O'Hair Shutters Ltd. makes solid wood interior shutter panels and the profiles that its customers use to fabricate pre-hung, pre-finished, ready-to-install shutter units.
O'Hair makes about 1,000 shutter panels a day with a lead time of about seven days, and plans lead time reductions with a new MRP system.
The Lubbock, Texas, company employs 225 people with 300,000 square feet of indoor space in several buildings on a 40-acre plant site, and plans further improvements in its facilities and processes. Here's a summary of steps they've taken and plan to take to improve.
Step 1: Management
O'Hair does things carefully, operating debt-free, even during expansions and capital equipment purchases.
"I believe that most millwork companies are limited in their growth by their capacity to manage," says company president Brant O'Hair.
"What can we buy in a capital expenditure that saves management time? We're not using automation just to save labor, but more importantly, to save management time.
"We've learned from our mistakes. We've bought machines without a proper background study to find out about mechanical serviceability, or we've bought machines where parts availability or service technician availability isn't right. These purchases end up not saving as much labor because runtime isn't what it should be.
"But worse than that, these purchases end up taking your most valuable resource your management time. When you look at it from the standpoint of management time, in many cases you should spend a little more money to get a better machine from a better company, where you know you're going to have fewer headaches."
Step 2: Product characteristics
O'Hair uses an edge-grain edge-glued process. Before moulding stile and louver profiles, cut stock is ripped into strips, then rotated and glued back together. O'Hair says that their stiles are edge-grain edge-glued for straightness. For louvers, it's a function of straightness plus minimal telegraphing of the glue lines, since louvers in a window are backlit by the sun.
For product assembly, O'Hair uses a mortise-and-tenon joint design for maximum glue surface area. Wet-to-wet glue application plus assembly screws are used to improve joint strength. Louvers pivot on monolithic tenons formed from the louver profile itself, providing a stronger pivot design.
Step 3: Special drying
O'Hair's manufacturing process begins with lumber drying, then rough milling, moulding, priming, component processing, assembly and shipping. There is no finish coating process.
"We dry lumber very well," O'Hair says. Open air drying and low-temperature kiln drying are used in a process that takes two to three months. "We have a large stack yard, and we keep lumber there for six weeks to air dry, then two weeks in the blow boxes, if needed," O'Hair says. Then lumber spends a week in the dry kiln at 120F. During the west Texas semi-arid summer, air drying is more effective, so kiln drying can be reduced to a three-day equalization cycle. "With proper drying, we get very stable lumber. After edge-grain edge-gluing, we can mould straight, very stable stiles and louvers for panels up to 11 feet tall and four feet wide." All shutters are made almost entirely of cottonwood, a species that O'Hair says paints and stains well. "Actually, it's a white poplar with few knots and lots of FAS cuttings. It's hard to use in millwork, but we've specialized in it." O'Hair has concentrated on this species, overcoming difficulties in its usage to take advantage of the stable supply and reasonable cost.
Step 4: Rough mill
The Weinig Powermat 1000 is new and is used to prepare for edge-gluing. "Edge-grain edge-gluing is key to stile and louver straightness, and accurate preparation of the glue modules is key to good edge-glue joints," O'Hair says. "Thickness accuracy through the Powermat is a big deal, and that's why we bought the machine. Two top and two bottom heads minimize thickness variations for uniform glue module width."
There are eight Weinig moulders in the Lubbock plant, including five Profimats and two Unimats. A Western fingerjoint line is part of the operation. "Fingerjoints have been mismanaged in millwork to the point they have a connotation of poor quality for consumers," O'Hair says. "You don't have to do a lot of fingerjointing with our lumber species, but on a high-end product like shutters, you better do it well."
The rough mill also improved lumber yield with a Weinig ScanCore board scanner and Raimann ProfiRip ripper.
"We experienced an 8 percent increase in rip yield (with this system) over the previous fixed-arbor setup," O'Hair says. "Much of the gain came from the utilization of a random rip range that we face-grain edge-glue for rail material. Our gain also came from eliminating ripper operator error."
