HANNOVER, Germany – Digitization, sustainability and other smart technology for panel processing, solid wood, surfacing, finishing and other applications, for facilities of all sizes, was out in force for the 80,000-plus visitors in attendance at LIGNA, the world's largest woodworking show.
Stretched across more than 1.2 million net square feet, and featuring displays by more than 1,300 companies, the biennial LIGNA took place May 15-19 at the Fairgrounds in Hannover, Germany. Woodworking Network staff in attendance took note of some of the new, and innovative products on display.
Below are just a few of the products that caught our eye. More will be featured in additional articles and videos. Organized by Deutsche Messe and VDMA, the next LIGNA will be held May 26-30, 2025. For information visit ligna.de.
Read additional articles on new products showcased at LIGNA 2023.
Videos and photos showcase a few of the eye-catching innovations
New products shown by Biesse included the Hydrogen Force System (HFS) is an innovative bonding system for edgebanding. Using water, the technology leverages the hydrolysis process to create hydrogen – a sustainable energy source – to power the edge application process. Biesse says the technology reduces energy consumption and related CO2 emissions. Also making its debut was the Opera 5 high-performance calibrating and sanding system for small and medium-size shops. New corporate colors and nomenclature were also unveiled. (Watch a video of the HFS, above.)
Among the machines at Weinig’s booth, the new Hydromat 4400 offers planing and profiling at up to 400 m/min with maximum output. The unit is operated via a 21.5-inch display with Weinig Machine Control (WMC) which reduce setup time to a minimum. Large feed rollers, table rollers and pressure rollers ensure that the workpieces are guided securely and smoothly. The Hydromat was shown in conjunction with the High Performance Feeder with speeds of 400 m/min. The new WMC was also on several other machines. (Watch a video, above.)
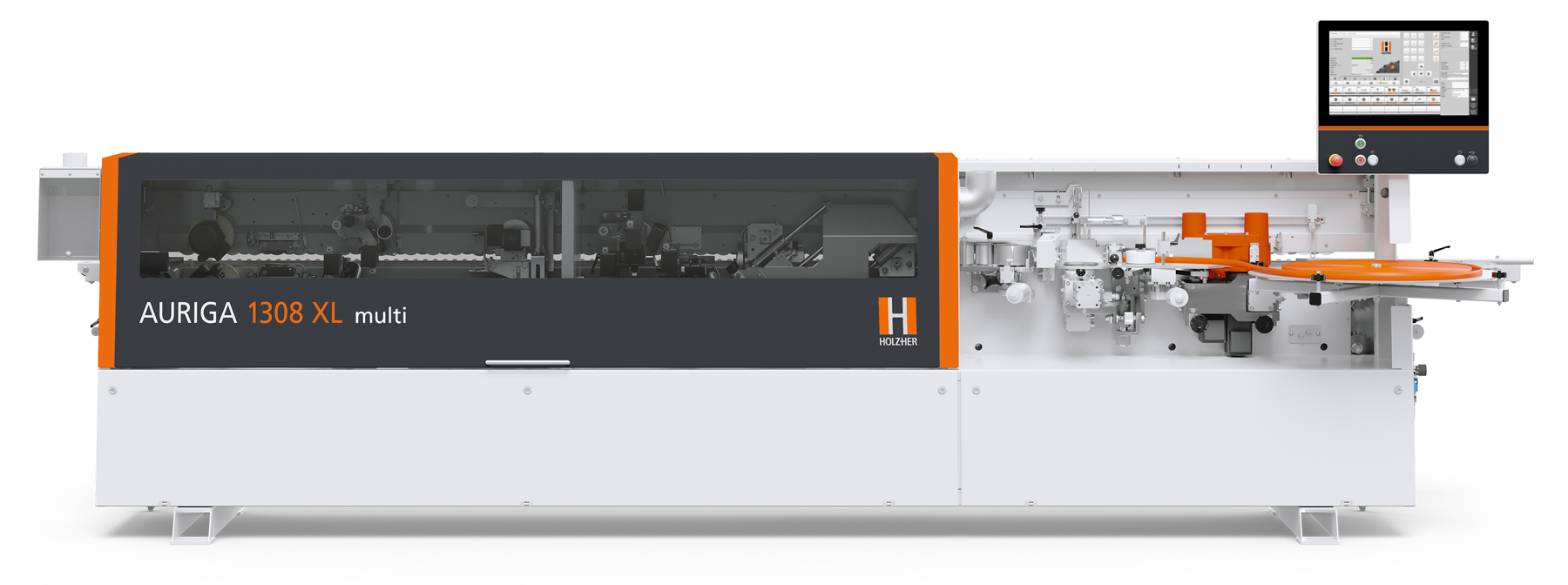
Holz-Her now offers the PinJet option on the Evolution, which allows for the driving of dowels pre-coated on both sides. After activating the dowel program, the steps of drilling, pretreating the holes and driving in the dowels are done automatically. Profiling, milling, drilling, engraving or complete machining of countertops are also possible. Also on display was the new Auriga 1308XL multi edgebander with the GluJet applicator system, for processing many materials (pictured above).
