Bring on the tough jobs. At New World Millworks, they want the custom and complicated projects.
"We work to fulfill the clients needs from design drawings to carefully engineered functional products," company president Eric Peterson says.
"We give innovative people the opportunity to come up with a good program. The wilder it is the better. People respond to that. It makes life interesting. People rise to the occasion."
Peterson says the Castle Rock, Colo., company offers a versatile product mix and an ability to respond to shifts in production or to accelerate production in different areas. That flexibility was upgraded recently with a new location and new plant layout. (The company name comes from Steve Miller's 1969 Brave New World album.)
Challenges and software
"Every project has something challenging about it," Peterson says. "Even if it's a repetitive item, we'll break it into smaller work packages. That improves our ability to start feeding product to a job as needed. Work packages can be any logical work grouping or set.
"Project manager and engineering work together to determine the most effective way to group or batch. We typically schedule a three-week duration for product in the shop. But we have the ability to accelerate that to a matter of days, if needed."
"All our jobs at New World have challenging conditions in veneer quality, hardwood requirements and specialty hardware," says Mike Slater, plant manager. "The work must be done as a team, (including) project managers, plant processes and installation. If we don't coordinate all these groups together, nothing works. Timing is everything when it comes to meeting the contractor's deadlines."
ShopPak is used to take larger jobs and turn them into smaller work packages, making it easier to track labor and material costs. It keeps track of which department a job is in, and how much has been completed.
"We believe that if you put enough work in front of someone, they'll get more than enough done," says Robert Hott, general manager. "ShopPak allows us to be more productive than most scheduling software I've seen."
Robert Frazier, engineering director, says engineers have two computer screens so they can work with Pytha 3-D modeling software and AutoCAD architectural drawings. "Having AutoCAD on one screen and Pytha on the other allows the engineer to work more efficiently," he says. "Pytha lets us take their concept and put it into a structure that allows us to build it.
"With Pytha you're actually building a model as you would on the floor. You're taking a part, identifying it as a part, material, edgebanding, and you're putting those parts together, as if you're building it in an electronic space. You can see where your tolerance problems would be, get a true three-D model."
Move and alliances
In April, New World moved about 10 miles to Castle Rock, Colo., increasing plant size from 30,000 to 100,000 square feet. Almost all of the 60 employees made the move.
"The old facility was our constraint," Peterson says. "Every time we tried to push more through that space than it was capable of, we didn't do well."
"Having more space has made a huge difference in the amount of work we can handle," Slater says. "Staging the finished product in the warehouse helps to make sure the product is complete and up to our expectations. We have the ability to bring more machines and increase our workflow, and we have increased the size of the finish room."
Hott says the move itself went better than expected. "We worked a night shift to create material backlog in case the machines were down to keep production employees busy."
The shop shut down on Wednesday, moved Thursday, Friday and Saturday, and by Monday the company was 50 percent productive.
Because New World had two saws, routers, etc., they were able to take one machine to the new site ahead of the move. Teams were established, and people took care of their own areas, evaluating what they would need and packing their own materials.
Peterson says there are three lines or cells in the new plant: custom wood products; lumber products; and casework. Stiles Machinery produced the plant layout. He credits alliances with companies like Stiles, Sherwin Williams, Application & Coating Solution and Dantherm with helping New World succeed. "Aligning yourself with the leaders in the industry is the road to a successful installation," he says.
Since 1994, Peterson also has benefited from membership in the Architectural Woodwork Institute. "It's one of the best decisions I've made," he says. "I can get out there and see what's going on, connect with leaders in the industry and work with the AWI Best Practices Group. It's the best resource out there."
Two of everything
Peterson likes redundancy, so New World has two each of edgebanders, CNC machining centers, dowel inserters and case clamps. The equipment includes two Holzma panel saws, an HPP 82 Optimat, Homag edgebanders, and a Weeke Optimat BP145. Peterson describes the latter as a workhorse, but one that will be updated to a new BOF when New World's veneer capability is added.
A new Weeke Optimat BHP200 is used for nested-based manufacturing, and has a Systech automatic panel loader, pushes finished pieces off the table, and prints labels that can be put on each piece. "It's very productive," Peterson says. "One operator stays busy unloading parts."
In the solid wood area, a Weinig Profimat 23E moulder is used for small runs and quick changeovers. New World is planning to add another larger moulder for longer production runs, and will add a second ripsaw. In the glue-up area, there are also plans for a new V-grooving machine to join a Pistorius miter cutting machine and a Butfering Classic widebelt sander.
Other equipment includes a Midwest Automation laminating line with glue spreader and layout table, Scheer drill and grooving station, and Accu-Systems dowel inserter. New World does its own laminating, except for melamine panels supplied by Roucke Inc. A Kaeser SFC 37T air compressor can provide as much as 20 percent of the heat when needed.
In a separate large finishing room, New World uses two spray booths provided by Application & Coating Solution. A Makor inline sprayer is used for runs of trim from 300 or 400 lineal feet to spray stain or varnish. New World is also looking at a larger finishing line. Sherwin Williams conversion varnish and stains are used.
Veneer next
Peterson sees more demand for veneer in all areas. A new 5,000 square foot room for veneer processing is next on New World's agenda, and it will provide a higher level of control over schedules and improve the ability to do special jobs. It will have veneer storage, clipping, guillotine, splicer or stitcher, and layout tables. A new veneer press will also be added.
Countertops are often included in jobs. In the countertop area of the plant, New World builds blanks and glues tops. A Midwest Automation countertop saw is used. They are switching to water-based glue for countertops and laminates. New World outsources solid surface fabrication work, and Peterson says that builders are comfortable ordering stone direct.
Peterson has a challenge for everyone. "Now that we have more space, we want everybody used to doing more sales, and we want to change the mentality that 1,200 hours used to be a lot for us. Now we're looking at 1,400 or 1,600 hours a week or more as normal. In the old facility, that couldn't be done."
"Growth has to be a controlled, continuous process and takes time," Peterson says. "Adjusting to contractor changes in schedule is always a challenge, but one we pay particular attention to. In our industry there are a lot of punches we have to roll with. We have to be able to adapt to changes quickly. That's one of our strengths."
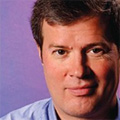
Karl D. Forth is online editor for CCI Media. He also writes news and feature stories in FDMC Magazine, in addition to newsletters and custom publishing projects. He is also involved in event organization, and compiles the annual FDM 300 list of industry leaders. He can be reached at [email protected].
Have something to say? Share your thoughts with us in the comments below.