Improving its manufacturing process and using lean techniques helped DeLeers Millwork efficiently complete a large job for a modern high-end hotel.
DeLeers worked on this project for theWit, a new 27-story boutique hotel in downtown Chicago, for almost a year.
Tom DeLeers, vice president of DeLeers Millwork, says the company was chosen for the project because of its ability to produce quality high-end products, the ability to work within short lead times, and a very competitive bid. The Green Bay, Wis., company also has the production capacity and capabilities to meet the demands of such a large project, and a good relationship with the general contractor.
“We provide a high level of customer service through proper communication and the level of our experienced staff,” DeLeers says. The company’s slogan is: A closer fit. A better finish. “We are that ‘closer fit’ because our level of experience makes it easy for us to identify and understand our customers’ needs.”
“We also make sure that our customers are satisfied at the end of the project and that everything is completed up to their standards,” he says. “No loose ends. Our goal is to develop long term relationships that thrive into the future.”
For the Wit Hotel project, DeLeers made a variety of pieces: kitchenettes, bathroom vanities, closet shelving, lobby registration desk, shop display cases, drapery valances and wall paneling for 270 guest rooms.
The registration desk offered some challenges. “There were many different materials being used on the registration desk,” DeLeers says. “We had to be sure that everything fit together perfectly within what we had built. Everything was coordinated properly so it would come together perfectly the first time.”
Rift white oak was used for some surfaces. The hotel room kitchenettes required a high-gloss lacquer finish, which was more difficult than typical finishes just because of the high gloss factor.
Four production areas
DeLeers says the millworker’s vision of lean is not specific to any one project; it is throughout the entire operation so it affects every job that they do.
“The overall flow of our production was restructured from the front to back,” he says. “Simple as it may sound, it helped to reduce the time spent transferring items from one department to another.”
The company also changed how it ordered materials.
“We worked with our suppliers to have materials stacked and sorted properly for how they were to be machined,” DeLeers says. “Now, if we have a unit of sheets come in from a supplier, they are already sorted in order of how the sheets are to be machined. We have made internal lean changes, but it is a matter of having our suppliers change with us also.”
DeLeers Millwork is divided into four main production areas: a machining department; a casework department; a custom product department; and a finishing department. Anderson CNC equipment, Olympic edgebander, Giben panel saw, Biesse Rover, and Koch dowel and bore equipment are the primary machines.
“All of our products start their life in our machining department,” DeLeers says. “We try to utilize our machines as much as possible because of the precision that is required with our products. This area produces parts for both our casework and custom departments.
“Our casework department is unique and is set right up within our machining department. Making this switch created much faster product turns for us and reduced the amount of inventory that is needed on hand. It also leaves very few parts in queue waiting to be built.”
The custom department is very hands-on and labor intensive. This area employs the company’s most skilled craftspeople. The machines can only take the product so far and then it requires some human finesse to get it to completion, DeLeers says.
Finishing flow
The finishing department receives products from all other areas. In the finishing room there are multiple spray booths along with downdraft tables and a large oven for curing the products. Many of the materials for the Wit were hand sanded, and a Global Finishing Solutions dryer was used to create a harder, more protective finish.
Among recent improvements is a major change in the overall flow of the finishing department.
“All items used to come in and out of the same door which was a huge flow issue,” DeLeers says. “It added extra time daily just to get items shuffled around to finish. We created a circular flow in the department which greatly increased our capacity. Along with that, we moved some of our finishing equipment around to accommodate the new flow and also help to increase the quality of our finished product.
“When we completed this project, we had doubled the size of our finishing department while reducing the amount of time it takes us to cycle products through there.”
Changes to the casework area helped reduce cycle times and turns.
“In our custom department, we restructured and created a circular flow with production cells. We have different pods set up with the necessary tools for four custom employees. We also have another area of our plant that is being restructured to support more custom employees. This will be for future expansion into that market and will be able to house another six employees.”
Challenges and improvement
“DeLeers Millwork is on a continuous improvement journey which means our improvements are never complete,” Tom DeLeers says. “When an improvement is made, it is only a matter of time before there is an improvement made to that initial improvement.”
The current downswing in the construction industry has hit the company’s markets hard. They are working to prepare for when the market turns toward a major growth period again.
“That is why we are so invested in the continuous improvement effort,” DeLeers says. “We want to come out of the depressed market stronger than ever and ready for any challenges ahead of us.
“Our end goal is always to be a low-cost high-end provider for our customers.”
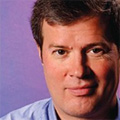
Karl D. Forth is online editor for CCI Media. He also writes news and feature stories in FDMC Magazine, in addition to newsletters and custom publishing projects. He is also involved in event organization, and compiles the annual FDM 300 list of industry leaders. He can be reached at [email protected].
Have something to say? Share your thoughts with us in the comments below.