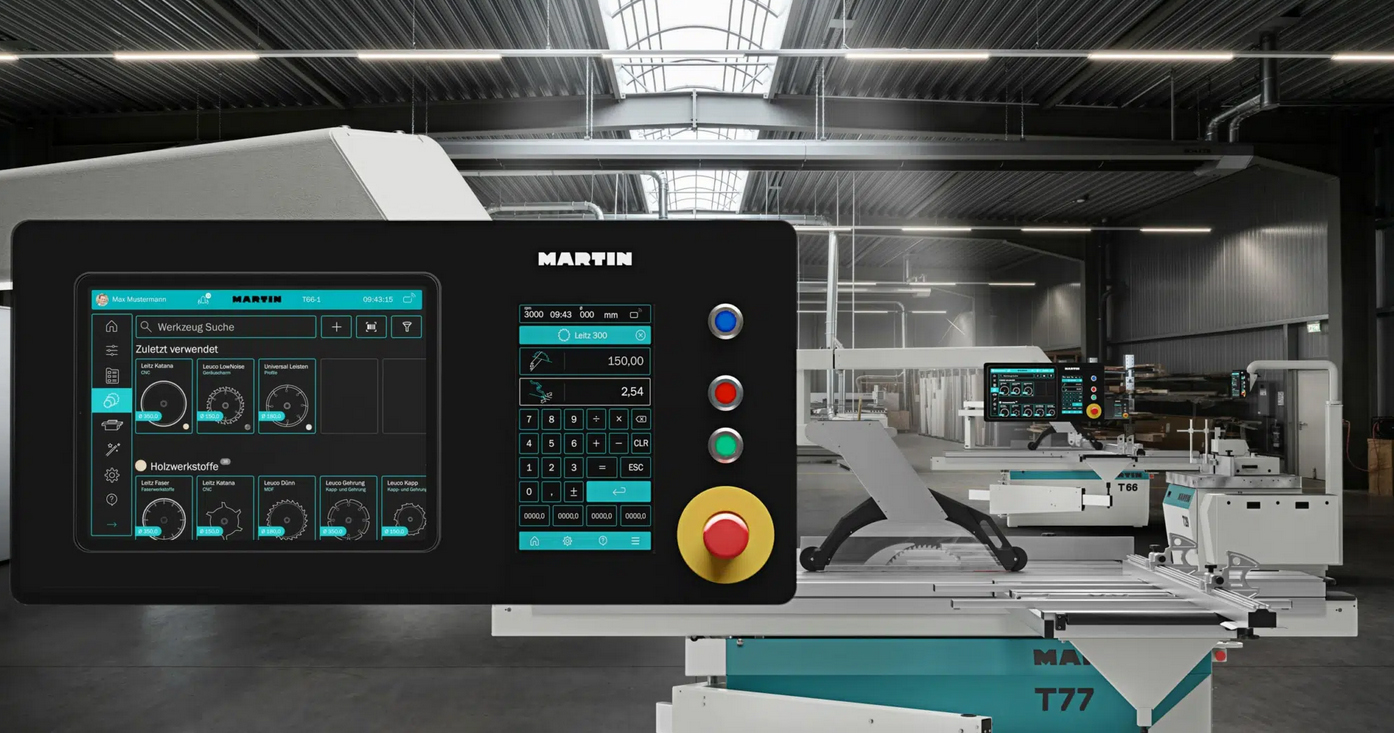
Featured at Martin was the ConnectControl concept for saws and spindle moulders. Using a 7-inch touchscreen, accurate axis adjustments can be made based on direct dimensional specifications or calculation functions, with quick access to all the machine’s functions. Machine operation can be enhanced with the ConnectPad, which attaches magnetically to the control panel, or with an Apple iPad Pro. ConnectApp allows for additional functions such as tool and order management or section planning. Data is exchanged between the user and machine through the cloud-based ConnectDrive.
Products by Altendorf included the award-winning Hand Guard, a certified and AI-controlled safety assistance system for sliding table saws. Two cameras monitor the area around the saw blade. When a hand gets too close, the blade is stopped and driven down in a maximum of a quarter of a second. No damage is done to the saw blade and the system can be operated again in about 10 seconds. The safety system also works with gloves, can handle nearly every type of saw blade, and is designed for virtually any material. (Watch a video, above.)
