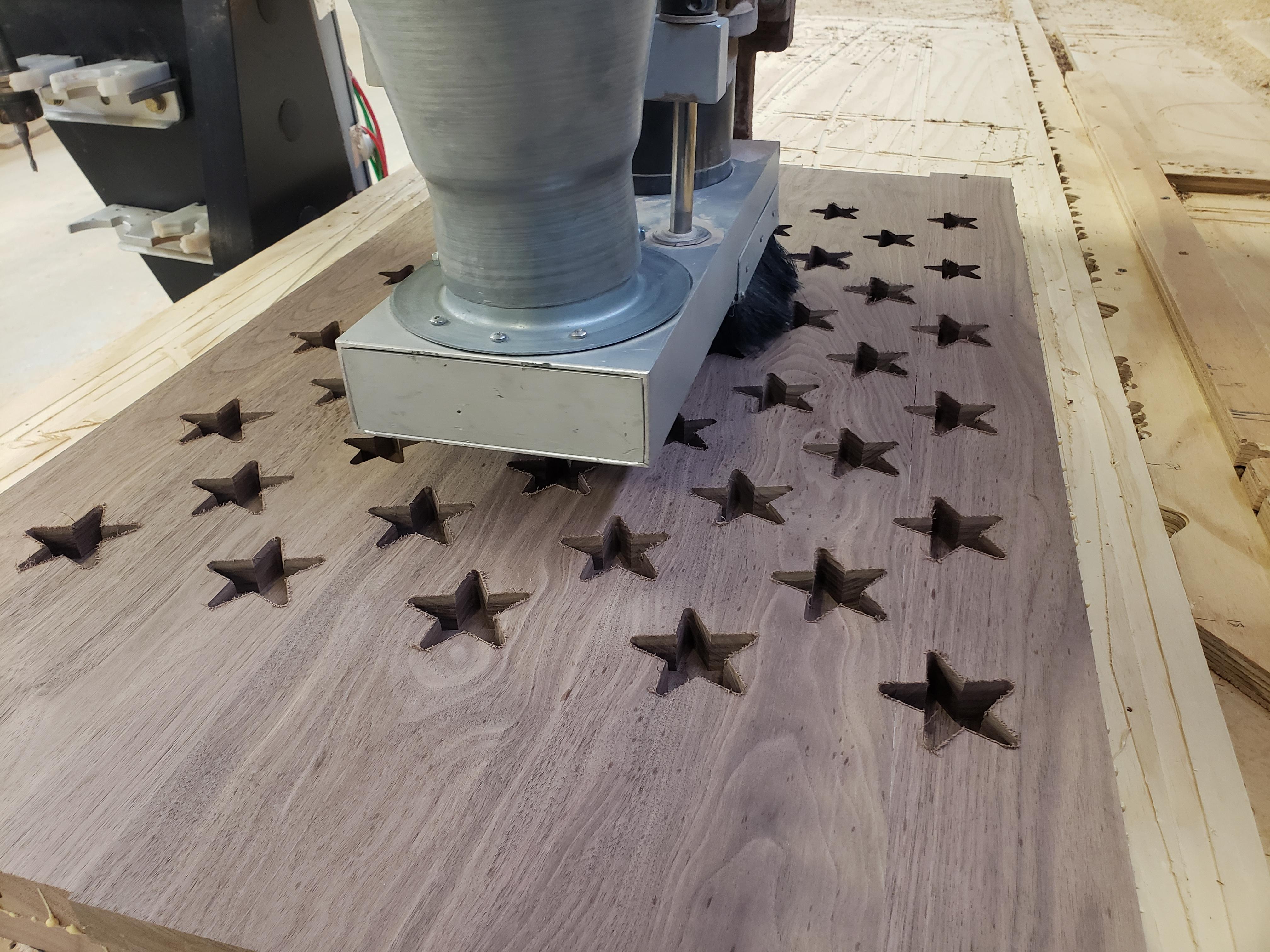
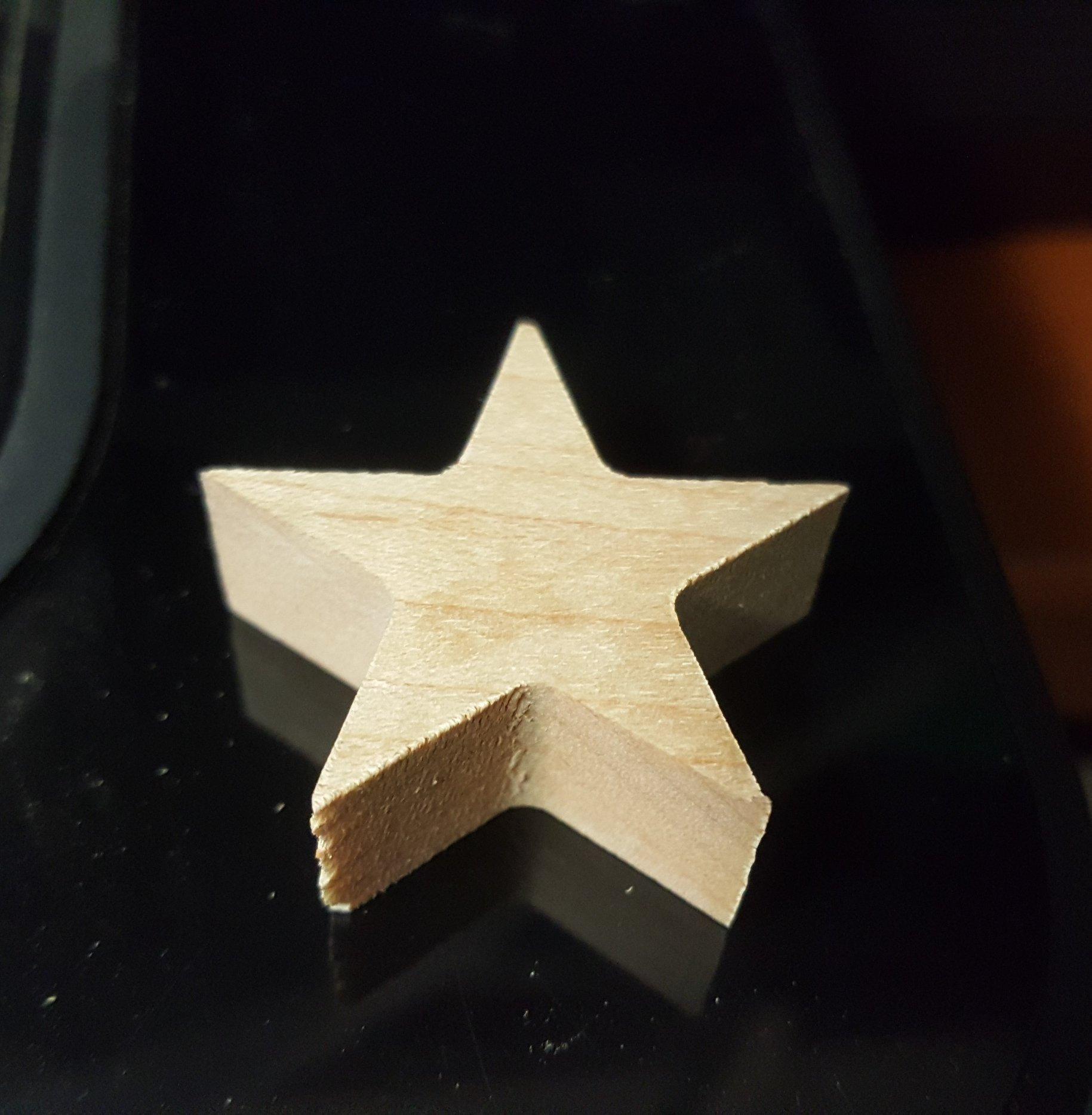
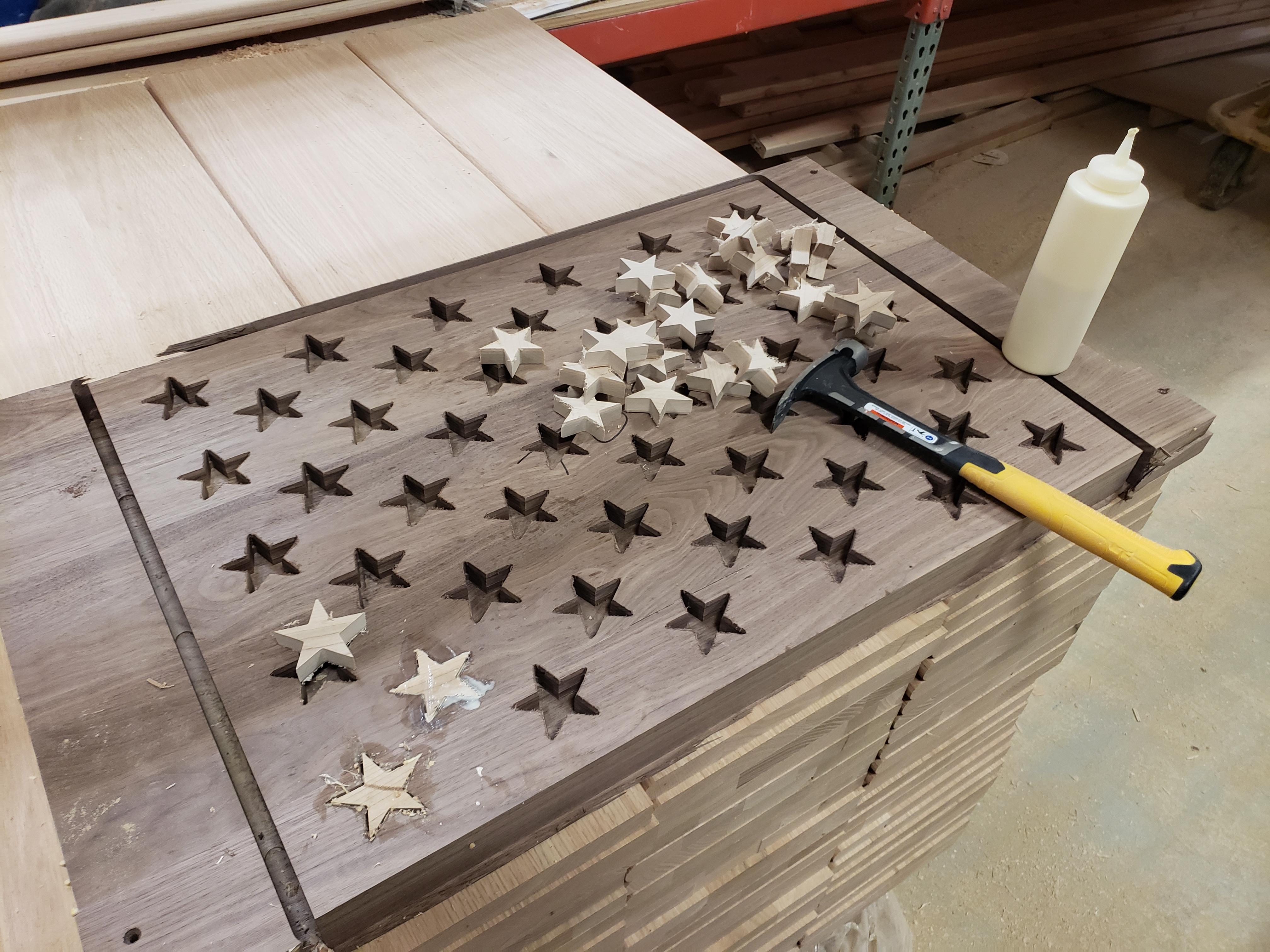
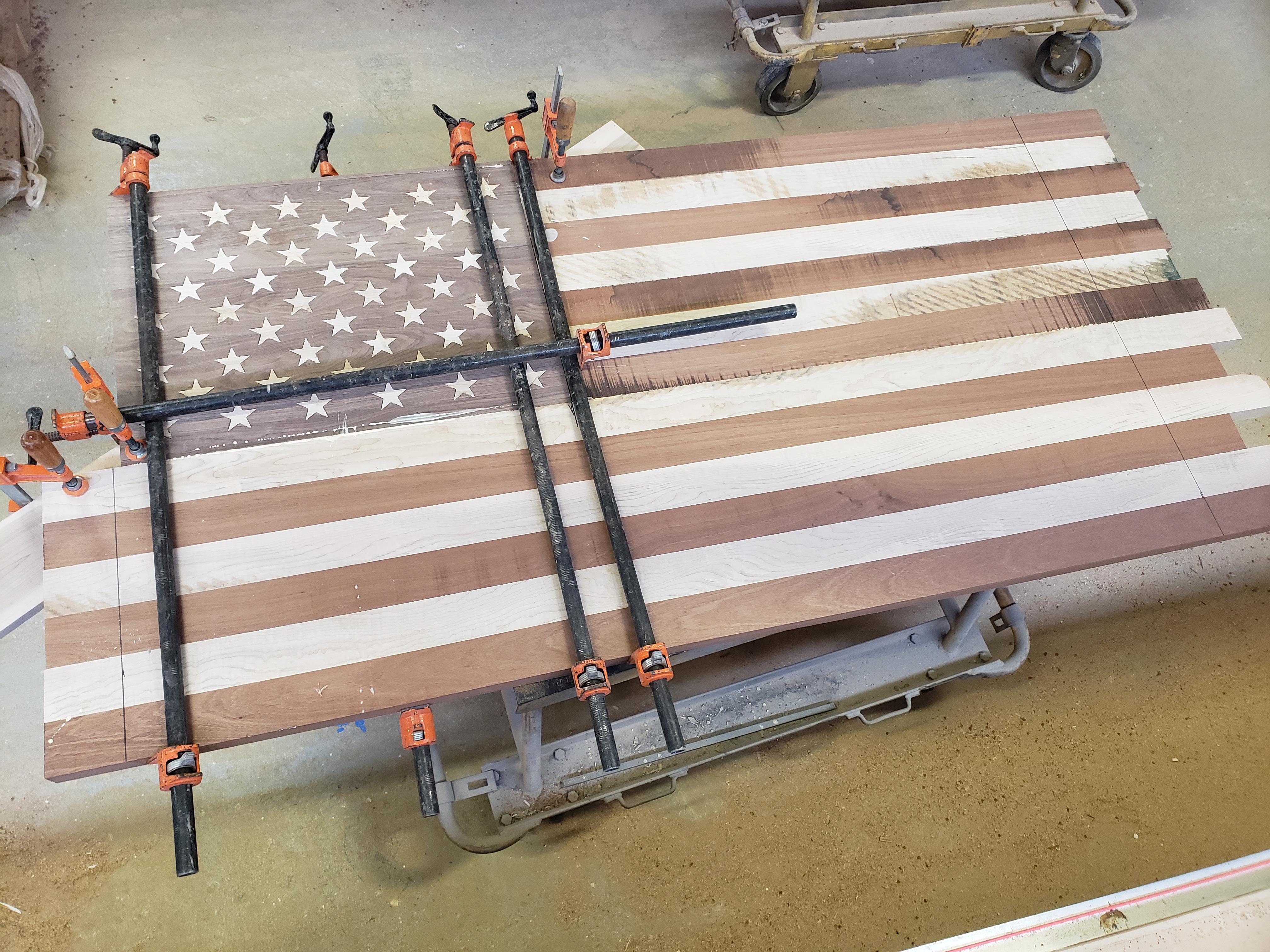
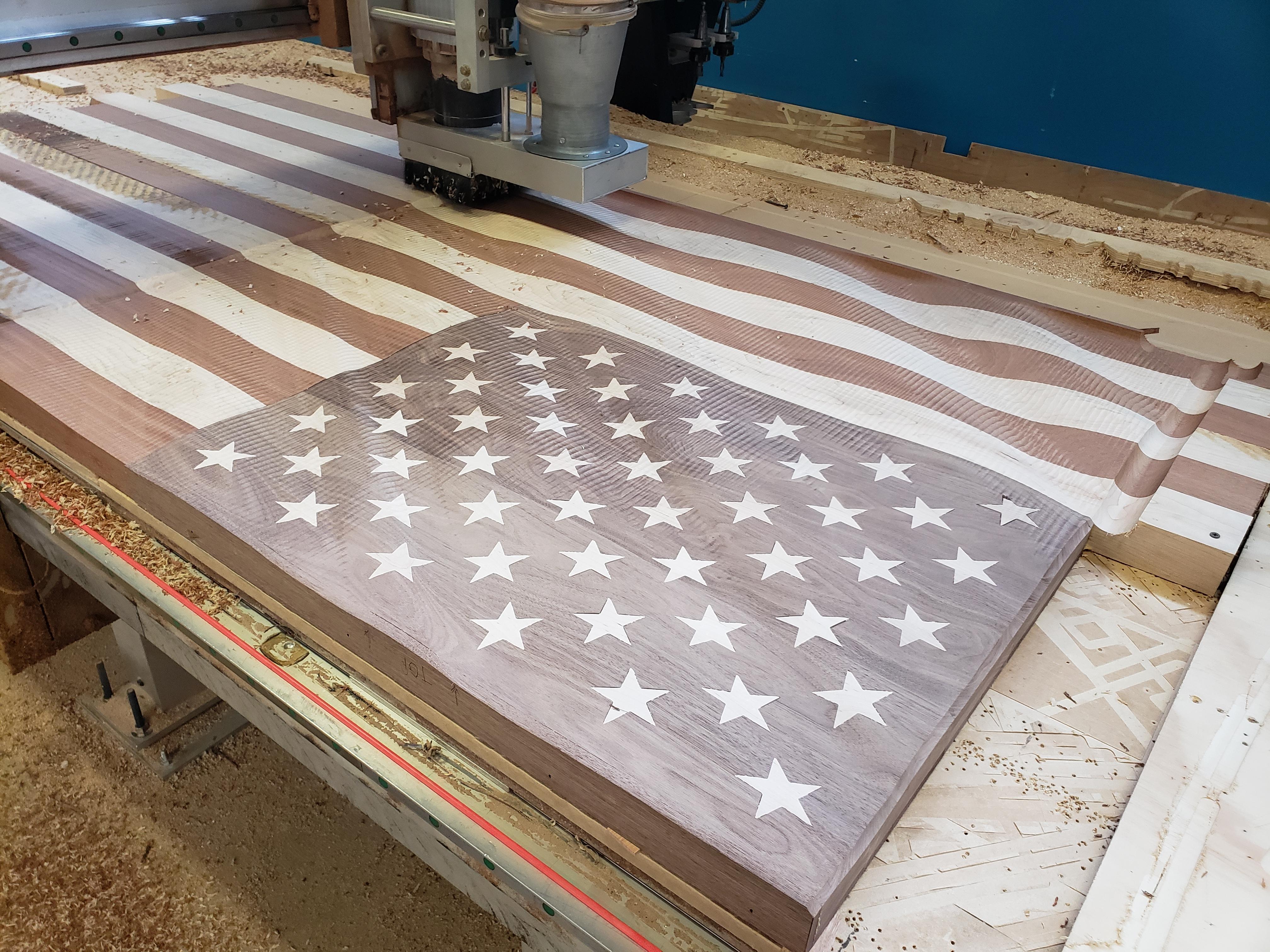
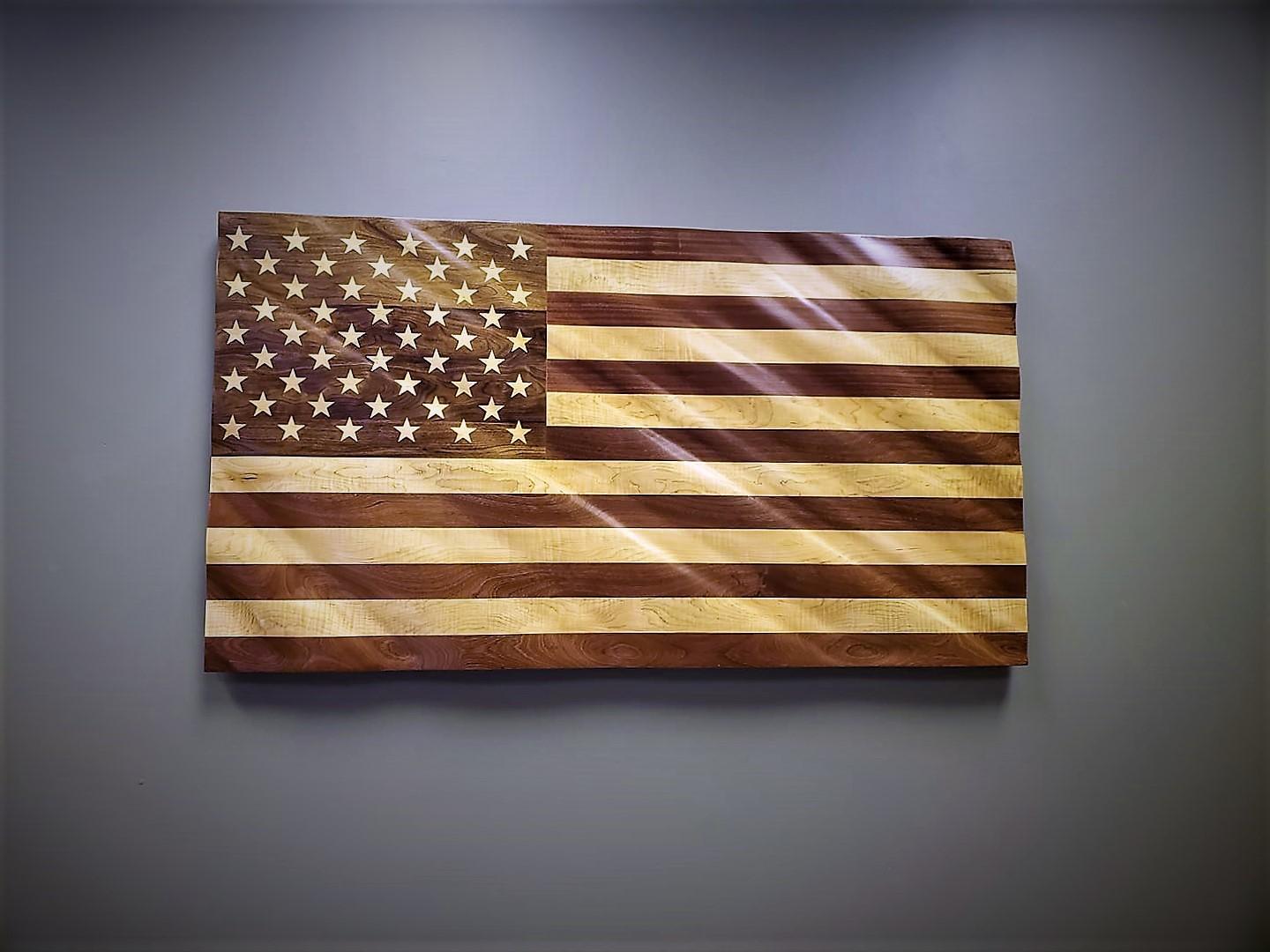
Steve Guenzel is used to challenges. His company, Advanced Stair Systems supplies stairs and handrails for