While woodworkers have long recognized Thermwood as a major player in CNC manufacturing, many probably don’t know the company is also a leader in large scale additive manufacturing (LSAM). This is like 3D printing but way bigger than those little desktop units.
Thermwood routinely applies for patent protection on additive manufacturing technology it develops for its LSAM large format additive systems, said Duane Marrett, vice president of marketing for the company.
“During COVID, we received electronic copies of patents that were granted, however, the official hard copies were withheld,” he said. “A couple of days before Christmas 2021, we received a package containing the official hard copy of 32 additive manufacturing patents. This was certainly a one-day record for Thermwood and a welcome sight!”
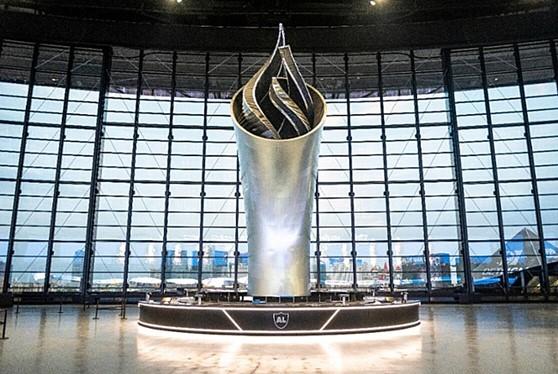
In addition to these latest patents, Thermwood already has a large portfolio of earlier issued patents covering the unique, large format (5x10 foot table and larger) 3D print technology it has developed.
This LSAM technology is currently the most widely used large scale additive print technology operating in industry today, Marrett said. LSAM is used in a wide variety of industries including aerospace, transportation, heavy equipment, foundry and large decorative structures.
“It is being used to produce a diversity of products including aerospace patterns, molds and tooling, heavy equipment foundry patterns, bus chassis, large valve body foundry patterns and trim tooling,” said Marrett. “It was even used to print the tallest 3D printed structure in the world, the 92 foot tall Al Davis Memorial Torch at Allegiant stadium in Las Vegas.”
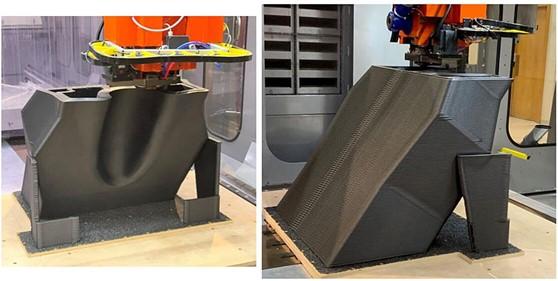
If you are used to relating 3D printing to those desktop units that squirt out melted plastic to form a small object, Thermwood’s machines create an entirely different picture.
“Thermwood offers this unique patented technology on a wide variety of equipment, the largest, most diverse product offering of its kind available today,” said Marrett. “It includes a broad selection of machines, including single and dual gantry, fixed and moving table configurations, with both print-only and print-and-trim systems, from 5-by-10-foot to 20-by-60-foot print envelopes. They are working on even larger machines but that’s for another day.”

Thermwood says they also offer the highest throughput print heads currently available with maximum print rates from 200 to more than 500 pounds per hour.
The primary focus of the patented LSAM technology is to reliably and repeatedly produce the highest quality, best fused, most homogeneous printed structures possible from a variety of reinforced thermoplastic polymer composites including those intended to operate at elevated temperatures, said Marrett.
“Although it is nice to have been granted these patents, it is even nicer to finally have the official hard copies in hand,” he said.
You can watch a video about Thermwood’s LSAM technology or learn more at thermwood.com.
Have something to say? Share your thoughts with us in the comments below.