Along with a prototype of its flexible, fully automated edgebander magazine that can store up to 96 coils, IMA-Schelling’s new products included the IMAGIC L1, a highly flexible batch-size-1 throughfeed drilling machine with multiple configurations possible: pure drilling or any combination of routing, drilling, dowel insertion and hardware mounting. The new patented Zimmer transport system with circulating clamping grippers moves the panels in a permanent, fixed clamp through the entire workcell - even with multiple machining supports. The IMAGIC L1 can be configured either as a manually operated or automated drilling cell. (Watch a video of the edgebander magazine prototype, above.)
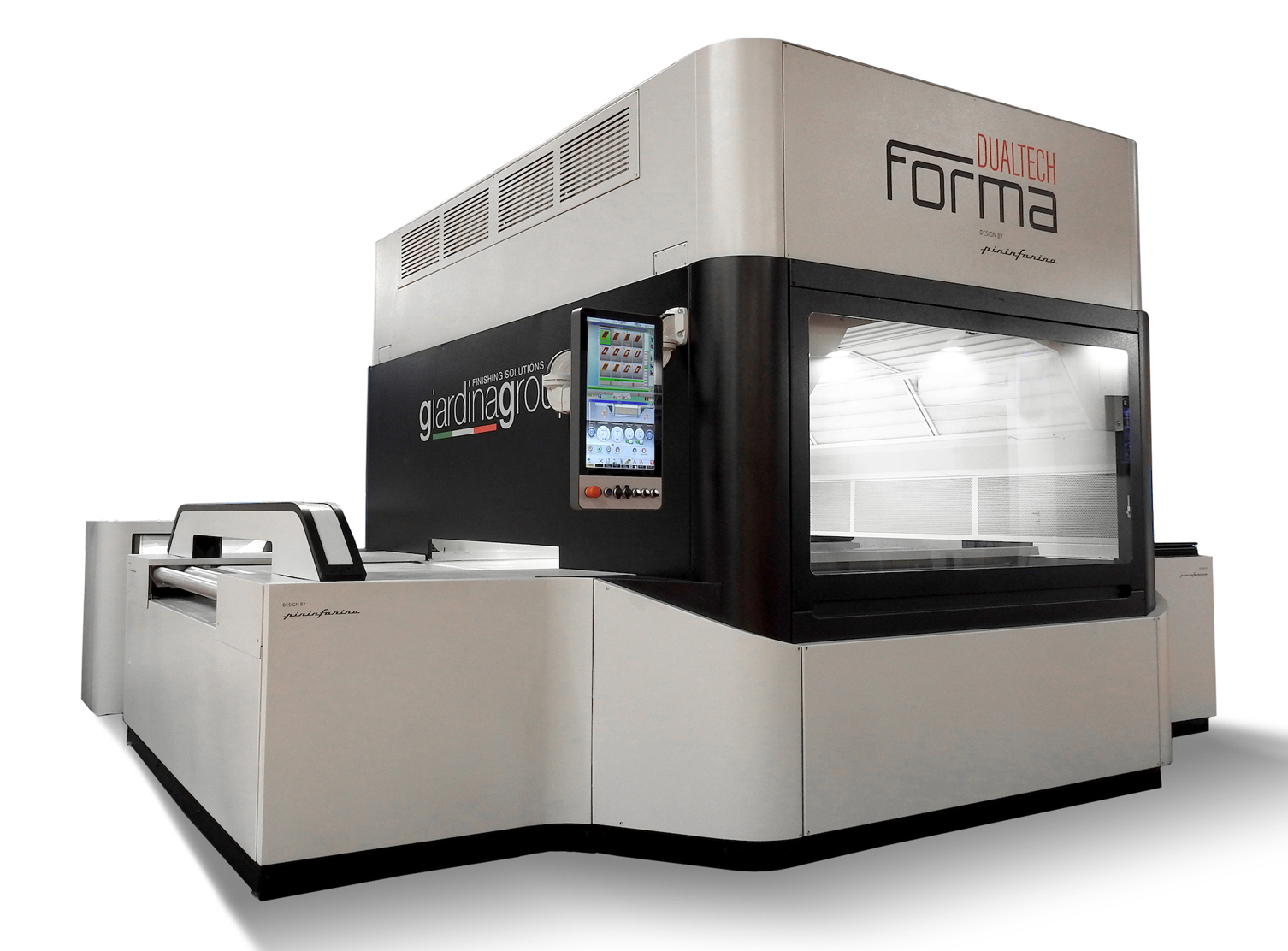
Giardina’s recently launched Dualtech Forma finishing system is ideal for medium to high production rates. Using two opposing reciprocating units that can hold up to four guns each, the machine can spray stain, primers and finishes onto smooth or shaped surfaces. It is equipped with a self-cleaning conveyor system plus convenient access to the painting area from both the front and rear. The Dualtech Forma also is fitted with two additional air distribution plenums that keep the spray booth under vacuum.
