Twenty years ago, Grandview Products Co. was nearly a 100 percent assembly operation outsourcing everything. Today, things are the opposite; the company produces, builds and assembles almost 100 percent of its product line.
"We are almost completely integrated," says president E. F. "Sonny" Zetmeir. "About the only thing we don't make is rigid thermofoil doors.
"Back in '70s and early '80s, the market was down and our company declined in size," Zetmeir says. "We couldn't give outside dimension plants enough business, so we had to do it on our own."
The switch helped fuel the company's current success. Today, Grandview, based in Parsons, Kansas, has its own rough mill. Sales were up 24 percent in 2004, and will be up about 19 percent in 2005. Zetmeir says the number-one reason for Grandview's growth is the strong cabinet market.
"We've been aggressive in the market, and we expanded our sales efforts, working with independent sales representatives," he says.
Grandview makes face-frame kitchen and bath cabinets, with mostly wood doors and frames, in 15 styles and 10 colors.
Seventy percent of Grandview's business is for multifamily buildings. Zetmeir says it's bid work and tends to be price sensitive. Many times it is one door style, one color, although on a condo project everything can be different, and apartment dwellers are getting more affluent. Countertops are usually included in these larger jobs.
"We used to do a lot of laminate slab-type cabinet doors, and now we're seeing upgrades, wood doors, raised panel and a lot of maple. They want a good-looking product. Because there's so much money involved, they tend to be very demanding."
Grandview ships cabinets from Alaska to the Caribbean, and from coast to coast. Zetmeir points out that Grandview is equidistant from either coast, and a truck shipment can be made to either coast in 36 hours.
Making cabinets
Grandview builds 1,700 to 1,800 cabinet boxes a day in the primary Parsons plant.
"We've gotten better at doing the onesy-twosy stuff than we ever were," production manager Chris Maffei says. "The dealer/distributor side has taught us how to handle smaller quantities."
The Cherryvale plant is treated as if it were a department in the main Parsons plant not a separate operation 25 miles away.
"It has the same lead times as if it were right here," Zetmeir says. "They get a daily cut bill. They run a truck over first thing in the morning and late in the afternoon. All pieces are palletized and skidded by order and are ready to move into the appropriate department." (Six blocks down the street in Parsons is a third plant that laminates particleboard for shelves on two laminating lines.)
All box material is laminated melamine saturated paper on particleboard. Work begins in Grandview's mill area, where there are two Holzma rear-loading panel saws (HPL 22 and HPL 33), two Holz-Her vertical panel saws, a Homag edgebander and a Brandt edgebander.
The face frame area is defined as a separate area of the plant where tenoned pieces come from Cherryvale. Mortising and drilling is done here on a recently purchased Accu-Systems HPM mortiser and drilling machine.
Face frames are assembled and put into a clamp. Both doors and face frames are sanded in a horseshoe-shaped sanding configuration that has two Timesavers sanders, both with Fladders. (Face frames are sanded on a second shift, doors and face frames both shifts.) Work is transferred on carts.
In Grandview's door assembly area, each door is hand assembled. Thermofoil doors are outsourced, one of few items that are purchased. Doors are built in groups by color and style.
Doors are assembled by hand, put in clamps and put in a black light booth to show excess glue. Then doors go through an SCMI Concept 2000 double-head tenoner to produce the final outside door profile. All parts come from Cherryvale except raised panels. A Jenkins Unique machine makes arched pieces, and a Voorwood A117 shaper/sander is also used.
Paint and assembly
Grandview has an overhead paint line that includes four steps in a 45-minute cycle time: spray stain application, vinyl sanding sealer application, overhead drying conveyor, sanding by hand, then application of catalyzed varnish for the complete process. It's dry at this point, but put on carts another hour so the doors don't block. Zetmeir is looking at ovens to add heat to that line, to get away from having to store pieces on carts and to reduce the possibility of pieces blocking in certain conditions. A similar overhead paint line is used in Cherryvale to coat small parts.
Countertops are also made in Parsons. The countertop shop buys laminate top blanks from two vendors. Tops are cut on a Midwest Automation miter saw. An Edgetech CTR960 router routs out sink holes.
Grandview uses two assembly lines for cabinet box parts, one for base cabinets and one for wall cabinets and special case cabinets. Cabinet assembly starts with the face frame, and then the cabinet is built up from that, using hotmelt adhesives, except for cold glue on the back. The company builds wall cabinets smaller than 42 inches on easels.
Interest rate concerns
Cabinet manufacturers have been watching interest rates closely. Zetmeir isn't too concerned yet, with relatively low rates. "In the short run, we may have a reaction," he says. "But people are still signing mortgages for not a lot of money. I don't think a couple of point increase would affect the cabinet market much."
Zetmeir says the multifamily market traditionally does better during times of higher interest rates. Recently, multifamily numbers haven't been good. "We have done well because we've been at it a long time, we do a good job and we have a good client list. We've diversified in condos, assisted living and student housing, and are seeking to expand single-family and remodel business.
"You have to create new products and diversify your offering with more styles and more colors," he says. "But I've also tried to keep us true to what we are. We aren't a semi-custom or custom company. We're a stock line.
"We want to do cabinets for the masses. We're not offering a $70,000 kitchen. We want to be a good value and we want to be perceived as a good value. We do a good job of delivering a good-quality, consistent product."
Zetmeir says that Grandview has also done a good job attracting good people. The company employs 400 people in its three southeastern Kansas locations. Despite the rural location, Zetmeir says it can be a challenge finding people who can pass a drug test, so Grandview has an active drug testing program.
"Drugs are something you don't run away from by moving to a small town," he says. "A group of employees came into my office and requested a drug testing program, because people might hurt themselves or others."
"We're more careful in the hiring process than we've ever been," says Maffei. "As high speed an operation as we are, we need people who are going to be pretty high energy.
"We do a lot of cross-training in the shop; many people know how to do a number of things."
Grandview may put in a medical clinic on site to help employees on a day to day basis, as one way to reduce healthcare costs.
In the future, Zetmeir intends to make big layout changes in the main Parsons building, including making the assembly lines longer by adding conveyor length and moving them so there is more room at the shipping end to package cabinets for dealers/distributors.
As far as the product mix, no major changes are planned. "We're probably more semi-custom than we would like to admit," Zetmeir says. "Most stock line companies are. It's kind of a blurred line."
But he is optimistic about the future.
"I think we're a bit more nimble than some of the big guys are."
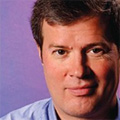
Karl D. Forth is online editor for CCI Media. He also writes news and feature stories in FDMC Magazine, in addition to newsletters and custom publishing projects. He is also involved in event organization, and compiles the annual FDM 300 list of industry leaders. He can be reached at [email protected].
Have something to say? Share your thoughts with us in the comments below.