custom projects in the greater Philadelphia area. “We specialize in creating reproduction handrails using the Tangent Handrail Method and 3D modeling, which is an art and science unto itself,” he said.
But he tackled a different kind of challenge when he started making flags that are made mostly of solid American hardwoods but look like they are flying in the breeze. “We have been making American hardwood flags for a few years now,” he said. “The original idea was a personal challenge to do better than a few that I saw on the internet. They make a stunning statement of beauty and patriotism.”
His most recent project really stretched the limits since the flag is 6 feet long and 2 inches thick.
“This particular flag is a lot larger than most flags we made previously and is 39”x 72” and 2” thick,” he said. “I had designed the waving profile a few years ago, and just had to modify a few things for the larger size. The stars are the greatest challenge, but I feel also they are the key element that had to have the right look to them. Getting the stars to a sharp point is difficult, and took a little trial and error, but in the end, I think we nailed it.”
The stripes are 3 inches tall with the white stripes crafted of hard maple and the red stripes from sapele mahogany. For the star field, they chose black walnut, using hard maple again for the stars.
“The stars are a little more than 2 inches point to point and ¾-inch thick, with care taken to align the grain correctly with the stripes,” he said. “They are cut out, and then inlayed into the walnut star field with a lot of precision, as any gaps or poor fits are extremely visible.”
Gluing up the parts of the flag requires three stages, then the whole thing is planed to the finish thickness of 2 inches.