SCM’s Smart & Human Factory included new automation. In the beam saw area, the Gabbiani gt2 flexible cell was shown with an articulated robot for automatic loading and unloading. The Morbidelli cx220 CNC drilling and dowelling flexible cell, shown with a robot, can produce a panel per minute, up to 400 panels per shift with a single operator. Also making its debut, the “Blade Off” safety system prevents accidental contact between the operator’s hand and the blade. Smart sensors identify and recognize the human body and trigger the system if too close to the blade’s designated zone area. (Watch a video of the Blade Off safety system, above.)
Fagus-Grecon featured intelligent technology from its two divisions. For fire prevention, the new GreCon DLD 1/9 uses intelligent detection technology to detect sparks, glow nests and other hot particles, in any light/environment. GreCon’s intelligent extinguishing technology (IET) monitors the extinguishing process and can detect wear, clogged nozzles, etc. at an early stage. On the measuring side, GreCon's EdgeInspect is a quality control system for furniture edges and door frames that detects defects such as broken edges, missing or too short decorative strips. (Watch a video, above.)
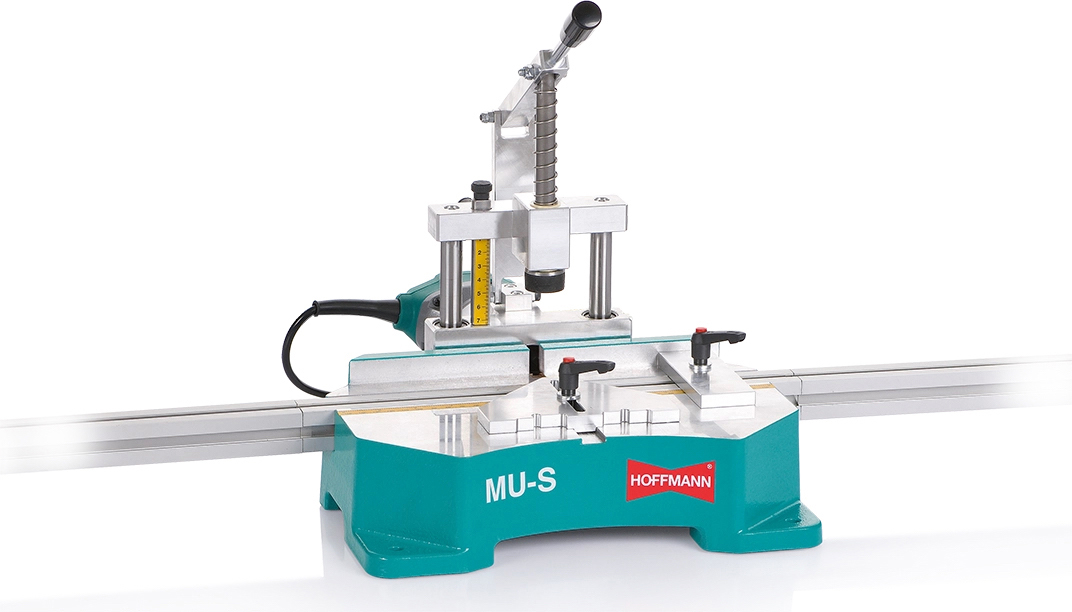
The MU-S manual dovetail routing machine was among the new products shown by Hoffmann. Easily transportable and lightweight, the benchtop model is ideal for use on-site or in the shop. It will rout a single dovetail slot per cycle, for Hoffmann keys size W-0/1/2/3, with routing depths of 0-55mm.
Partner with the Koch Group, Paul’s display included the Slimline pushfeed saw system for the optimized and automatic cutting at the saw of single or several boards. Another highlight at Koch was the new Lehbrink point-to-point throughfeed machine with a keyhole locking system and a stacked feeder. The machine can also be equipped with milling or routing heads. (Watch a video, above.)
Leuco’s regeneration technology enables the brazing out of the worn cutting tips on a jointing cutter and replacing them with new cutting edges. The company says the regeneration can be carried out several times, saving the user time and money. Leuco also showed its patent-pending concept for arranging cutting edges on basic tool bodies. Based on the Fibonacci principle, the concept was shown on several tool types, including a Z4+4 nesting cutter with a diameter of 12mm, the "SmartJointer airFace" and Leuco p-System cutters with exchangeable blades, and a disk finger cutter. (Watch a video, above.)
