The tour began in Berlin, Germany, and over the next five days, more than two dozen representatives from some of North America’s leading wood products manufacturers would tour eight of Northern Europe’s most highly automated factories that produce hundreds of finished goods and thousands of components daily all with a handful — or less — workers on the production line.
The 2023 IMA Schelling Group Technology Tour to Northern Europe, held September 9 to 16 toured manufacturers specializing in cabinetry, office furniture, medical furniture, components, and more.
Week-long tour
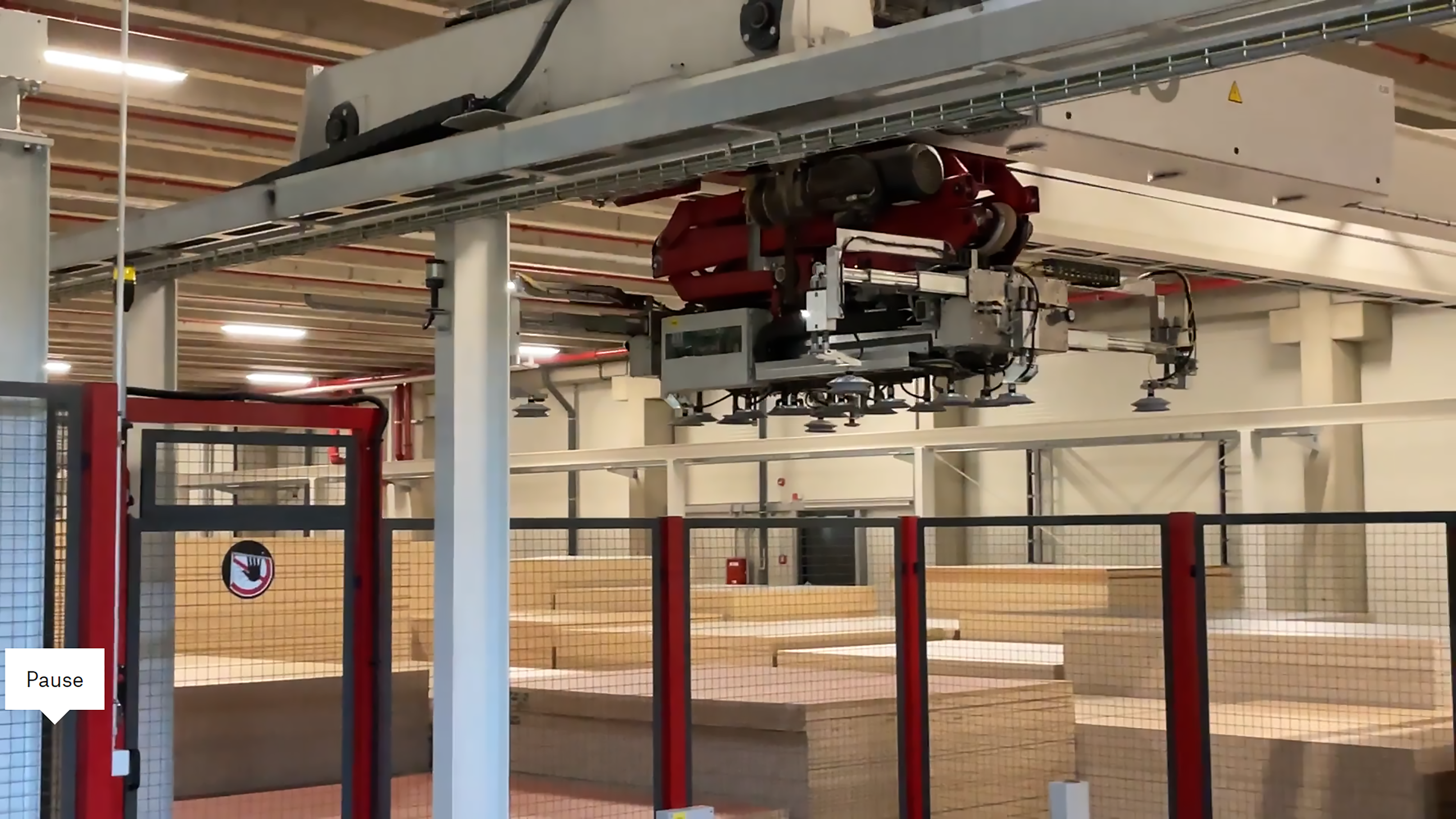
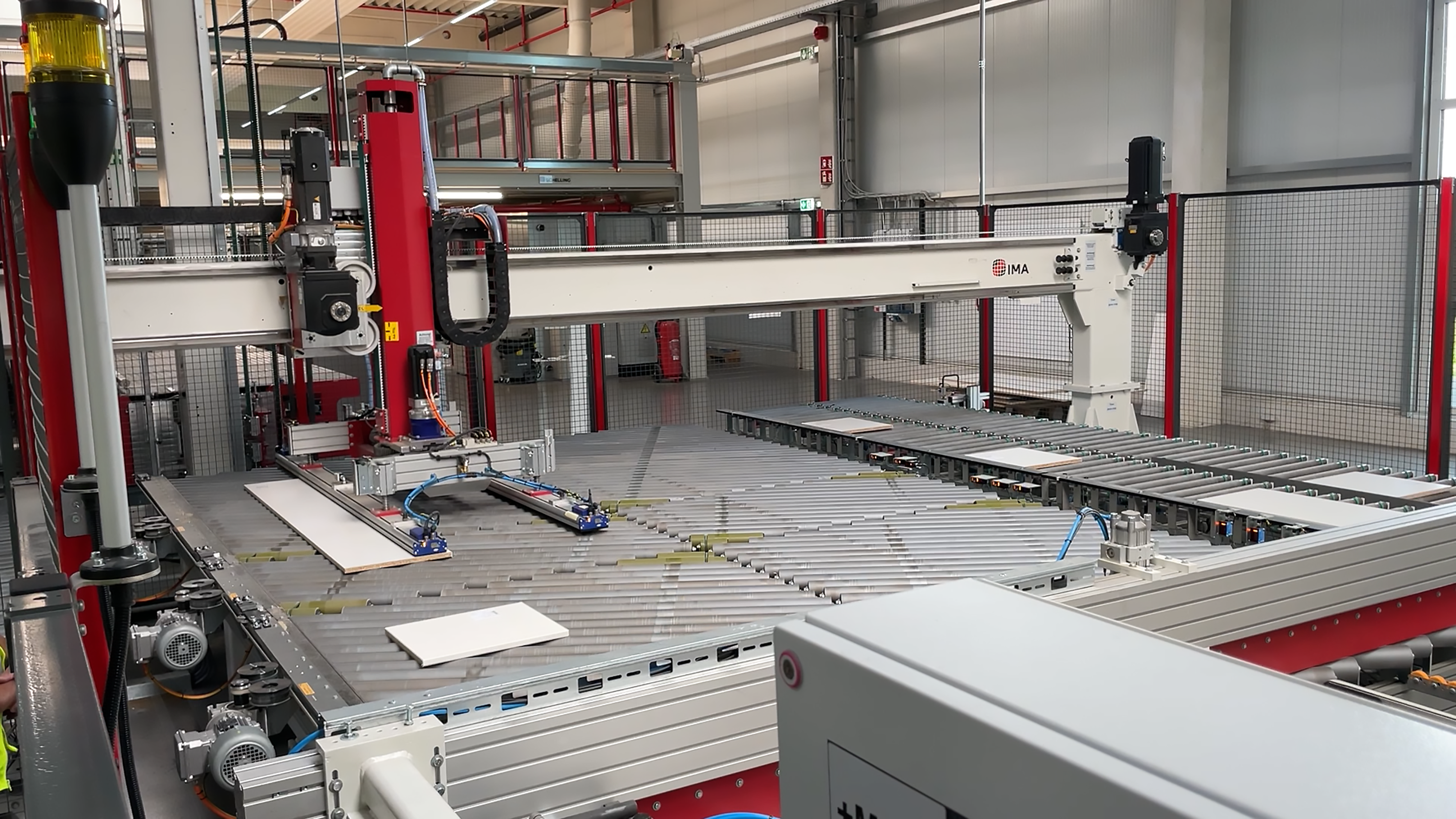
Over the five-day excursion, the tour goers traveled some 600 miles by bus, stopping at the factories and staying at nearby hotels.