The next step is what really makes the flag distinctive: carving the waves to make the flag look like it is flapping in the wind.
“The machining of the wave and the final cutout of the flag is done on our 22-foot CNT Motion CNC router,” Guenzel said. “For this project we used Aspire CAM software to program the CNC and Autodesk Inventor for the 3D modeling to get the wave just right.”
Guenzel says it is impressive seeing the flag take shape on the bed of the CNC.
“Watching the CNC cut the wave is amazing and is surpassed only by the spraying of the first coats of clear coat on the flags, and watching the true colors just pop,” he said. “This stage almost brings you to tears.”
For maximum effect, the flags use only the natural wood coloring.
“Cutting the waves across the wood brings out an interesting grain pattern and lets the natural beauty of the wood come out,” he said. “No stains are used on our flags, as the genuine tones of the wood are incredible on their own.”
This flag will be proudly displayed in the showroom at Advanced Stair Systems’ new shop north of Philadelphia. For more on the company, you can visit their website at advancedstairsystems.com.
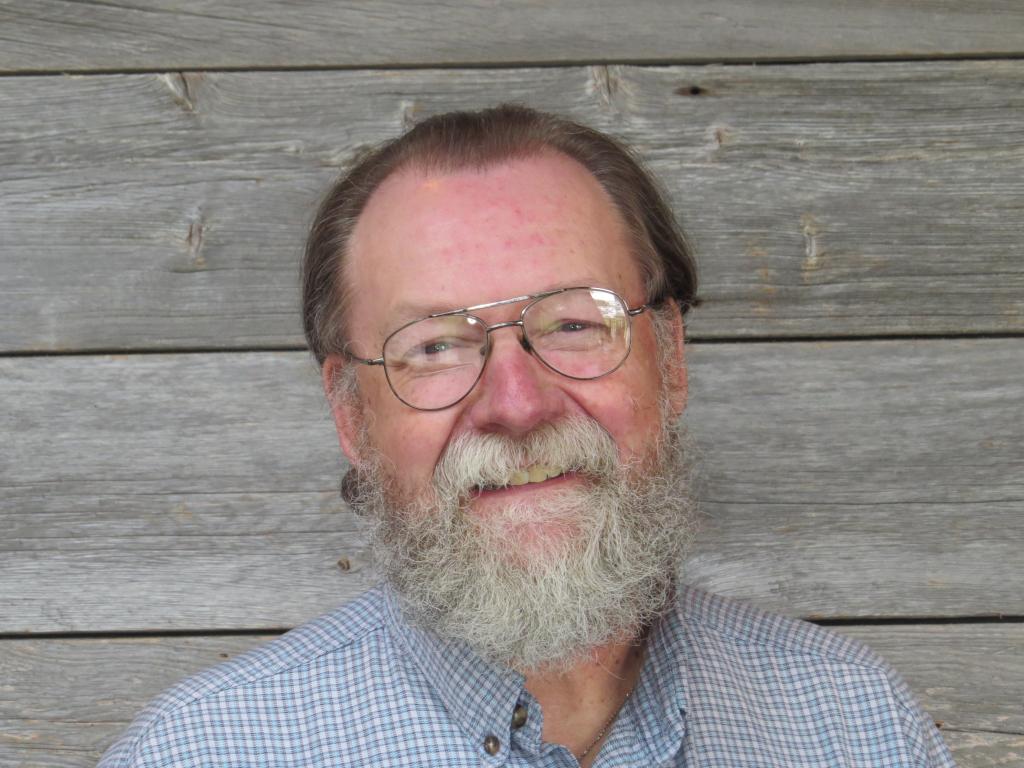
William Sampson is a lifelong woodworker, and he has been an advocate for small-scale entrepreneurs and lean manufacturing since the 1980s. He was the editor of Fine Woodworking magazine in the early 1990s and founded WoodshopBusiness magazine, which he eventually sold and merged with CabinetMaker magazine. He helped found the Cabinet Makers Association in 1998 and was its first executive director. Today, as editorial director of Woodworking Network and FDMC magazine he has more than 20 years experience covering the professional woodworking industry. His popular "In the Shop" tool reviews and videos appear monthly in FDMC.
Have something to say? Share your thoughts with us in the comments below.