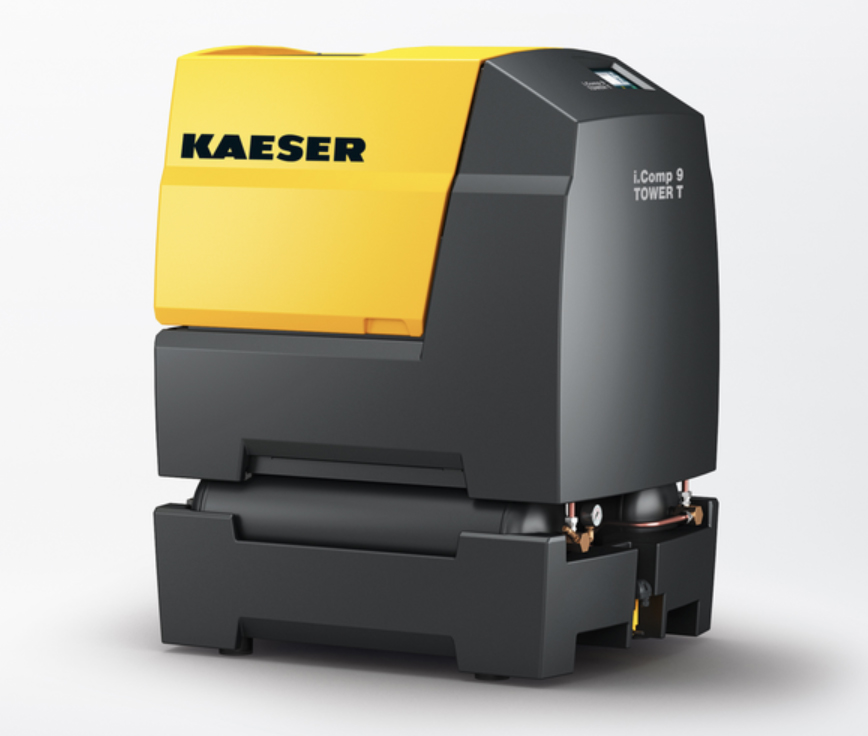
Kaeser’s new compressors include the space-saving i.Comp 8 and i.Comp 9 Tower compact systems, which feature a compressed air supply concept. The company says the reciprocating compressors are able to operate with 100% duty cycles and with a volumetric flow rate to 580 l / min, the i.Comp Towers can be used for a wide range of shops and applications, achieving a constant pressure of up to 11 bar with absolute operational reliability.
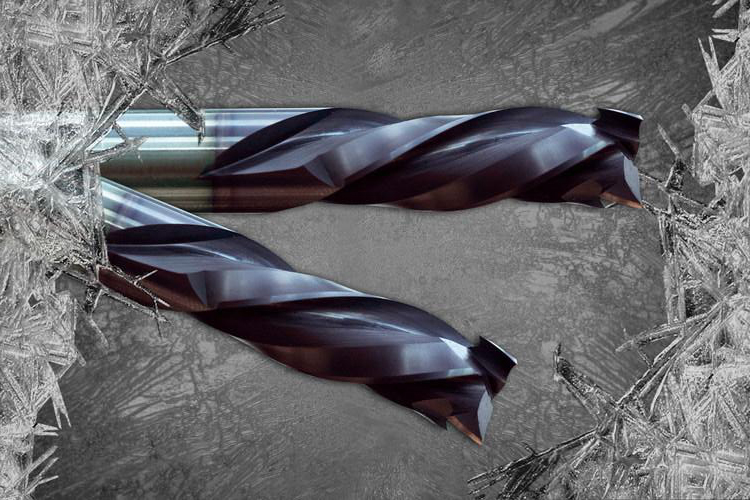
Freud's display included CNC router bits with Black I.C.E. coating, which helps cool cutting edges by shielding the solid carbide cutting edge by creating a slick, lubricant-like coating. Combined with Freud’s TiCo (titanium cobalt) hi-density carbide and Black I.C.E coating, the bits offer a sharper edge with precise cuts with less wear, resulting in 2X tool life, the company said.
