History is essential to the story of the George J. Rothan Millwork Company of Peoria, Illinois. A story 150 years in the making that was written by the thousands of workers who walked the same floors and climbed the stairs of the two-story woodshop.
It was upon the shoulders of these workers that the company forged ahead through good times and bad to reach its sesquicentennial anniversary. Today, it is a successful millwork and woodwork shop that venerates the past while working in the present and considering its future.
The home of the Rothan Planing Mill sometime around 1873.
“I love this place,” said George J. Rothan, the current and fifth George J. Rothan to run the company since the first George J. founded the company in 1873.
Rothan, better known since childhood as JJ, has played amongst the wood and tools for most of his life. It was the same for his father before him. “My dad was working down here since he was nine years old, you know, running around and doing things,” Rothan said.
Current family members have worked at the shop. His son worked at the business for several years before changing careers. Brother Chris was a company VP before moving to Indianapolis to work for a general contractor.
Moving forward, Rothan said, the company will face some challenges including keeping alive the tradition of a Rothan owning and operating the business or continuing to operate in a more than 100-year-old two-story building. “Is that going to be possible, I’m not quite sure if it’s going to be possible to keep it going another 25 or 30 years, or however long it can go.”
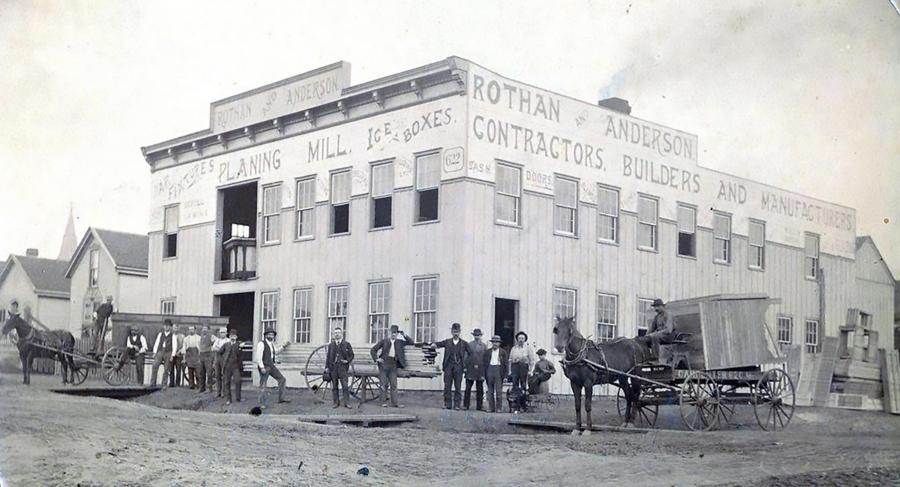
“Waking up every morning, sometimes you’re like, ‘I got to do it again, you got to go back’ and it is hard because you’re trying to please a lot of people. At the same time, it’s a challenge that is rewarding because you know that you’re basically doing that for all the people that came before you.
“I mean, when you’re talking 150 years in operation, it’s unbelievable,” he said. Not too many people can say that they are covering 150 years of work that somebody laid out back in 1873 when the original ‘George’ made the move from Cincinnati, Ohio, to Peoria, Illinois, on a horse and buggy.
“You don’t think about it very much,” he said, “but when you do it is amazing. And that is what makes me want to work to ensure that the business stays in the family. That’s what drives me.”
A historic project
Over the years the company has manufactured a vast range of goods and worked on many major projects throughout the Midwest and throughout the country. From crafting bars before the prohibition to building windows for a home-building company after the World War ll, the company has adapted to the needs of its community.
The city of Peoria, which is about three hours south of Chicago, has been one of its clients. More than 130 years ago, the city put out for bid the building of its City Hall, and the Rothan company was the general contractor on that job.
“That building was built from the ground up by Rothan crews,” said Rothan. “We did all the exterior work, you know, the concrete and all that brick. And then, we did all the interior woodworking [including the wainscot paneling, doors, railings, and trim].”
Fast forward to 2014, when the city wanted to restore the City Council’s chambers. “We went in and removed what we put in 100 years ago,” said Rothan. “We made new wall paneling, new doors, new frames, new casing, new trim. We went in there and brought it back to what it was 100 years ago.”
- Price tag for the city hall job 100 years ago: $18,000.
- Renovation of the council chambers: more than $100,000.

As they were taking apart the old paneling, workers found more than century-old pictures of retired co-workers hidden in the walls during the initial panel installation. “So, when we installed the paneling, we took a picture of our employees and left it there. So, if Rothan ends up redoing the council chambers in another 50 or 100 years, future workers might find our pictures.”
The company operates out of the 20,000-square foot facility — ten thousand square feet per floor — where it does laminate cabinet work for commercial jobs as well as solid wood projects, including recent hospital and library jobs.
The company has 14 employees including seven full-time union carpenters and one union carpenter who is also a project manager and shop foreman. The company also has three draftsman/project managers, an office manager, and JJ, the president.
The longest-tenured worker is Jim Kieswetter who has worked at the company for 36 years. Kieswetter, the carpenter-project manager-shop foreman, remembers his very first day.
“The first day on the job I was in Iowa at a college, and we were making a bunch of partition panels for cubicles,” he said.