Day one of the tour began at the Reiss office furniture factory in Bad Liebenwerda, Germany, and ended at the Porsche Experience Center in Leipzig where attendees got to tour the data-driven assembly plant.
Day two found the tour in Nordhausen, Germany, walking through a Stiegelmeyer factory. At this facility, the main focus for the medical and hospital furniture specialist is wood, and this is where the wooden elements for its beds, bedside cabinets, and contract wood furniture pieces are produced.
From there, the tour traveled to office furniture manufacturer Sedus, which calls itself Germany’s largest office furniture manufacturer. The company produces ergonomic and high-quality office furniture.
The Pronorm kitchen cabinet factory in Vlotho, Germany, is where day three of the tour began. Attendees got to see how unique products with a wide variety of options are made by the thousands every day. In the afternoon, the tour moved to FM office furniture where the tour included a batch size 1 production line.
Day 4 began at Egger in Bunde where high-volume components are made and ended at Assman, Mele, Germany, where its automated and digitized manufacturing lines produce more than 2,500 pieces of furniture every day.
The final day of the tour found the attendees crossing over the border into the Netherlands, where we toured the DKG Group’s 56,000 square meter (600,000 square feet) kitchen factory.
Highly automated
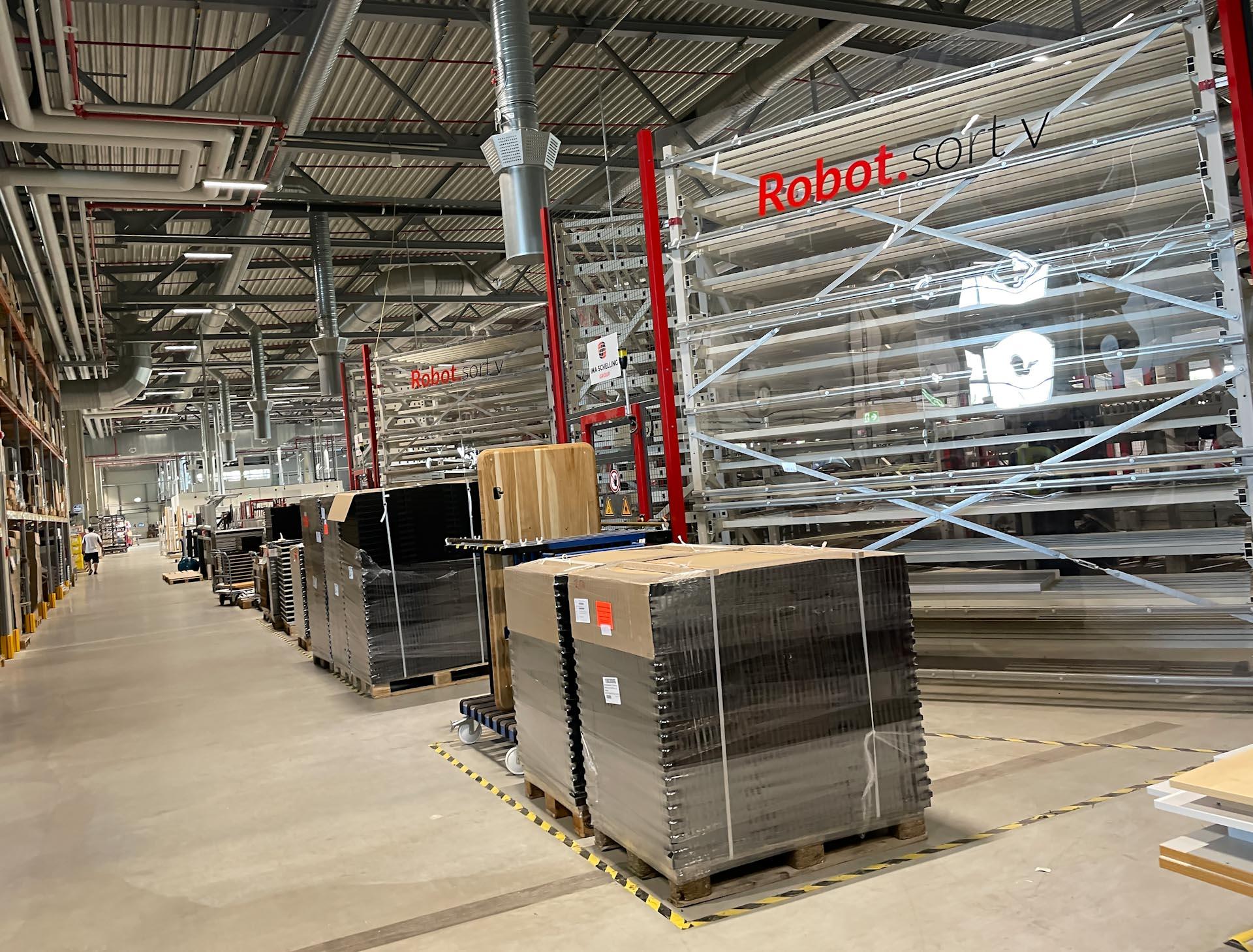
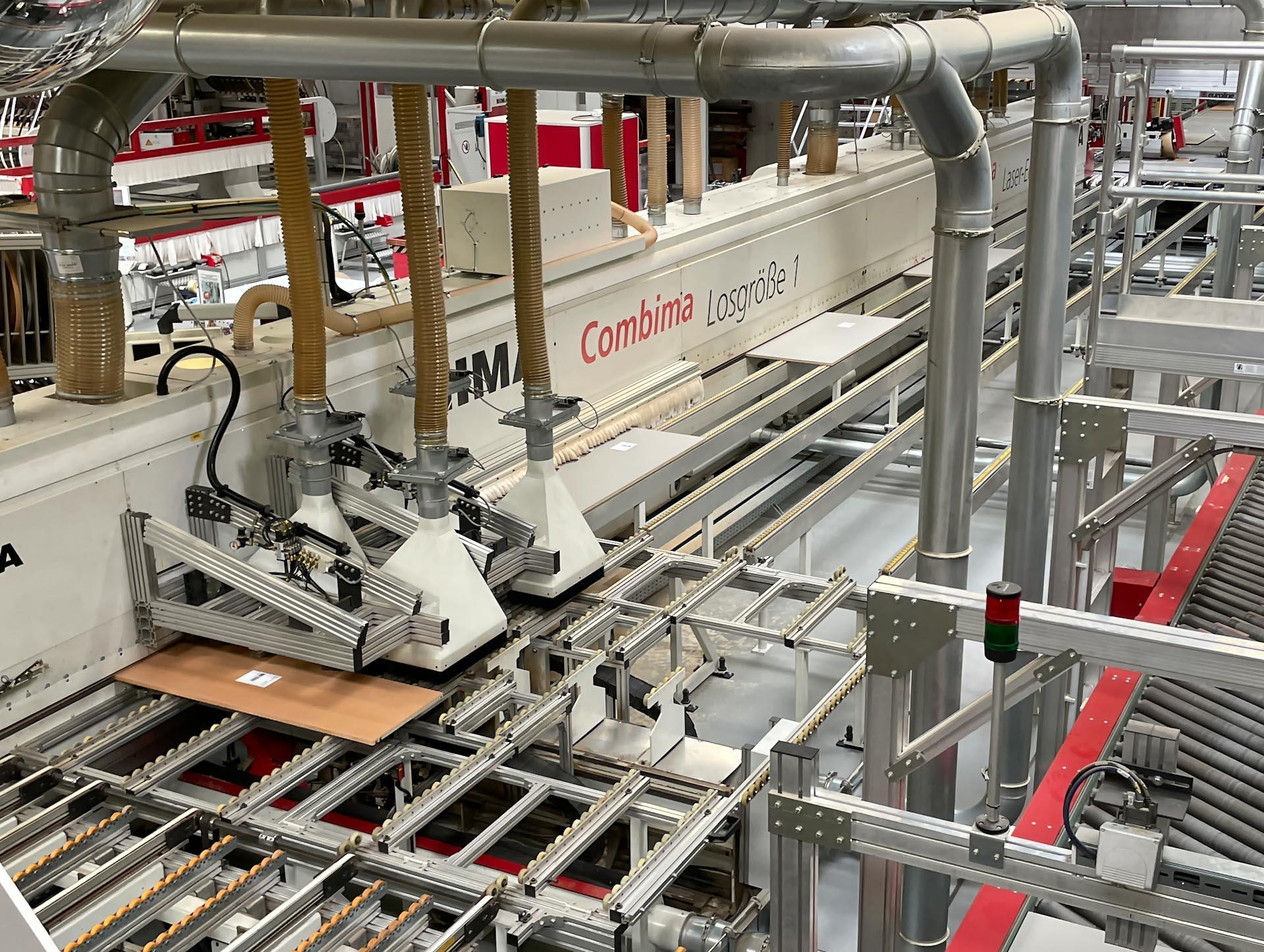
While the products these companies manufacture and distribute are varied, a few things were common between them. Batch Size One production, in which manufacturing is a continuous production process and each batch is exactly one piece, was prevalent with this concept.