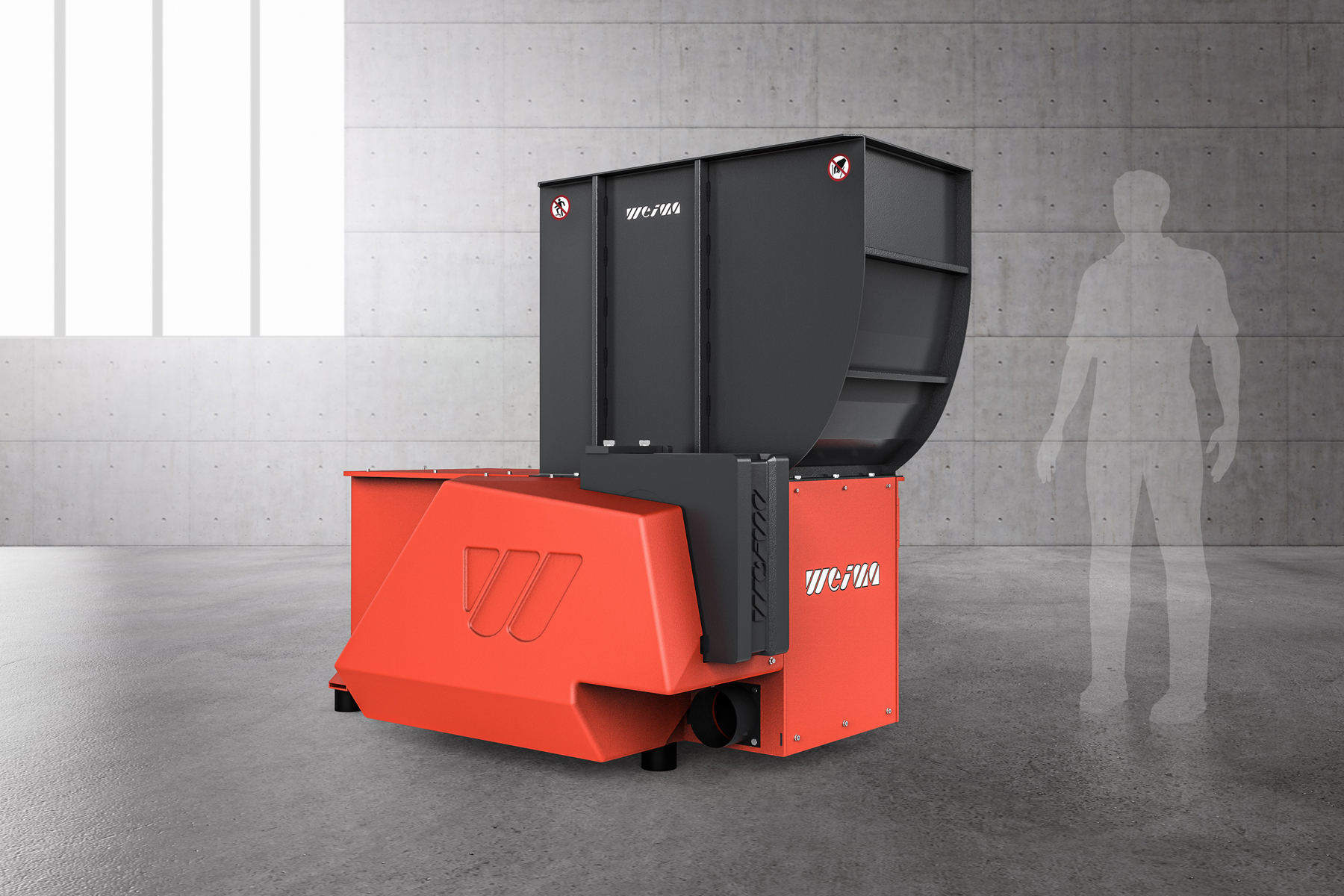
WEIMA showed a revamped WL4 single-shaft shredder at LIGNA. The new base frame of the machine now has a significantly more robust design and vibrations have been reduced to a minimum. Another innovation is the maintenance-free V-belt. To increase energy efficiency, WEIMA has also improved the hydraulic unit, which is protected inside the machine, and optimized the PLC control unit.
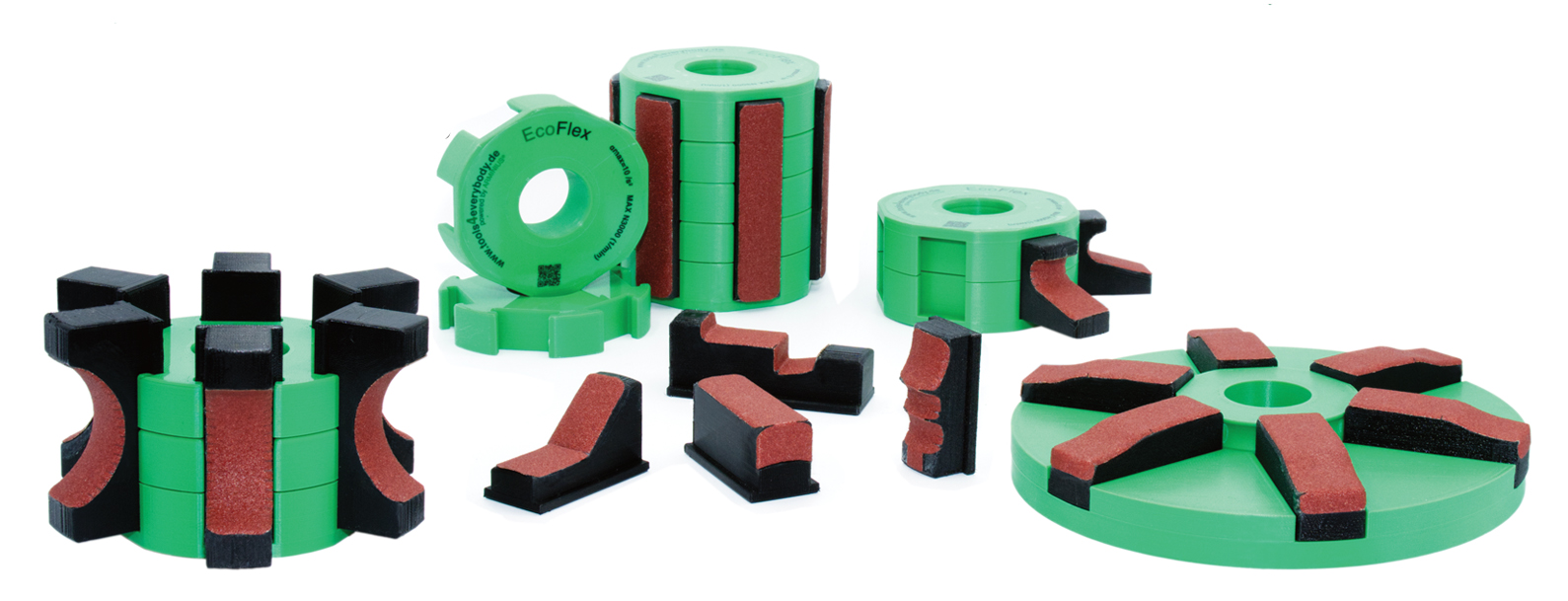
Arminius says its EcoFlex line of sanding tools are individually and easily online configurable. The tools are suitable for all types of wood and are ideal for small series, one-off profiles.