Also in the rough mill are a Timesavers rough mill planer, SRT RF glue line, Rosenquist RF tunnel and Barr-Mullin optimizer saws. Chop optimization is currently using old technology fluorescent crayon manual marking and a camera that reads the fluorescent marks on knots, splits, end checks and other defects in the rips.
"We have a new chop system on order, including a LuxScan defect scanner that will replace two marker personnel and improve defect accuracy for better yield," O'Hair says. "A Lux-Scan color scanner will identify, categorize and mark stain-grade material at the same time. This will eliminate six color grading personnel. Two Grecon/Dimter saws fed by the scanner will increase our cutline capacity."
Step 5: Manufacturing upgrades
In addition to the rough mill, there are several areas that O'Hair has improved or modified. O'Hair uses twin-table CMS routers for component processing, including gang tenoning stacks of louvers backed up against one another.
"Most shutter manufacturers will finish cut a louver moulding to length and then drill a hole to insert a nylon pin," O'Hair says. "But there's an inherent weakness in drilling into the end grain of the wood. Our monolithic tenons, formed right out of the profile, are more than twice as strong. This part of our design makes our product suitable for commercial installations like hotel lobbies and guest rooms where from rough handling, plastic pins are broken or the end grain breaks around the pin."
O'Hair is using three Anderson Stratus SUP four-axis machining centers to process stiles with routed mortises, drilled pivot holes and drilled assembly screw holes. The machines are online to the network and receive their make-to-order instructions from the MRP software. One side of the stile is routed and bored, and then the machine automatically flips them over to be bored on the other side. These three machines process as many as 250 different setups a day, all by computer control.
"I believe we'll be using more of that type machine, probably from Anderson, which has turned out to be a good vendor. We'll have other applications in the future, like nested end-rail processing," O'Hair says.
Also, two Accu-Systems machines are used for trimming tenons after the final sizing of end rails.
O'Hair also makes Z-shaped profiles by moulding a single rectangular piece while sawing out a corner, leaving an L-shape and, afterward, re-attaching the corner as a stop-form completing the Z. "The design was done internally to reduce the cost of Z-frames," O'Hair says. "The key to our Z-frame production is precise moulder setup using thin kerf moulder saws followed by specialized RF gluing equipment from SRT to speed the glue curing of the Z-shape without damaging the moulded surfaces."
O'Hair has BeA Fasteners Inc. high-capacity modular staple guns jig-mounted in proprietary production equipment that has increased productivity. "The main benefit we've gained from the BeA reloader guns is longer runs between reloads," O'Hair says. "We put 20 sticks of staples in the hopper and the gun reloads its own magazine. We can run a lot of product through without stopping to re-load the hopper." They use a glue-coated 304 stainless steel staple, made by BeA in Germany. O'Hair's in-house machine shop builds many precision parts for the unusual equipment O'Hair has designed for its manufacturing processes.
For flat surfacing of mouldings, O'Hair uses three Timesavers 200 sanders, one Timesavers abrasive planer and two Fladder denibbing machines modified to do a grain erosion process that O'Hair calls Sandbrushed, a trademarked name. "Material got caught in the Fladder one day, and it had some interesting grain erosion, discovered by accident," O'Hair says. Equipment was then modified to be more aggressive to achieve this effect on a production basis. Cottonwood is the right hardness to allow the soft grain to be eroded, leaving the harder grain lines elevated. About 90 percent of shutters are sent out primed and sanded, including 10 percent Sandbrushed, leaving another 10 percent uncoated. The priming area includes a Delle Vedove vacuum coater line and a Superfici flatline. O'Hair went to UV-cured priming about five years ago.
"More and more we aspire to supply all sorts of services to help our dealers be successful, beyond just being their millwork supplier," O'Hair says. "We're now a vendor of software and retail marketing support. That's what it will take in the future. With cheap labor products from southeast Asia and their improving quality, we better be more than just a vendor of a millwork product line."
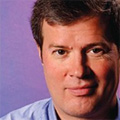
Karl D. Forth is online editor for CCI Media. He also writes news and feature stories in FDMC Magazine, in addition to newsletters and custom publishing projects. He is also involved in event organization, and compiles the annual FDM 300 list of industry leaders. He can be reached at [email protected].
Have something to say? Share your thoughts with us in the comments below.