Gerhard Loeffel wanted a good place to work for his employees.
"I'm a firm believer in creating a nice work environment for my employees, so we can work as a team together and create a great product," says the principal and co-founder of Case Group LLC, Case Window and Door.
It was Loeffel's goal from the start to build a top-notch window factory based on European design, including the furniture, doors and windows. The 48,000-square-foot building has 4,000 square feet of glass, and is located in a park-like setting amid trees and water in Green Island, N.Y.
"Construction of the building is different than a standard production building," he says. "If you make your environment beautiful, people want to work here."
No wonder other woodworking companies in the area dubbed the company "the country club." Loeffel accepts the compliment. "Definitely we're a country club compared to them," he says.
Large, high-end windows
Case Window specializes in large, high-end windows and doors for private houses that may cost $5 million or more to build. The company was started in nearby Schenectady in 1993 by partners Loeffel and Russell Brooks. Loeffel and Brooks met while coordinating on several projects and decided to combine Brooks's sales and marketing background with Loeffel's manufacturing experience.
At that time, Loeffel says the pair approached banks with their business plan of reaching this highest market level. But the banks, with the exception of one, didn't understand the potential of the high-end market.
The customers did understand. From Maine to Florida, and from Martha's Vineyard to Jackson, Wyo., there were plenty of takers for the Case Window high-end products.
"What we do best is to solve complicated design problems posed by the architect," Loeffel says. "We're offering the capability of designing very complex things, and we are able to manufacture a very large product range."
Production of profiles
Case Window works from standard profiles, but every project has some amount of customization. The shop uses AutoCad, AlphaCam and 3E, German-made software that handles everything from sales to programming the CNC machine. The shop is metric.
Solid wood is the basic material, often domestic and tropical hardwoods, sometimes with aluminum or bronze cladding. Production is based on 5/4 lumber. Teak, sapele, white oak, mahogany and cherry are some of the species used.
The U-shaped production layout starts at the loading dock. Every piece of lumber is quality checked and labeled. All incoming wood sits for two weeks. Loeffel says this acclimation period improves consistent moisture content in all pieces. Case has a variety of hardwood vendors, including Rex Lumber.
In the rough room, pieces are cut to length on a Whirlwind saw with TigerStop positioning system, then go to a Weinig Profimat 22N moulder, which is used for S4S. A SAC Sueri jointer and planer straighten bow.
Each piece is sanded, then pieces are sorted for lamination. Urethane glue joins three pieces of lumber together to make a 72 mm system, which comprises the basic stock used to make window components and allows Case to glaze anything from a standard 1 inch glass to 1-1/4 inch glass. Case switched from mortise-and-tenon construction to dowels for the higher glue area.
After gluing, components are set aside for a day, then fed through the moulder for another S4S run, and then are sanded again.
The machining area features a Routech 240 machining center, with three-axis and five-axis head, drilling aggregate and capacity for 74 different tooling heads. Frame profiles can be cut in one pass on the 22-by-5 foot bed.
A Gubisch Centromat is a programmed 10-head shaper used for perimeter milling. There are also two Stegherr joint cutter machines that make the window muntin crosses. Panhans shapers are used for some jobs.
Case Windows' spray room has overhead conveyors, exhaust fan and air makeup system, and the room has its own humidity zone. There is a 14,000 cfm flow, but it feels like a cool breeze. Water-based finishes provide a heavier finish for windows and doors.
In the product staging area a vacuum wall allows large pieces of glass to be set in the window frame. Case also is installing an overhead crane. Quality control is done in every stage of production, and glass can be rejected for the smallest defect. A metal shop on site can cut, weld and machine steel and aluminum extrusions.
Future plans
It may be a country club to some, but Loeffel isn't completely satisfied. He always wants to streamline production and improve material flow.
"Glazing, hardware and material handling are areas that could be improved, along with a 20,000-square-foot expansion for wood storage and expanded metal product capability."
Broadening of the product line and expansion of the company could lead to a faster time to market, which also is a goal.
One thing that won't change is Case Window using its own building as a sales tool.
"We bring high-powered clients that associate themselves with a certain level of quality," Loeffel says. "When they see this level of detail they know we can deliver."
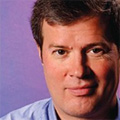
Karl D. Forth is online editor for CCI Media. He also writes news and feature stories in FDMC Magazine, in addition to newsletters and custom publishing projects. He is also involved in event organization, and compiles the annual FDM 300 list of industry leaders. He can be reached at [email protected].
Have something to say? Share your thoughts with us in the comments below.