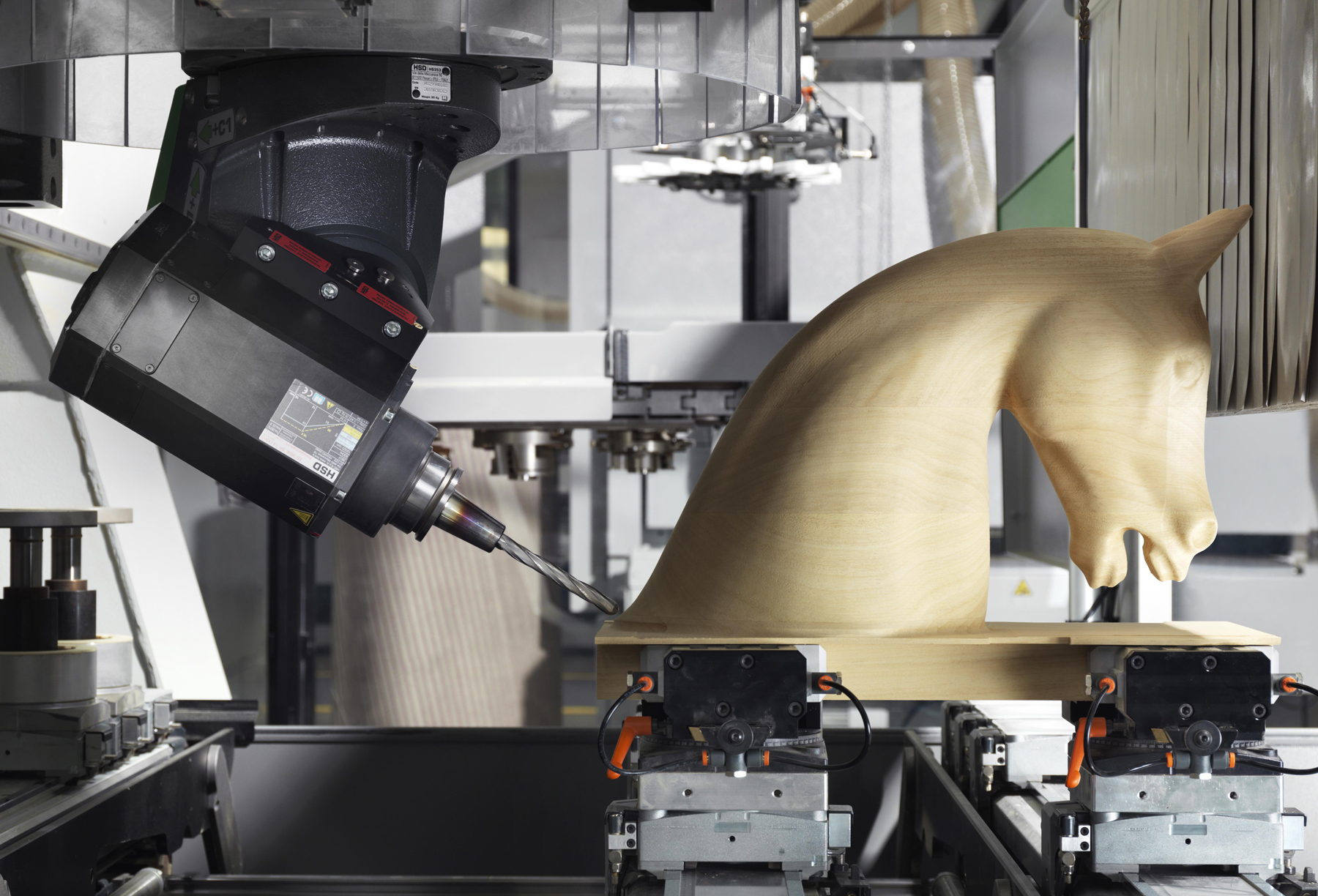
HSD’s products include the Wi-Fi ES951 range of electrospindles for 3-axis machining centers and robotic applications. The ES951 range allows interaction with the machine via IoLink, Ethercat or Canopen fieldbuses, and offers a version with an HSD-produced MEMS accelerometer and a thermal probe to monitor the temperature of the front bearings. The ES951 range also features an integrated IoT system, enabling connection to the My HSD IoT platform for a high-performance combination.