The use of manufacturing execution systems (MES) to coordinate production of parts of all sizes and shapes, to sort and sequence as needed, is critical to the process.
In these factories, parts moved at dizzying speeds. Gantry-style vacuum material handling equipment moves panels as needed, when needed, and directs them to workstations all while tracking inventory. Other material handling systems or robots grab parts in the process and place them onto the conveyor systems en route to work or assembly stations as needed.
And, these are not large-run orders in which the facility is producing the same component over and over again. Individual parts run one after the other, often different than the previous and subsequent parts, and an MES system tracks and collects information about each product through all stages of the production process.
Components traveling in line are diverted to different processes as needed. Does the part need drilling, dowel, or other hardware insertion, banding, contouring, or other processing?
The part diverts from one conveyor system to another path. If the product has to wait for processes to be completed because of a backup in production or other factors, the system knows to hold that in queue while different parts flow to where they are needed. Production will continue.
The utilization of material — little is wasted — is another common attribute. While panel yield might take a backseat to production levels, utilizing the material is critical. Wood dust and bits and pieces of wood offal are often burned to heat facilities during the winter.
While similar in overall concept — getting the most product as quickly and efficiently as possible with the fewest workers and the highest quality — each facility did things a little differently. In some plants, for instance, edgebanders were arranged in line with banding applied to one edge, turned, and applied to subsequent edges as needed. Other lines were in a horseshoe or other shapes that allowed the components to run through the banders in the most efficient method possible. Some lines used PUR hotmelts or laser edgebanded. In at least one case, the company used both processes on the same machine in line while the MES informed the machine which to use on which part.
Our first stop
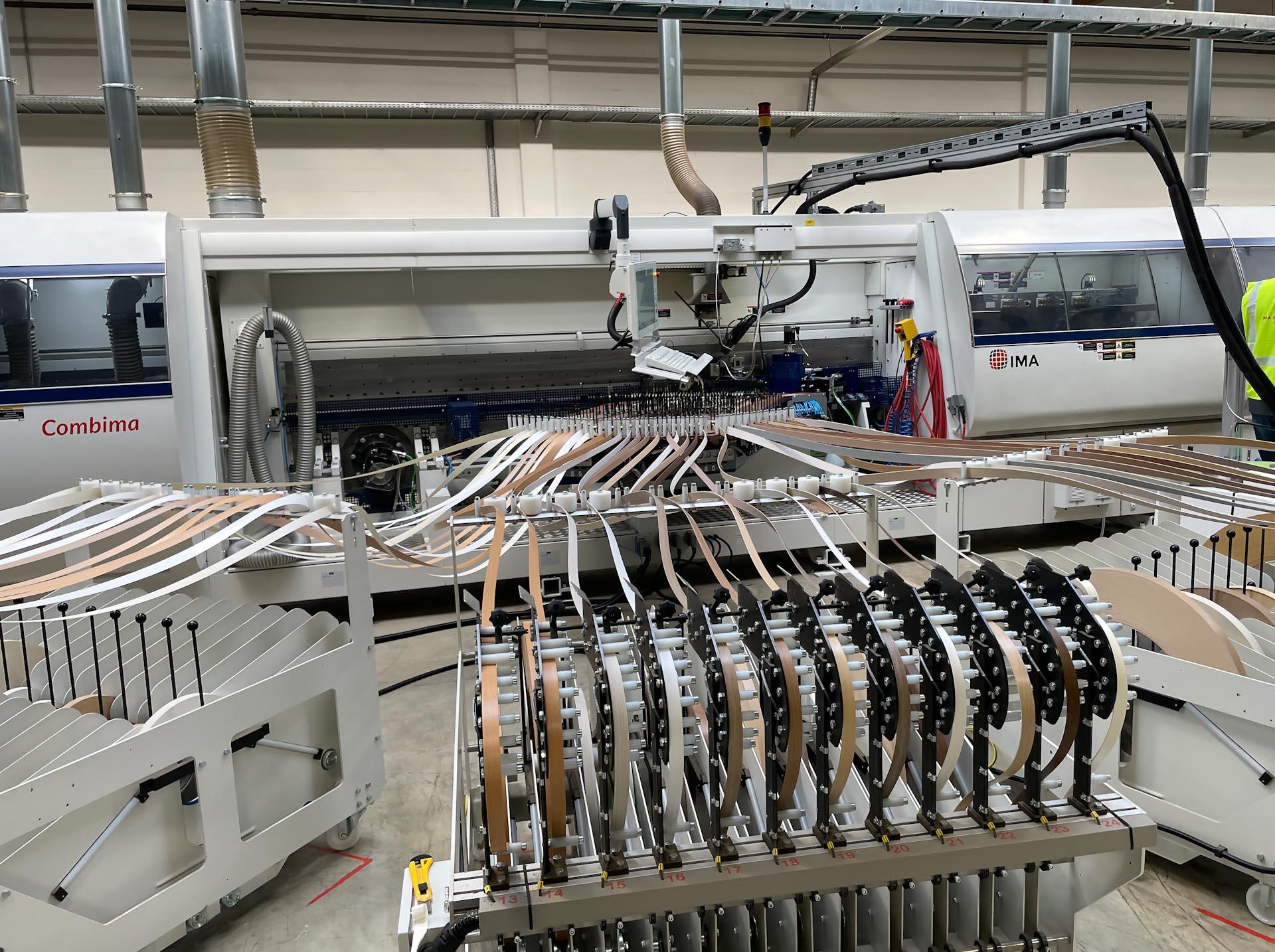
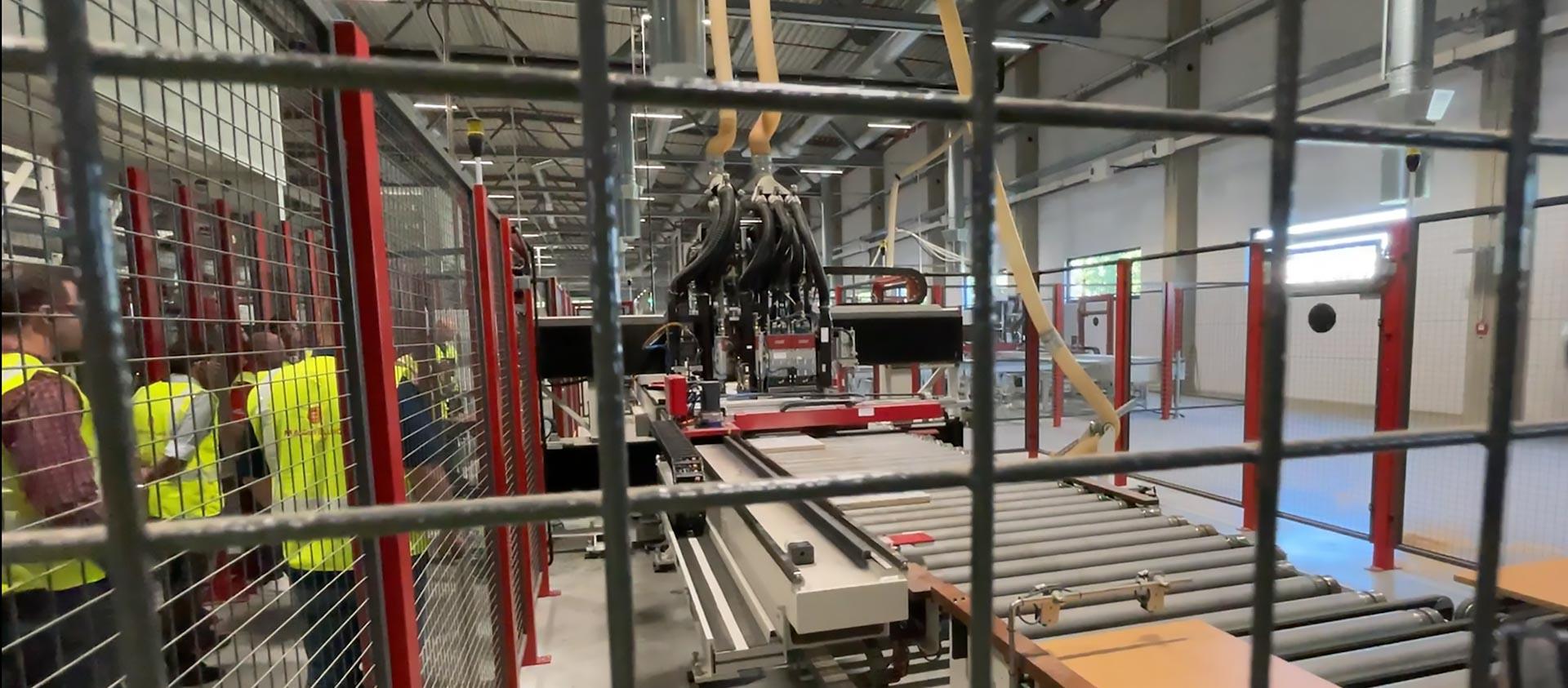
In 2020, Reiss built a new facility expressly for an automated production concept, said Joerg Rosemeier, Export Sales Manager North, Central and South America, IMA Schelling Group Germany.
The facility is 12,500 square meters or more than 135,000 square feet and it has 120 employees, which includes office workers, maintenance staff, assemblers, and production personnel. Of that total, Rosemeier said, two employees worked on the production line and eight workers assembled products. Few parts are ever touched by human hands until assembly and shipping.
Here, more than 50,000 cabinets and 80,000 tabletops are made per year and much of this production is on an individual order basis. It can accomplish this through the highly automated production line.
Geno Plitt, president of Bay View Industries, Oak Creek, Wisconsin, an OEM manufacturer of laminated components for the office furniture, hospitality, healthcare, and institutional markets was particularly impressed. The Reiss production line was a “fabulous representation of IMA Schelling automation from storage retrieval to edgebanding, cutting, and assembly. Everything is just so well thought out, every single detail is thought out.”
Because production has shifted to more individual orders, which means that production must be fast and flexible,” said Rosemeier.
“So, just in time, batch size one, are important {concept} when coming from a production manufacturer to more or less individual orders.
The facility uses a sophisticated storage and retrieval system. Panels are constantly in motion and they are moved by a vacuum gantry system and tracked by the MES. Components are stored via IMA Schelling Robot.sort v. that automatically stores parts in books and retrieves them again through order picking.
The line featured an edgebander that bands using both PUR and laser edgebanding depending on what the MES has determined is required.
Some parts are diverted to a contour edgebander because of rounded shaped components.
Utilizing MES helps to improve efficiency by taking the “air” out of production, said Rosemeier. “What good does it do if you have more air in the machine than wood? I mean, that should be not the idea of it,” he said.
If the next shift requires another component, for example, the MES can drive the production of the next shift’s needed part. “MES gives you the control to create the mix that is needed for upcoming production and assembly needs,” he said. “It doesn’t make sense to have a strong cutting, but edgebanding is running empty or vice versa. Instead, this allows you to put another material into the loop to fill up production, to get the air out.”
Have something to say? Share your thoughts with us in the comments below.