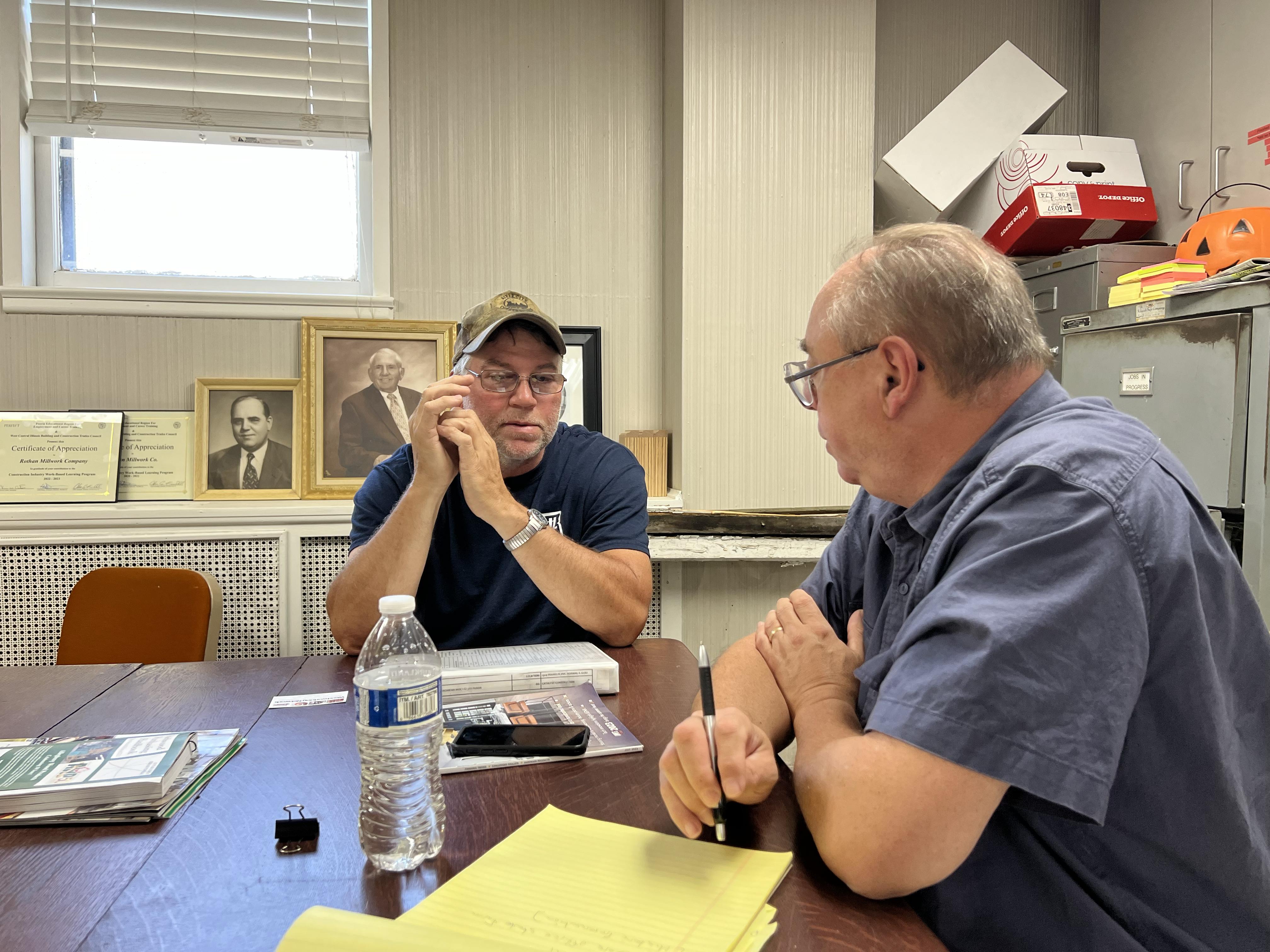
Today, Kieswetter said that work is very similar from then until now, except that they “used to run a lot more actual wood back then." And now it seems like there’s more solid surface and plastic laminate work.
When he started, the company had no edgebander, and the edgebanding was put on by hand. Today, the company has two Holz-Her edgebanders to do most of that work. One edgebander applies hardwood edging and the second does 3mm edgeband material.
The company 14 years ago purchased a Comec CNC rou
ter that does a lot of the radiuses as well as flat panel work. The company has become very adept at programming to get the most out of each board and machine the raw material as efficiently as possible.
Before that, said Rothan, a lot of radiuses were done on the company’s oldest piece of equipment in the shop, its band saw. “This piece of equipment probably hasn’t moved for over 125 years. And we still use it every day.”
Work flows from floor to floor going through a power moulder and saws, getting edgebanding applied, holes drilled, and components machined. Throughout the factory, there are power moulders and a variety of saws. Handwork is still prevalent.
The multi-level structure poses some difficulties. “One of the biggest challenges that we have is moving stuff from one floor to the next. It takes a good 10 to 15 minutes to move things. We have two hoists on each side of the building, we have one here that’s on on the alley side and then one that’s on the street side. After everything is built, it goes to the loading dock.
“We’ve utilized every ounce of space that we can in this building,” he said.
Rothan said that operating out of a building that has been occupied for almost the entirety of the company’s existence has its advantages. But, it has disadvantages as well.
Does that mean the company might move to a more
moder
n building?
“That is something that we’ve looked at and considered,” said Rothan with one eye to the past and the other to the future.
“One side of me says, ‘All right, we have to move if we’re going to get better and compete with the other people.’ The other side of me says, ‘If we were to leave, we leave all this history behind.”
Have something to say? Share your thoughts with us in the comments below.