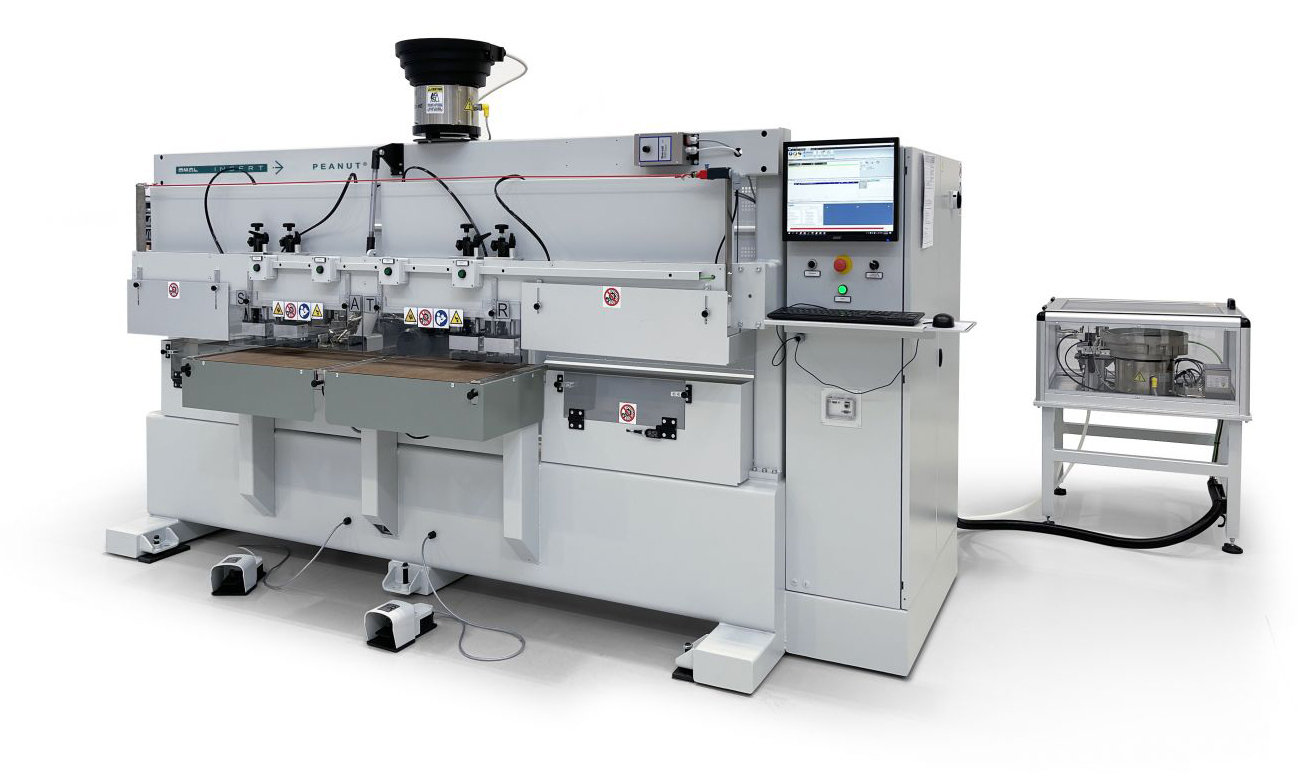
Products shown by OMAL (distributed in the United States by SCM) included the Insert Peanut, a 3-axis CNC machine for horizontal boring and peanut insertion as well as vertical face routing for peanut slots. It can also be equipped with drilling, gluing and a wooden dowel insertion unit upon request. The machine has a 1300mm worktable with 4 fields, indexable central and side fences with an open frame to machine parts up to 2600mm.
Keep watch for more innovations shown at LIGNA 2023.
Have something to say? Share your thoughts with us in the comments below.